Aeroespace
In its production phase, the aerospace industry is mainly characterized by three key aspects: high annual investments in R+D; significant production costs with very long term returns and rigorous quality and safety controls of components. The agents involved in the development of this strategic sector point out the need to invest in advanced manufacturing technologies to guarantee, on the one hand, the reliability of the design and manufacture of aircraft and, on the other, the increase in the competitiveness of companies by reducing their life cycle costs.
Hot Isostatic Pressing (HIP) is a technique applicable to engine and structural components of airplanes, helicopters, satellites, rockets, etc., which guarantees compliance with this requirement.
HIP applications in aerospace: parts, materials and techniques
The aerospace industry is seeking to design and manufacture lighter, stronger components that will help increase the efficiency and environmental impact of aircraft, as well as reduce process costs. To do this, it uses a wide range of production techniques, including Additive Manufacturing (AM), advanced Diffusion Bonding (DB) techniques and Metal Injection Molding (MIM).
These manufacturing techniques are often used in combination with Hot Isostatic Pressing, not only because it allows the development of materials with exceptional mechanical properties, such as Metal Matrix Composites (MMC), but also because it helps to reduce raw material and thus production costs.
Examples of aerospace parts manufactured using HIP include turbine rotor shafts, jet engine turbine blades, engine and turbine casings, small hardware and supports, and seat anchorage structures.
The most commonly used materials in the aviation industry include: Nickel-based super alloys such as Inconel (IN718/IN625), low weight Titanium alloys (Ti64, TiAl) or Cobalt-Chrome alloys (CoCr).
Since the introduction of the Additive Manufacturing (AM) processes in the aviation industry, the HIP treatment has become even more important as this manufacturing method often produces an internal porosity that has to be treated by HIP. The most common additive manufacturing techniques currently used in this sector are L-PBF and EBM.
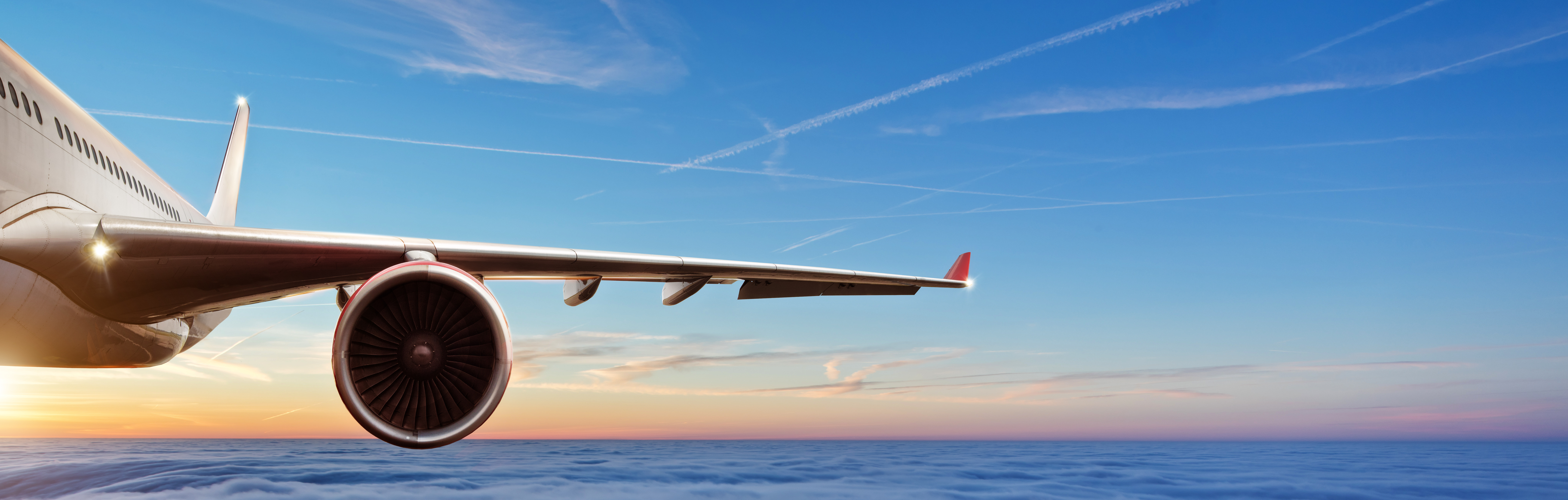
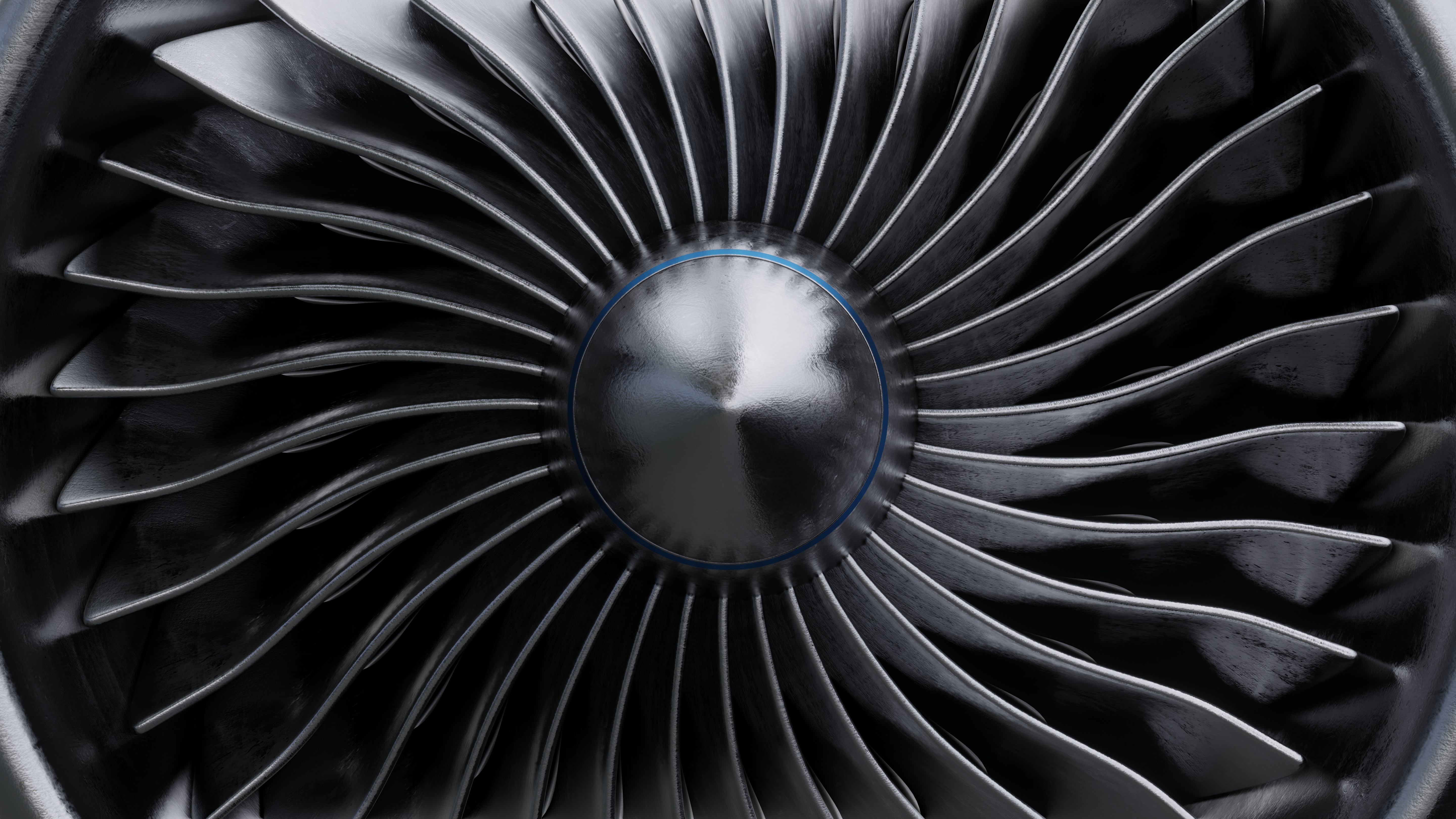
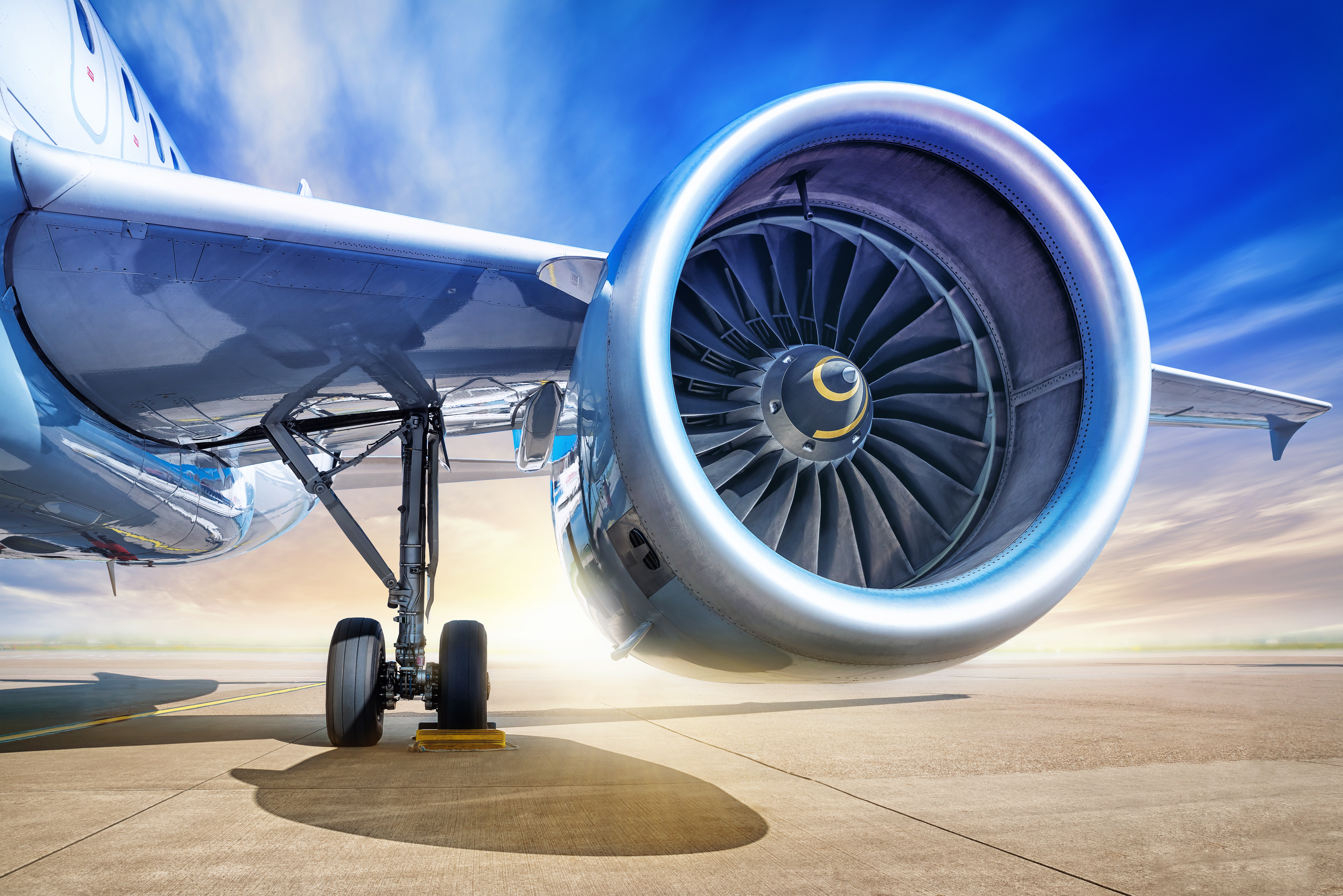
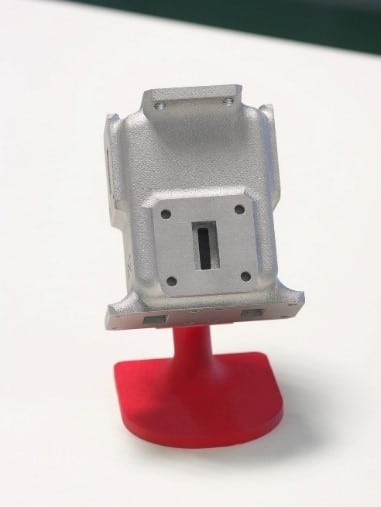
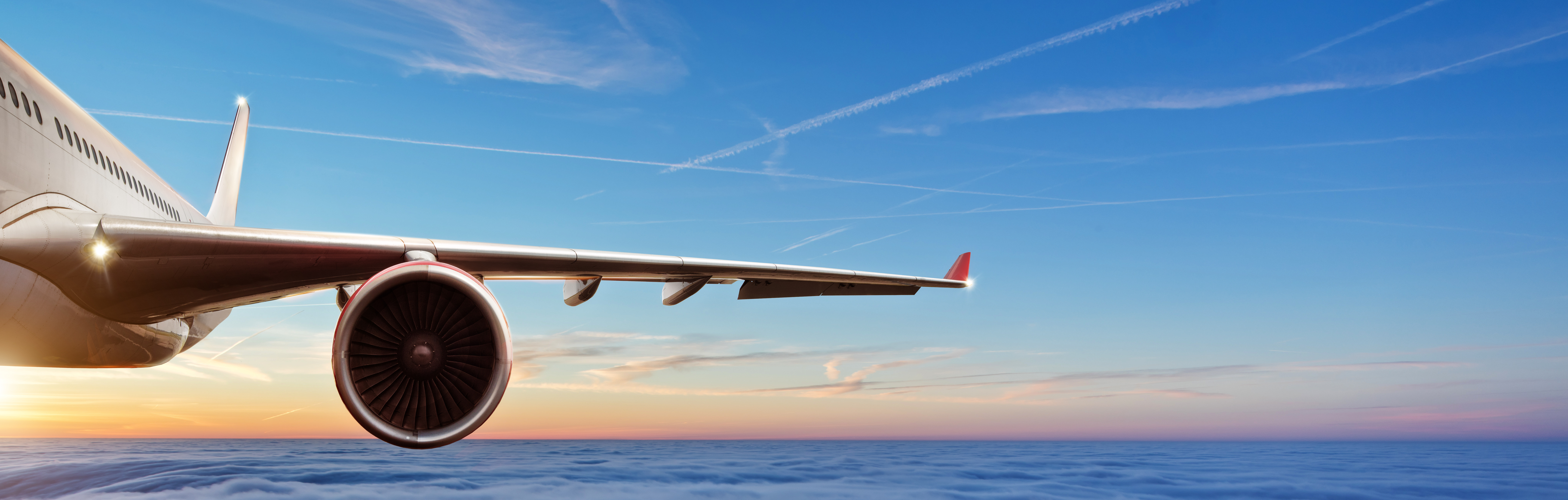
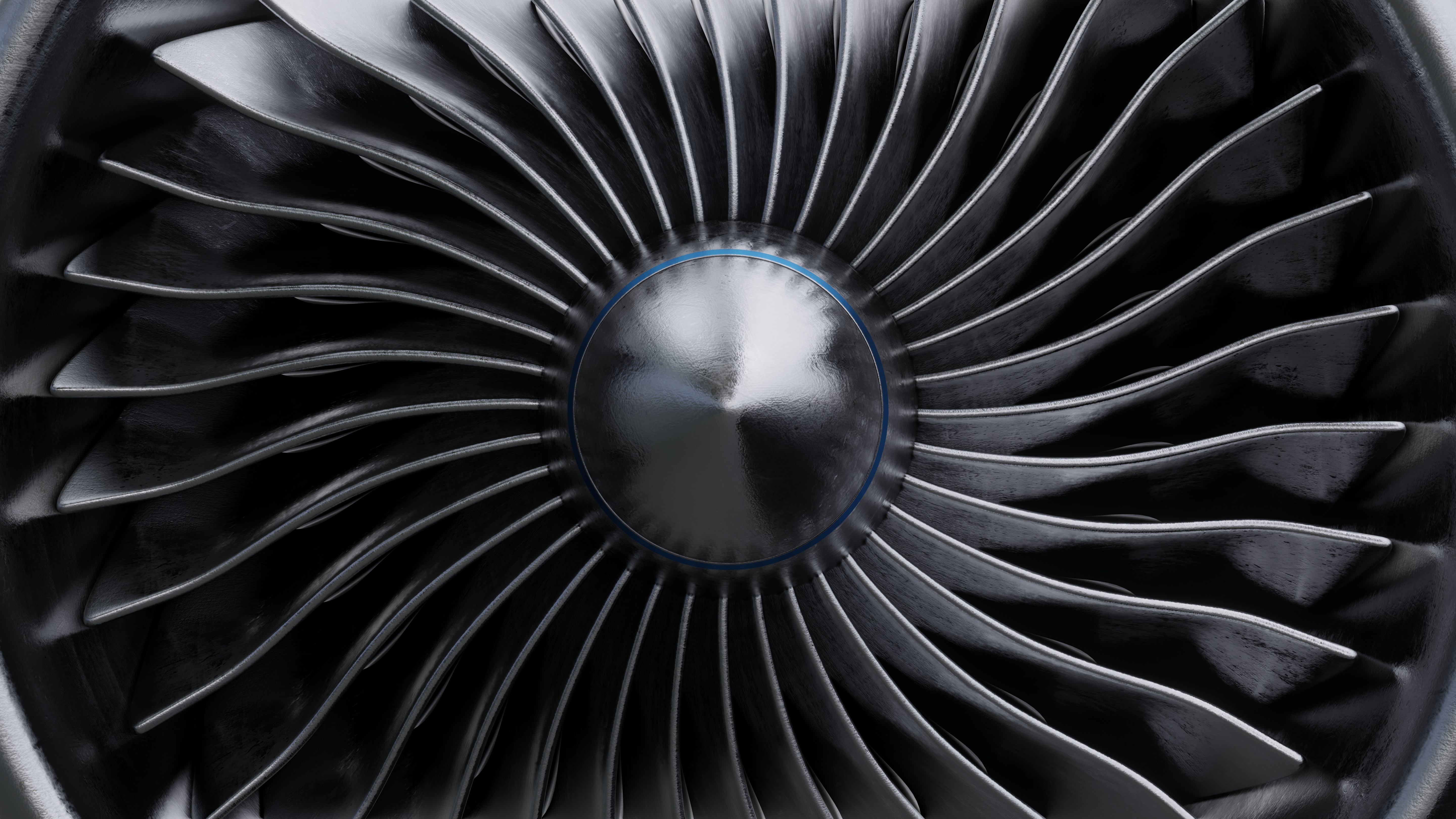
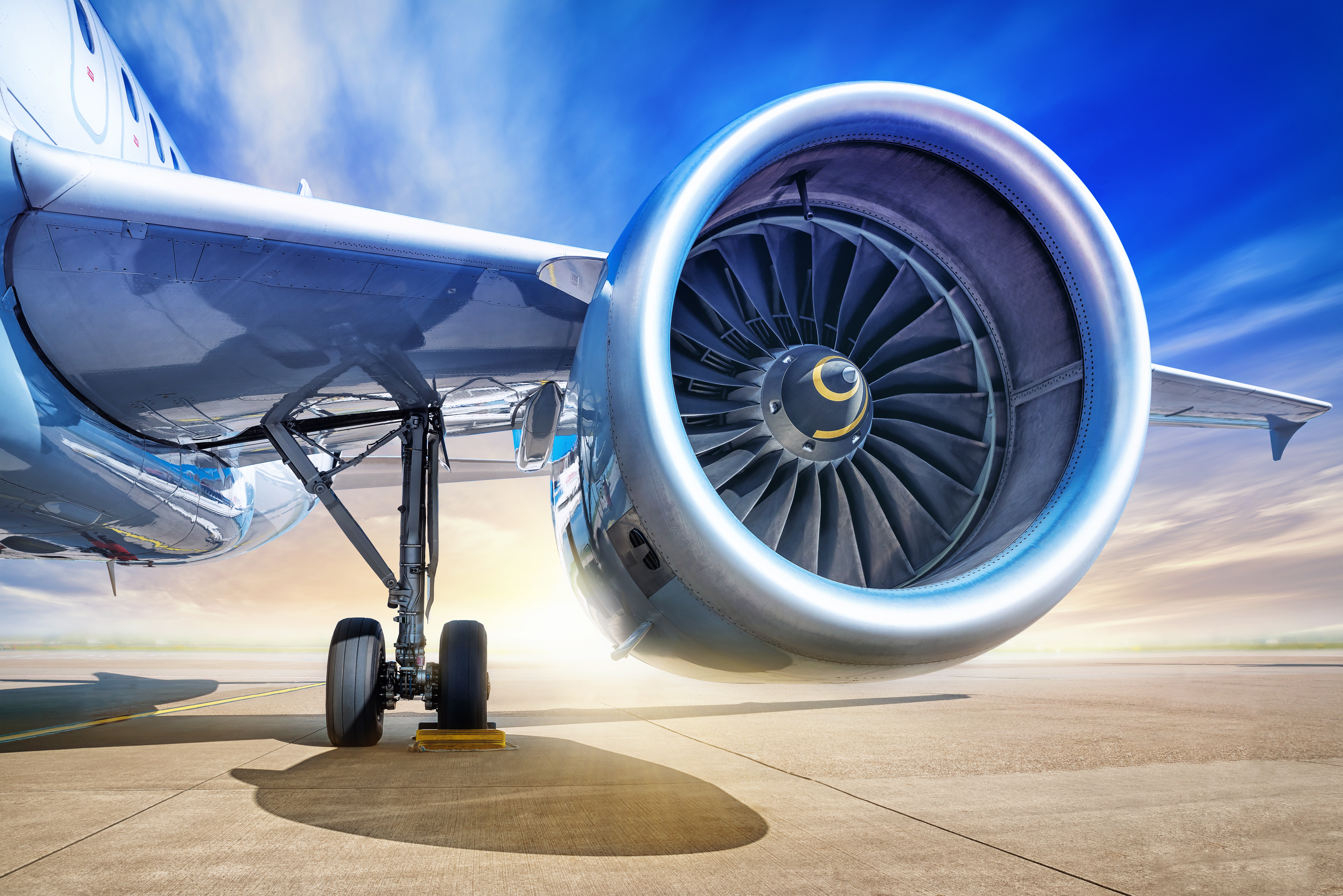
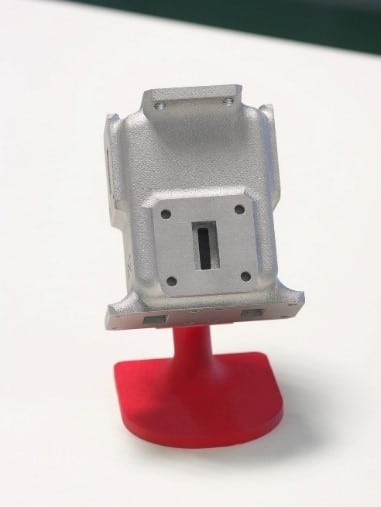
MAIN BENEFITS OF USING HIP IN AEROSPACE SECTOR
The main advantages that HIP brings to the components of the aeronautical sector are the following:
Improved mechanical properties:
- Increases fatigue strength, ductility, toughness and resistance to stress rupture.
- In diffusion bonding, in addition to welding similar or non-metallic surfaces, without filler materials, it improves the mechanical performance of the part by eliminating casting porosity and obtaining a homogeneous granular structure throughout the part.
It reaches 100% of the theoretical density:
- Facilitates machining and improves surface finish.
- Eliminates internal porosity, an essential element to maximize the properties and life of the components.
- Improves the X-ray standard.
- Reduces spreading properties.
More efficient production in manufacturing processes:
- Reduces the rejection rate.
- Reduces scrap losses when repairing porous castings.
Cost reduction
- Casting performance is significantly improved, resulting in lower costs and more effective use of raw materials.
- Reduces welding repair.
- Restores components, extending their life.
Certificates
The main standards and certificates required by the aeronautical sector are the following:
NADCAP AC7102/6 (HIP's TT standard)
DIN AS/EN/JISQ 9100: Quality Management System for Suppliers for the Aerospace Industry
Airbus, BAE Systems, Boeing, GE, Honeywell, Messier-Dowty, Pratt & Whitney, Rolls-Royce, Smiths and Snecma.