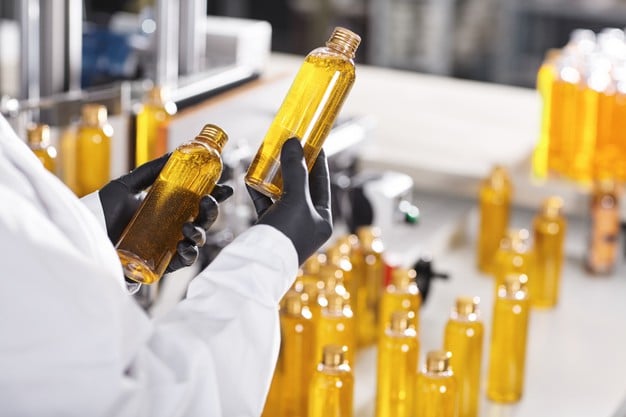
High Pressure Processing (HPP) is traditionally an In-Pack technology, meaning that the products are processed in their final package. A suitable packaging is essential to protect the product against oxidation, spoilage microorganisms and other external agents. Therefore, the right package combined with HPP increases the product shelf-life. In this article we will clarify the most important aspects when it comes to make a decision about the package and how can Hiperbaric help in this process.
High Pressure Processing (HPP) enhances food safety and extends the product shelf-life by submitting them to pressure levels around 400 – 600 MPa / 58,000 – 87,000 psi during 1-6 minutes. HPP is a non-thermal technology, allowing a better preservation of the organoleptic and nutritional characteristics of foods. Whilst delivers a safe product and minimally processed. The traditional HPP process works In-Pack, meaning that the products are already in their final package before processing, avoiding post-processing contamination. Thus, it becomes clear that the packaging plays a very important part, and is a key factor to the success of the process and brand.
Cans, glass, paper-board… could be used for HPP?
Packaging in HPP processing is subjected (jointly with the food) to high pressures using water as a pressurization fluid. Thus, packaging materials must be water-resistant. Packaging is in contact with pressurization water during the HPP cycle. On the other hand, during pressurization, water reduces 15% – 18% of this volume which is recovered when HPP cycle is finished, therefore the reversible response of the whole package to compression is crucial to the success of the HPP processing.
So, packaging materials are required to be flexible enough to withstand the mechanical stress caused by hydrostatic pressure while maintaining physical integrity. Due to their good flexibility, elasticity and water-barrier characteristics, plastics are commonly used in HPP products. Other materials such as paperboard-based, metal cans and glass bottles are not well suited for HPP: They are not able to recover the shape and size after HPP and because of their lack of water and pressure resistance. Despite this requirements, it is worth mention, that there are already several options for HPP biodegradable packaging, based in plastics that naturally decompose in the environment.
Hiperbaric also offers a breakthrough innovation, the In-Bulk Technology, which allows to process beverages in bulk, that is, before bottling. Contrarily to the In-Pack process, this technology allows the use of any kind of packaging for HPP beverages.
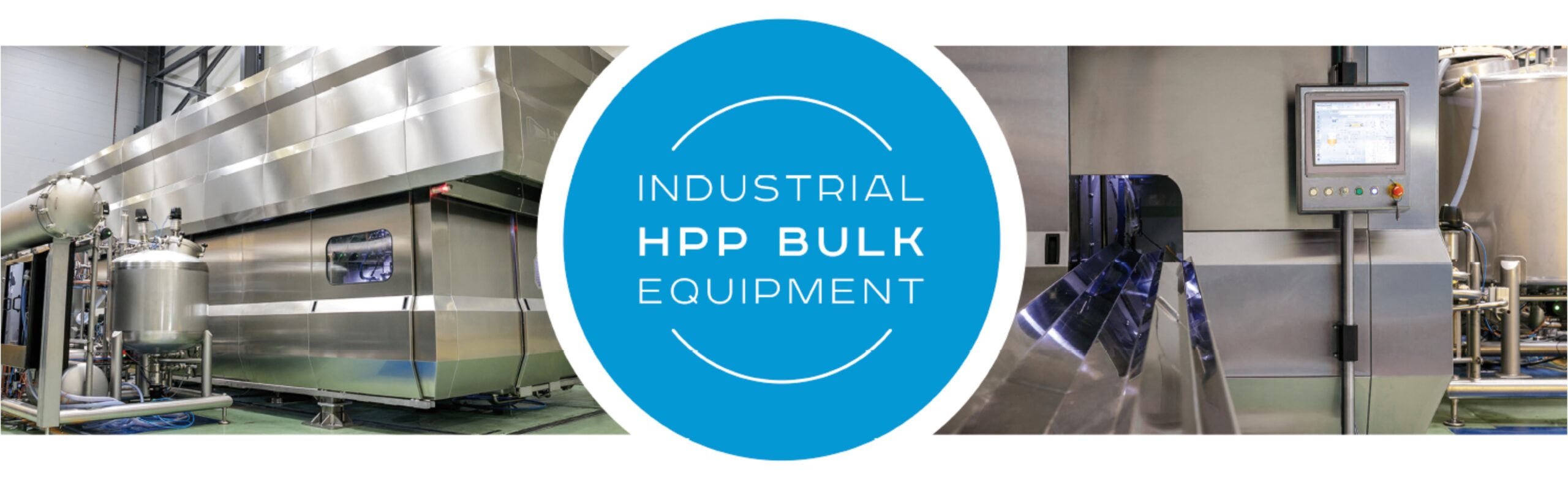
What polymers are HPP suitable?
The performance of plastics under HPP conditions are widely described in literature. Juliano and collaborators and Caner and collaborators summarized the effect of HPP on polymeric materials. They provide a valuable tool for preliminary selection and evaluation of polymeric-based materials for HPP. Also, Hiperbaric encourages testing each packaging at actual/expected HPP conditions in order to assess the suitability of the materials for each food product. In addition, Hiperbaric offers support in this area, since we offer a pilot plant for trials, which can be used to assess the suitability of the packaging.
Besides good mechanical, sealing and barrier properties, all packaging material in HPP products must fulfill national or regional regulations about food-contact materials and migration. Food and Health authorities from Europe, USA, Canada and other countries offer guidelines and further information about this topic. Also, among other studies, Luis and colleagues have recently assessed the migration of a chemical compound from the package towards the food matrix after HPP. They were able to conclude that the compound migration rate with HPP was below the regulatory limits stablished, and also, lower when compared to the result obtained for thermal processing.
The shape and size doesn’t matter in HPP technology
In HPP, pressure is transmitted instantaneously and homogenously throughout the food product, regardless of the size and geometry of the product. The latter makes HPP technology suitable for processing different kind of food products in different types of packaging such as bottles, pouches, trays, cups, bags (even big bags for foodservice market). Please see below a resume table that shows different options of packaging along with the recommended materials.
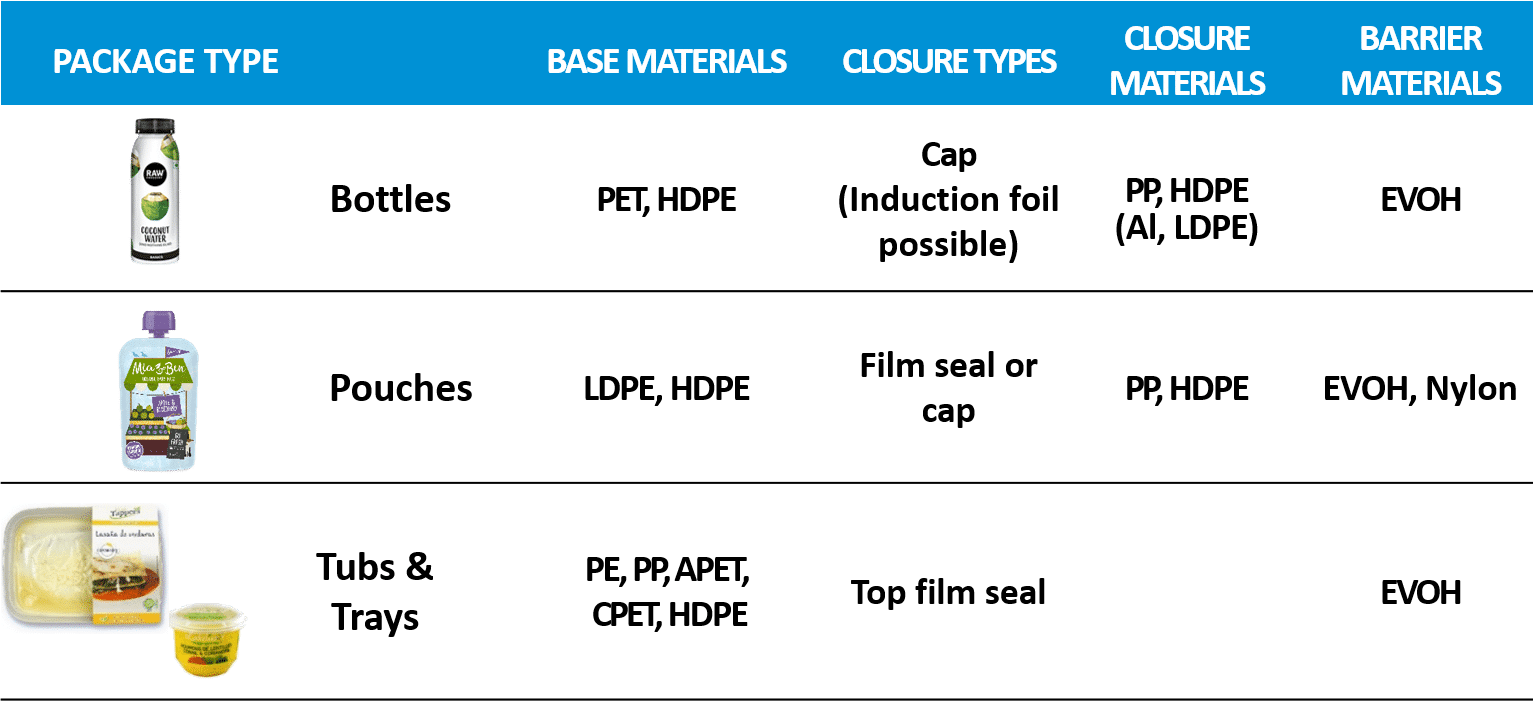
… well, actually they do
Since the technology is effective despite of the design of the packaging (good news for design and marketing teams), size and shape play a relevant role in productivity. The productivity in HPP is closely related to how many products can be processed per time unit (the more, the cheaper… the better). The quantity of product to be processed in each batch will depend on packaging design, as well. Thus, packaging design will play a primary role in marketing and production decisions, influencing on product’s convenience and attractiveness to consumers and on filling ratio (the proportion of volume of product in one batch divide by the capacity of HPP machine). The higher filling ratio, the higher HPP production per cycle.
What happens with MAP in HPP?
Modified atmosphere packaging (MAP) is a technique used in order to improve shelf-life of foods by replacing air with other gases such as nitrogen, carbon dioxide and carbon monoxide, or their mixtures. Sometimes consumers perceived MAP-packaged food products as fresher, being processed by HPP, as well. The synergy between MAP and HPP remains unclear and strictly product-dependent. However there are available MAP-packaged products processed by HPP in market around the world, mainly meat products, but this choice is mostly made on marketing/product presentation decisions.
Due to the fact that gases are very compressible under high pressure, more headspace involves lower productivity in terms of kg per hour, because part of the volume is occupied by gases which must be compressed. On the other hand, the higher headspace the bigger deformation strains on the packaging materials. Hiperbaric recommends keeping headspace as small as possible.
Hiperbaric considers packaging an essential part of the success of HPP technology, impacting directly on marketing, productivity and product’s acceptance of HPP products. We will be pleased to support you throughout packaging selection and the design of your HPP products.