Casting
Casting has been a manufacturing process for a long time, but it is still very relevant today. There are many casting techniques, but the basic method consists of pouring molten material into a mold where it solidifies to obtain the final shape.
Many industries such as aeronautics, shipping, automotive or heavy machinery manufacture components of their products through a casting process because it allows relatively complex geometries to be obtained in a simple way once you have the mold. It is particularly suitable as a manufacturing process for large batches and for large sizes in general.
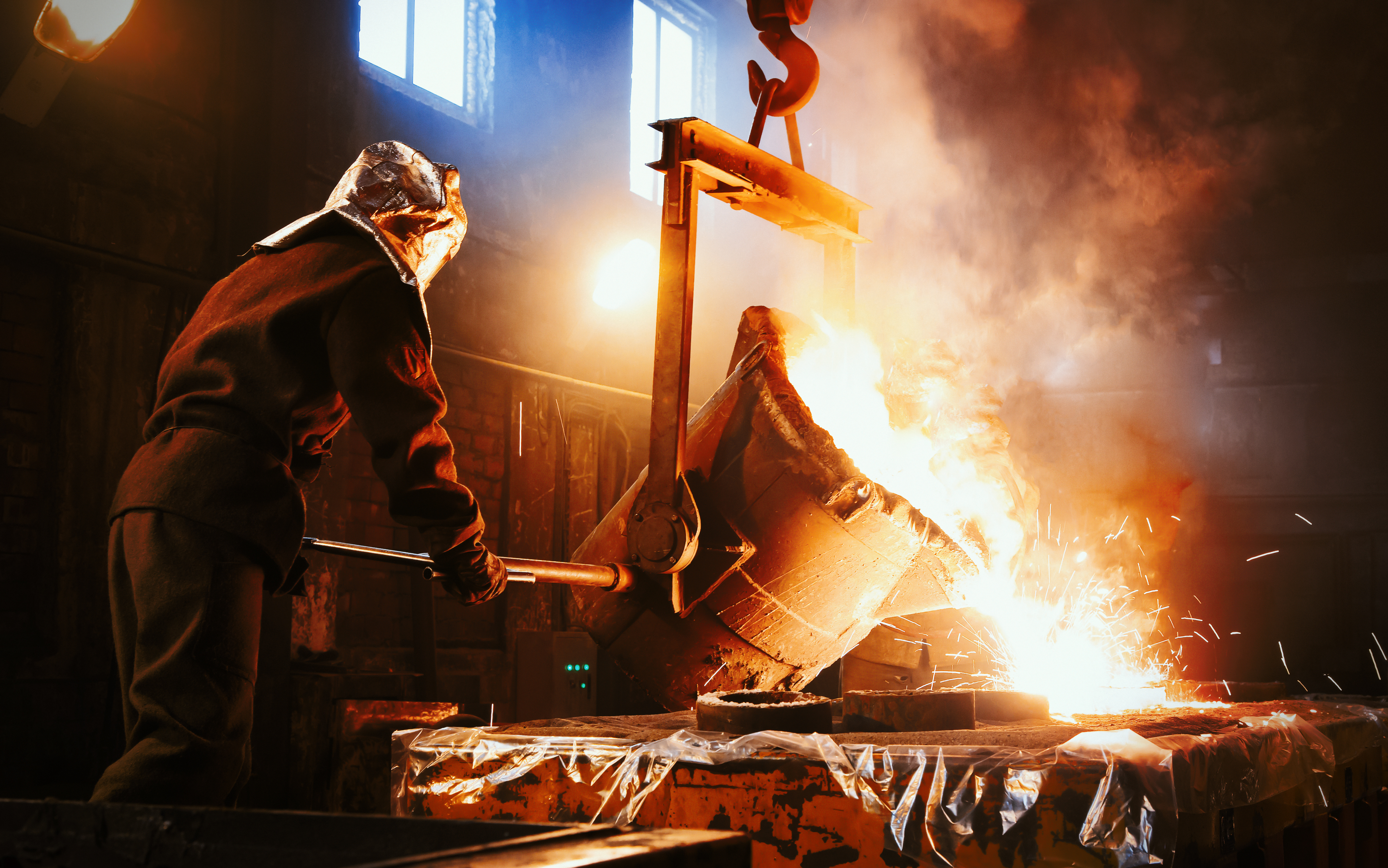
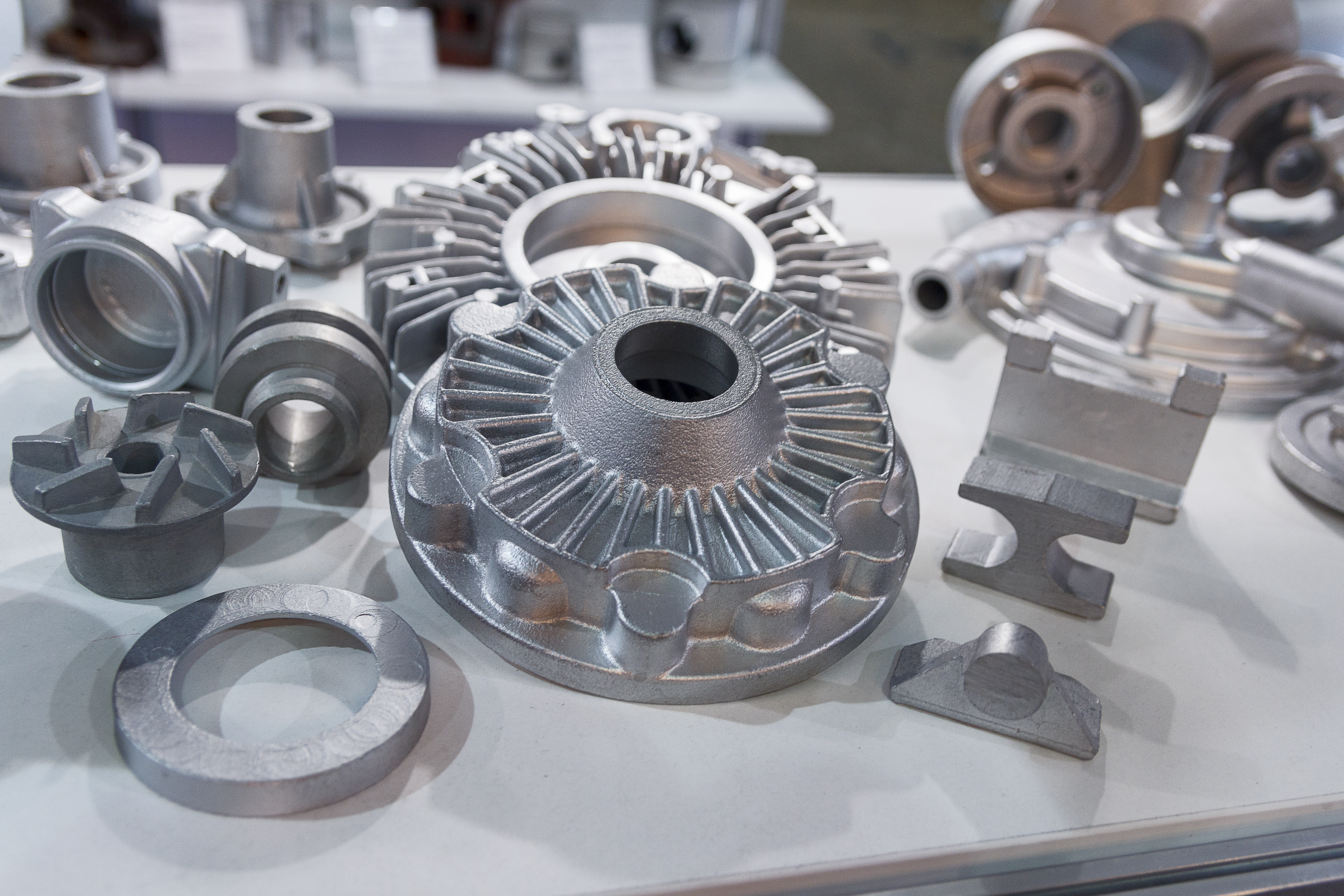
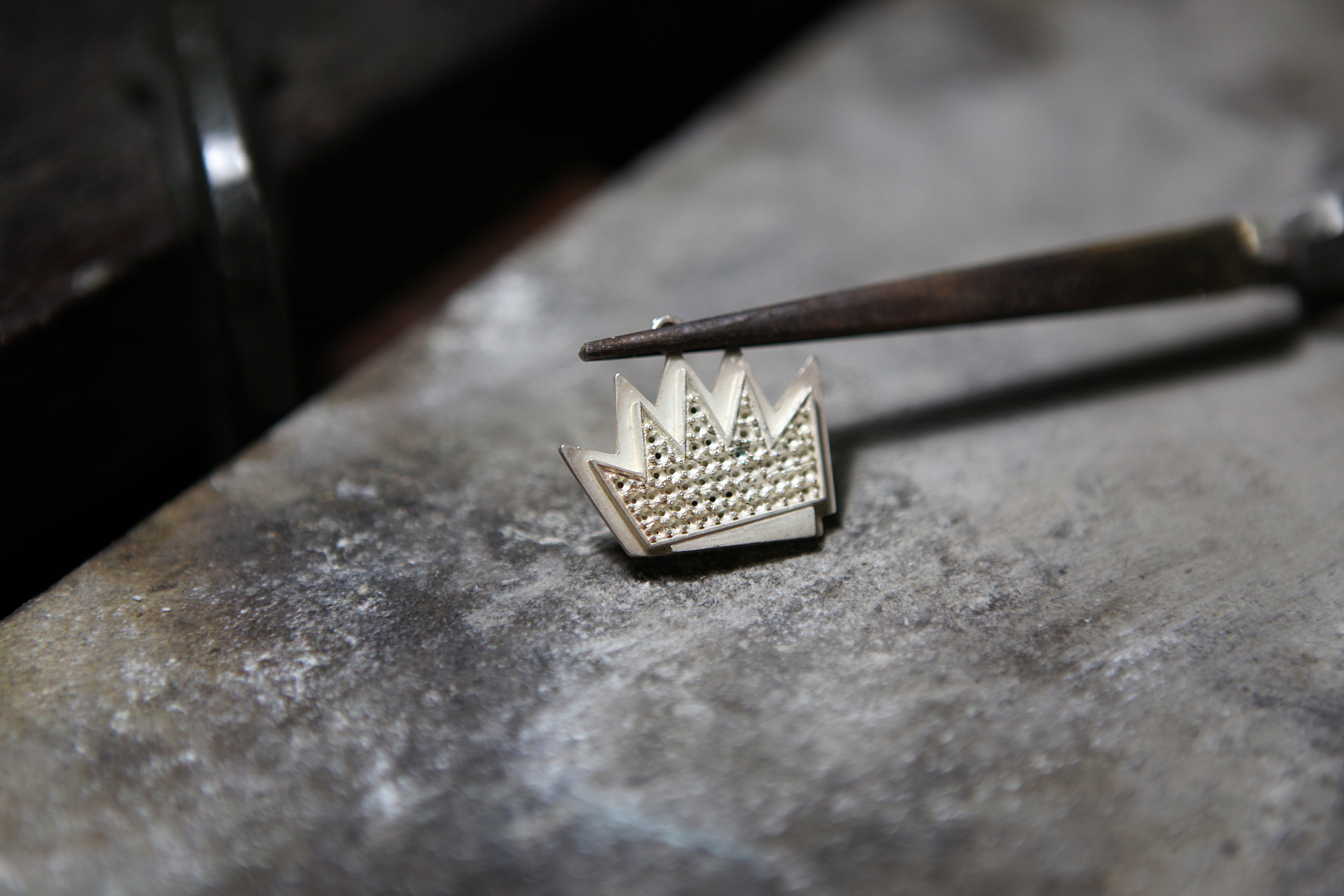
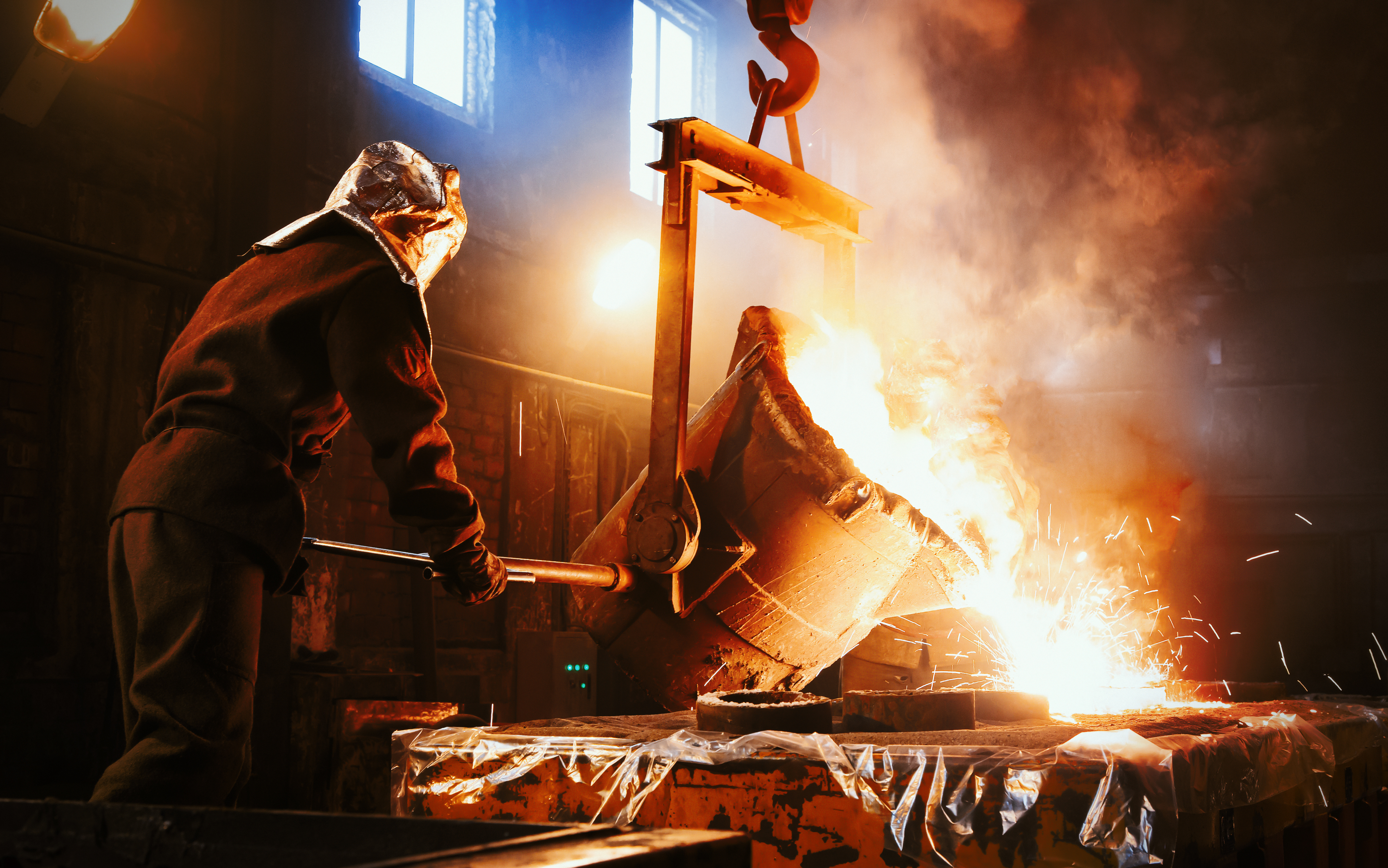
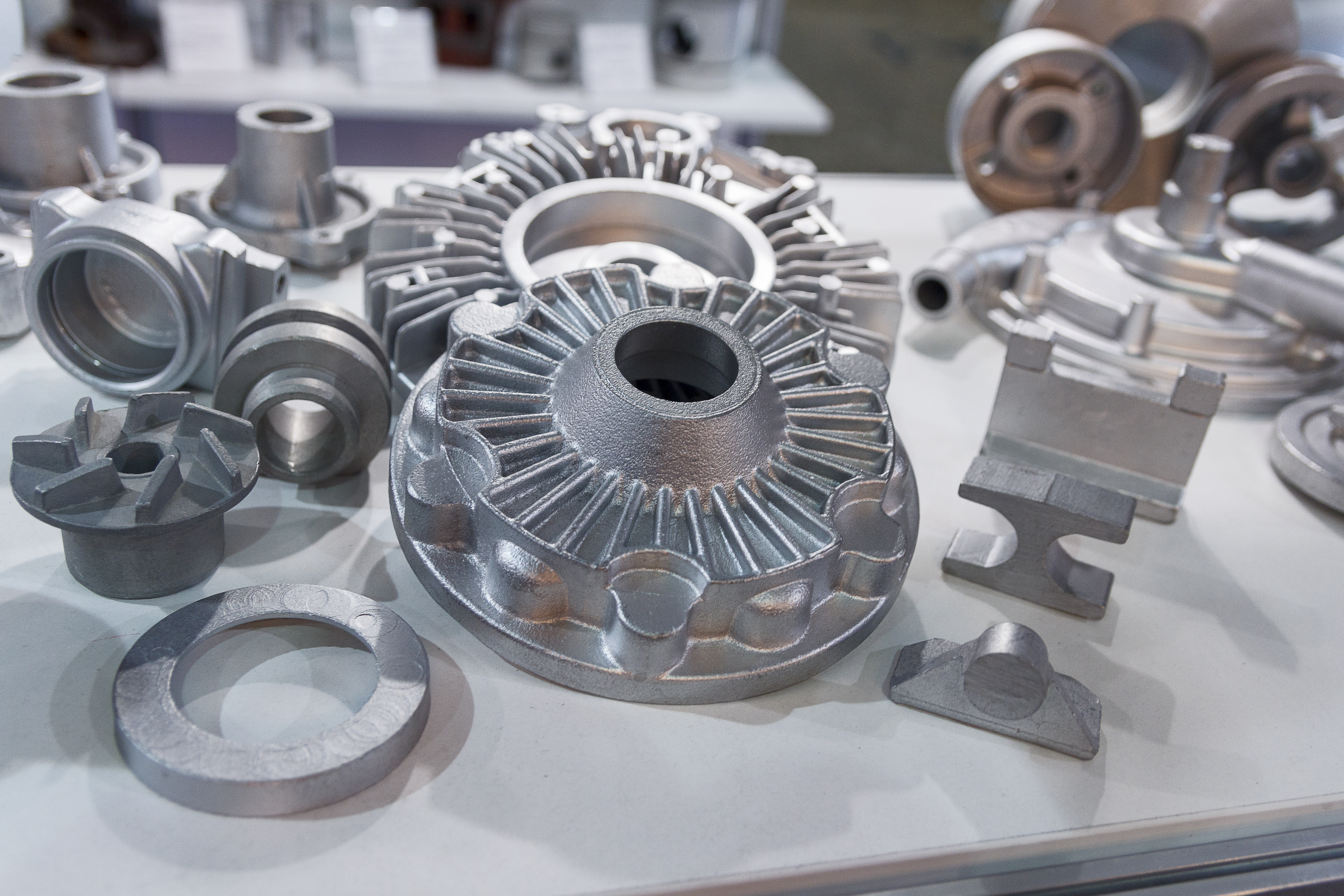
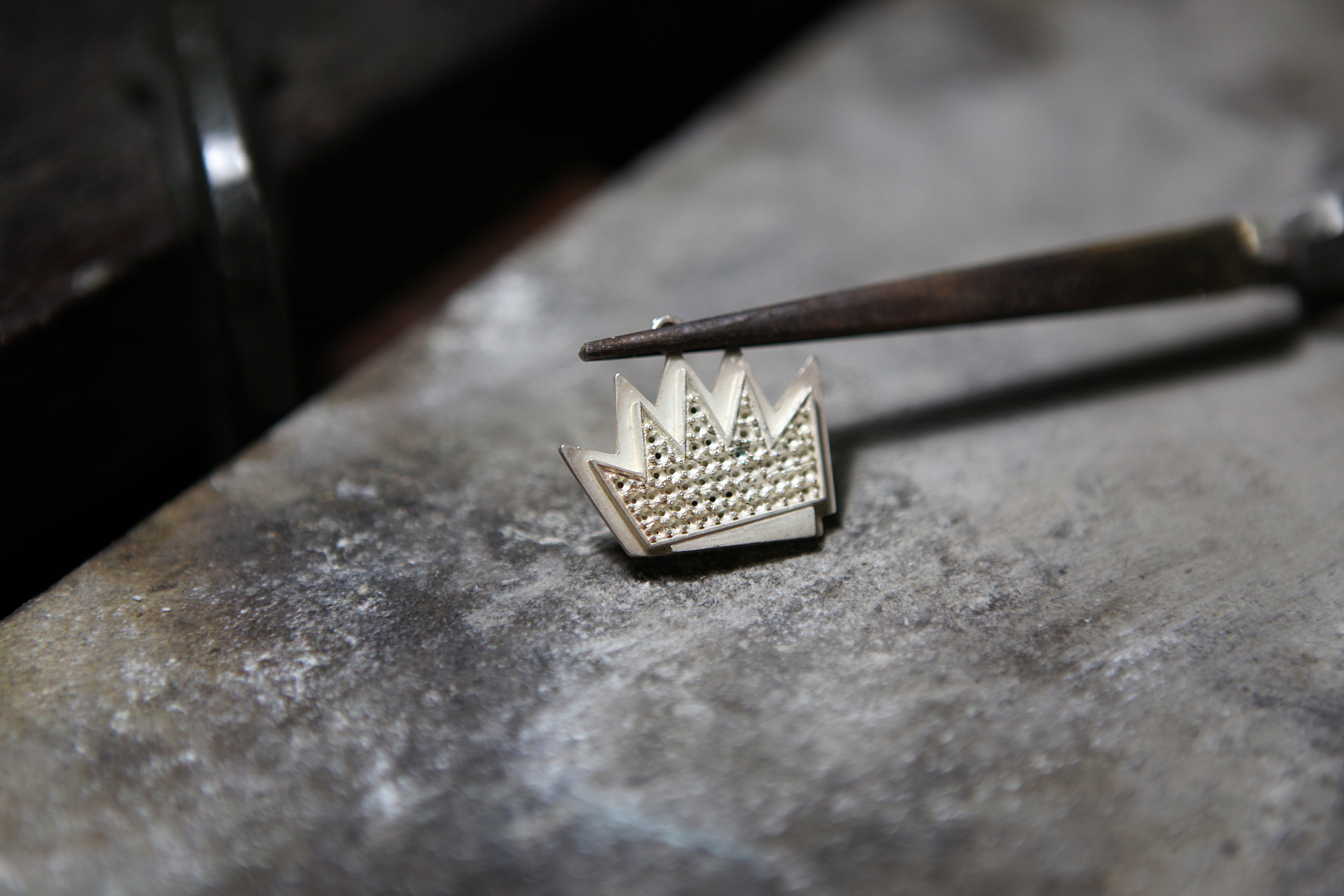
SYNERGIES AND BENEFITS OF CASTING USING HIP
Since casting is a process in which a liquid solidifies inside a mold, various problems can cause defects in the finished component. Effects such as spurts, heterogeneities, trapped gases or loss of solubility of gases in the transition from liquid to solid or during cooling, can cause the appearance of porosities in the parts manufactured by casting, often difficult to avoid in castings of complex geometry.
Thanks to Hot Isostatic Pressing (HIP) technology, the above-mentioned problems associated with castings can be repaired effectively and efficiently while applying the heat processes required for the material to come into service. This avoids having to carry out expensive, manual repairs to castings by welding. This is in addition to the advantage that the use of HIP improves the mechanical properties of the parts, such as resilience, toughness or fatigue life.
Common examples of HIP and casting combinations:
In jewelry, certain palladium and iridium castings are subjected to HIP to improve the responsiveness of these materials to polishing.
In aeronautics, engine components that are manufactured by casting (nickel super alloy) are subjected to HIP to eliminate the porosity of these critical components in aircraft engines.