Additive Manufacturing (AM)
Additive Manufacturing (AM) is a manufacturing process that encompasses various techniques that have the production of three-dimensional components from a previous CAD design in common, based on the addition of layers or two-dimensional elements. This form of manufacture allows for greater design freedom as it is not limited by conventional manufacturing techniques. Additive Manufacturing is also known as 3D printing or rapid prototyping.
Hiperbaric's Hot Isostatic Pressing (HIP) technology improves the properties of the metal parts manufactured by different AM processes, giving them more added value and making them suitable for a larger number of applications by providing them with the necessary functionalities.
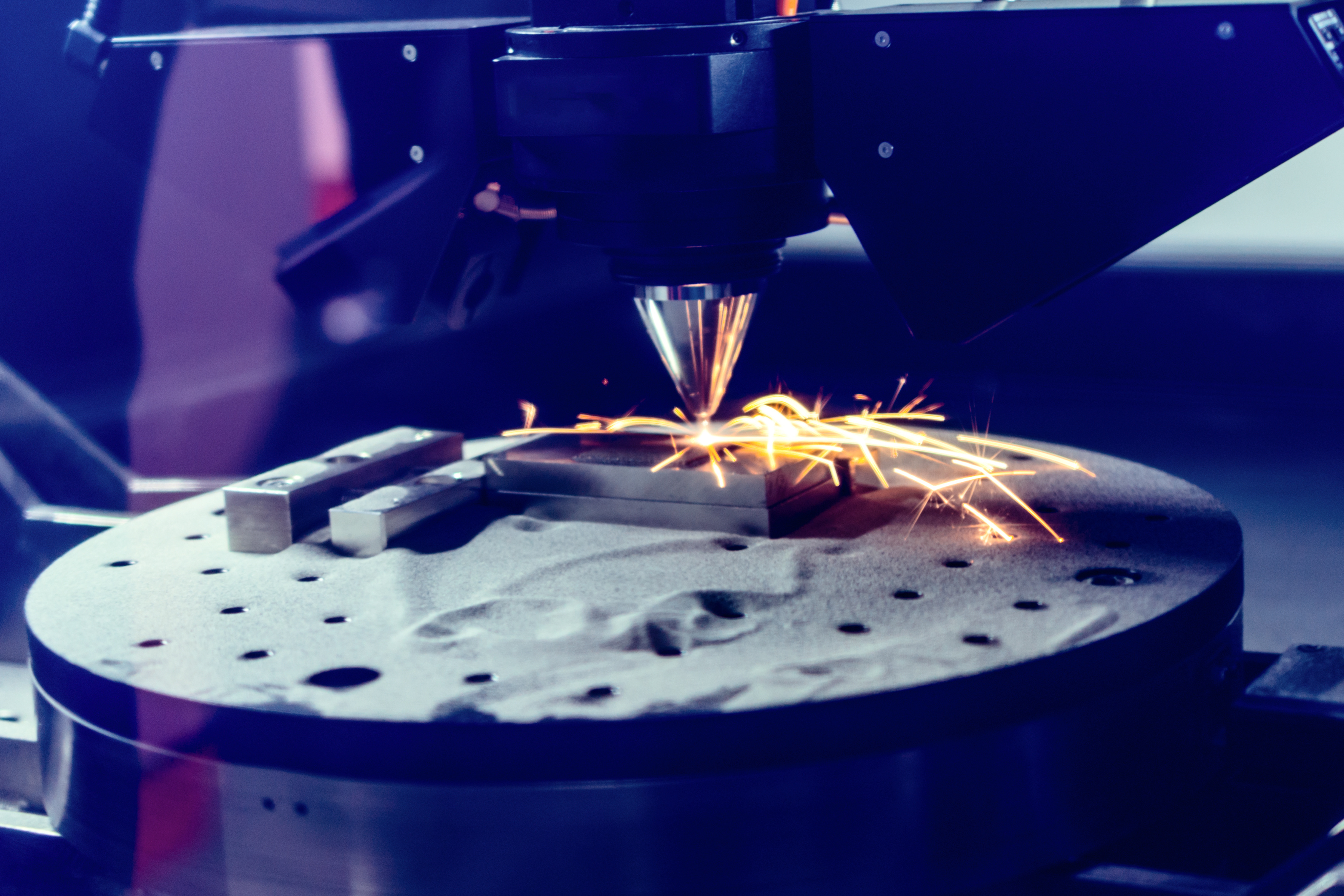
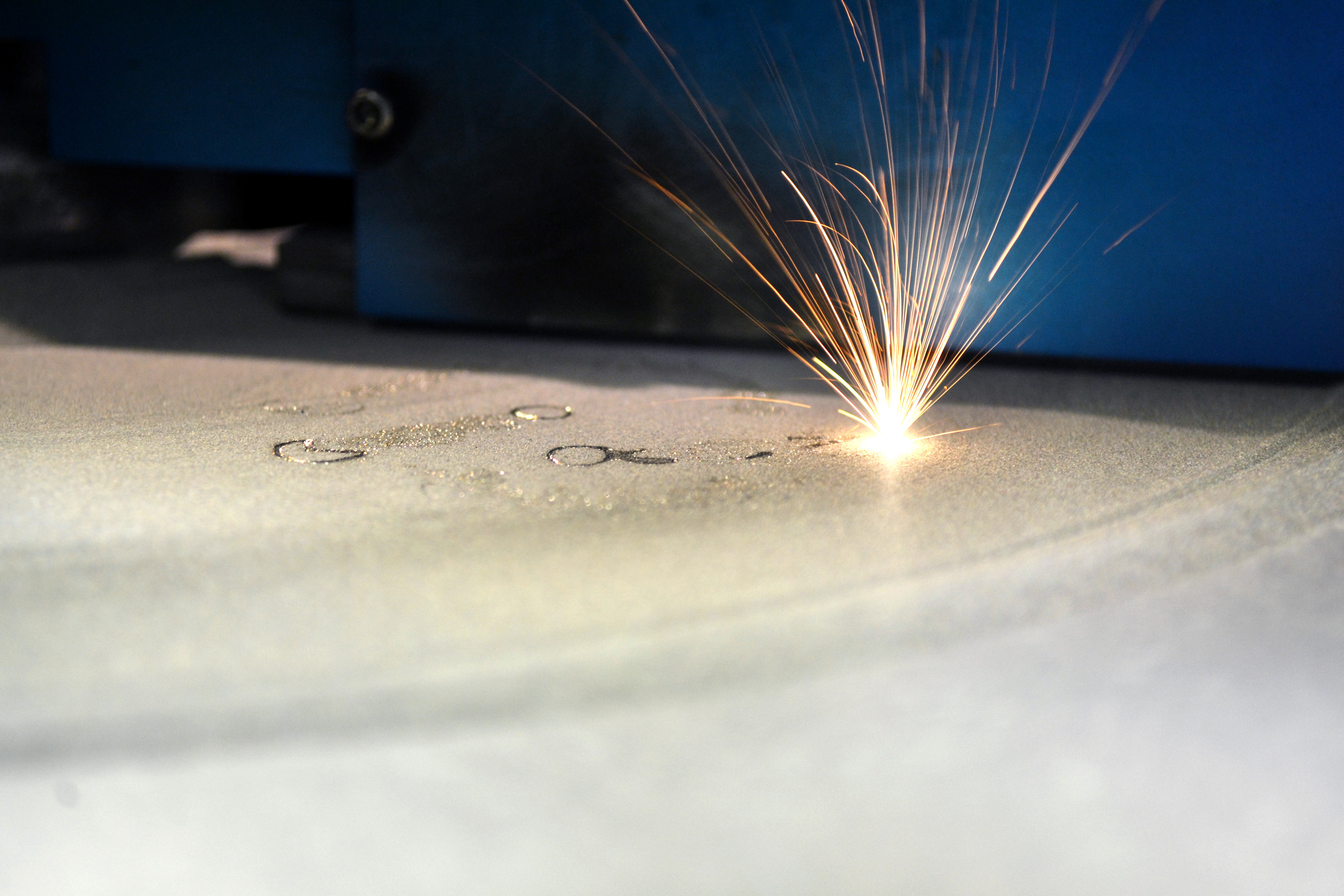
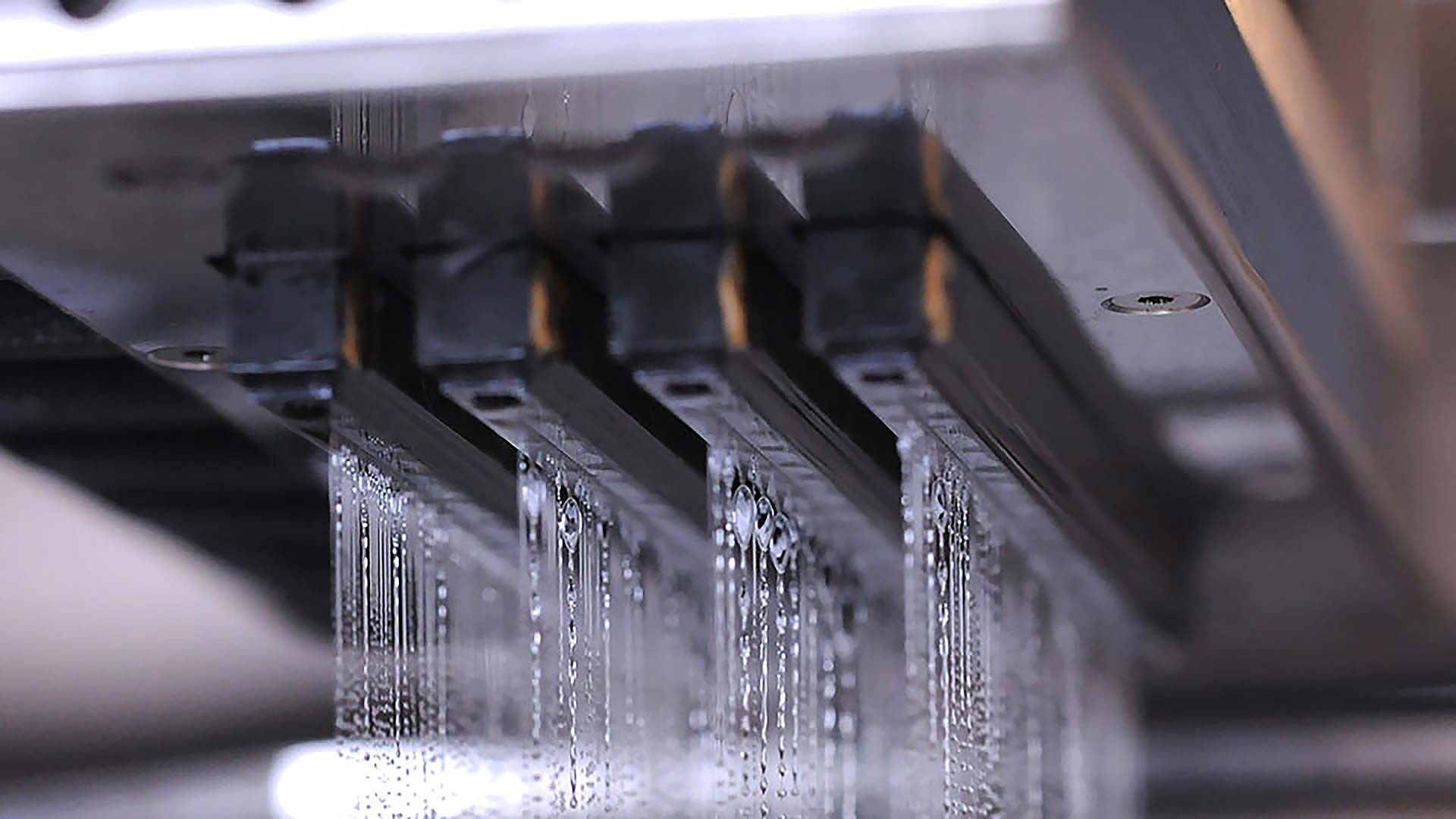
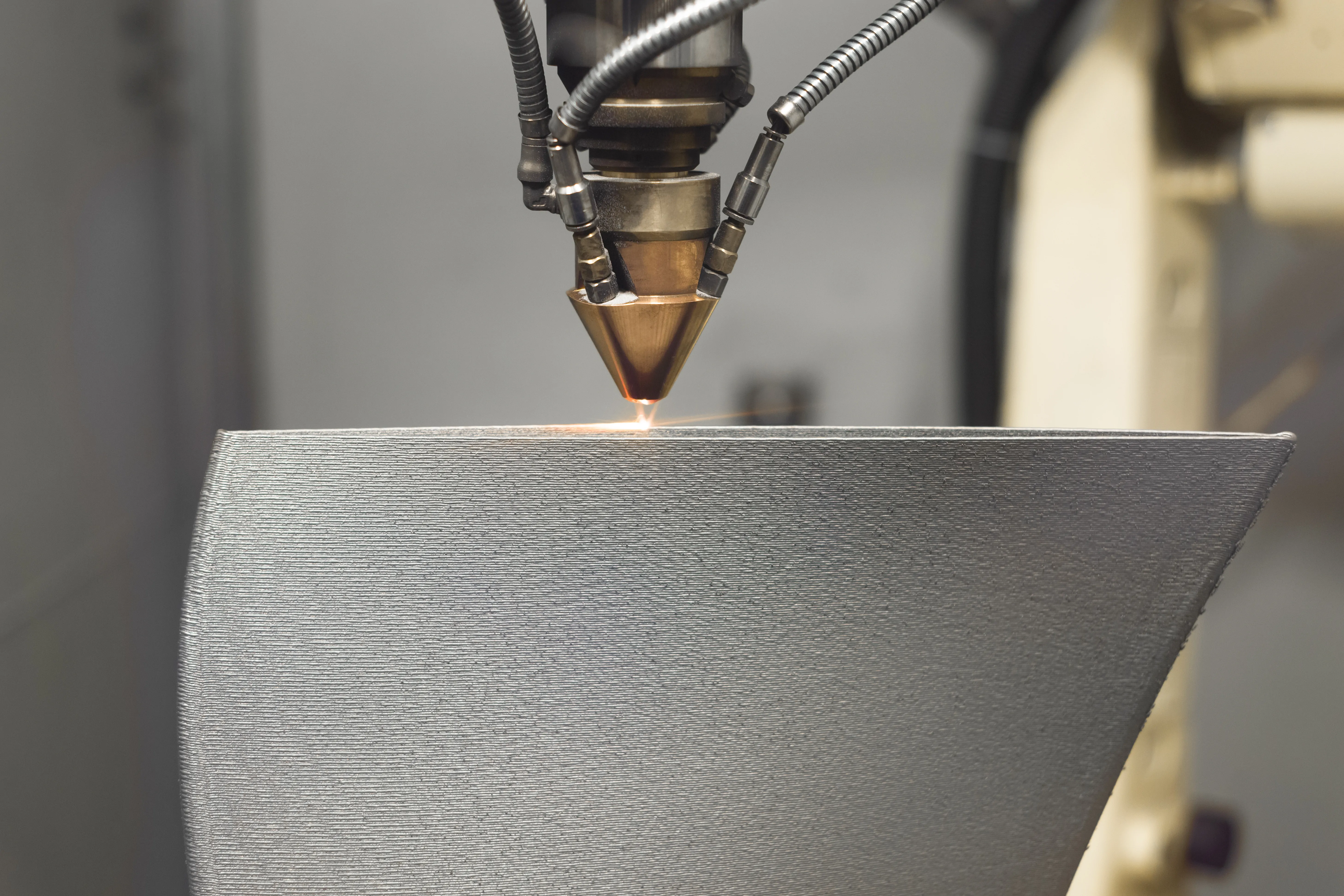
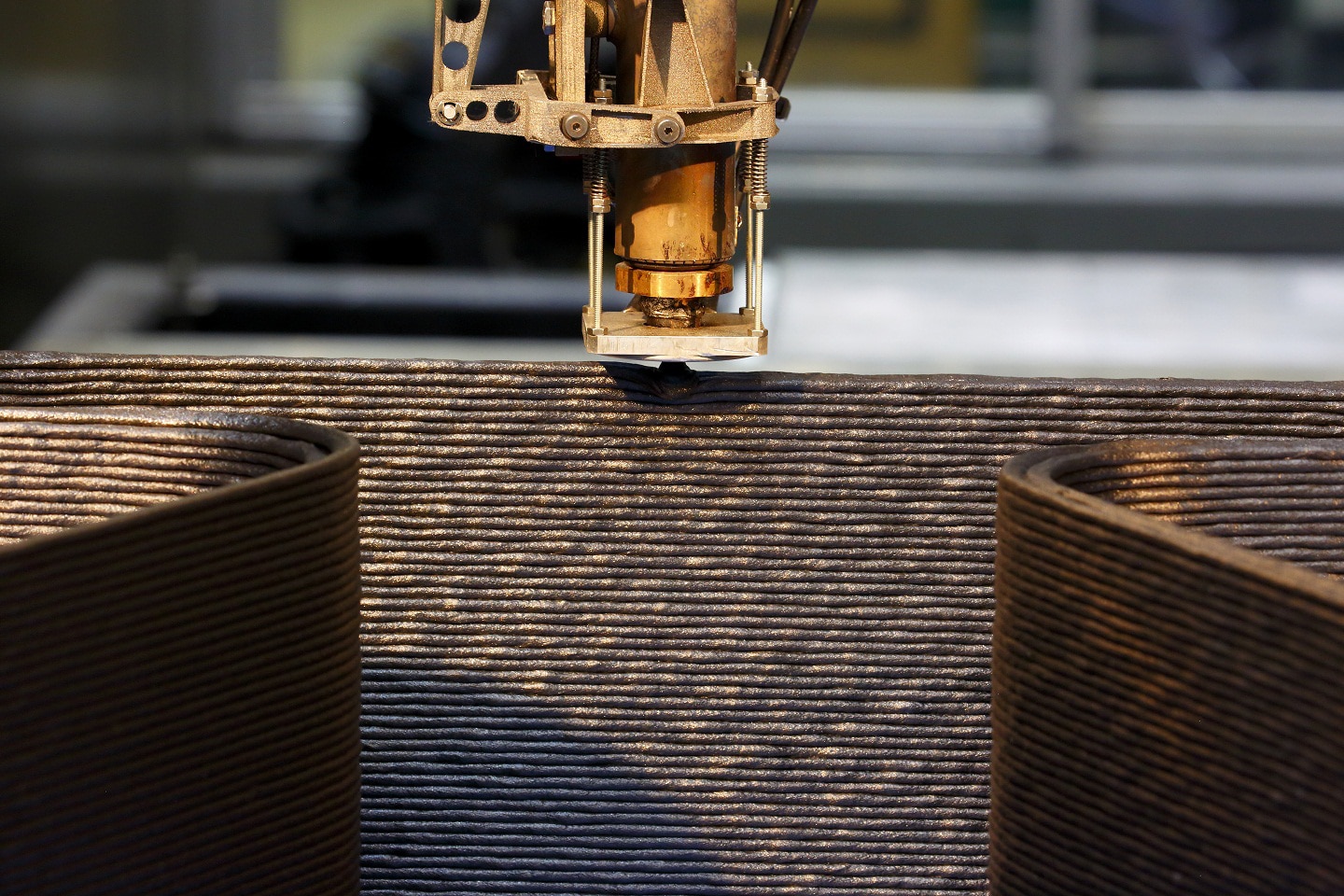

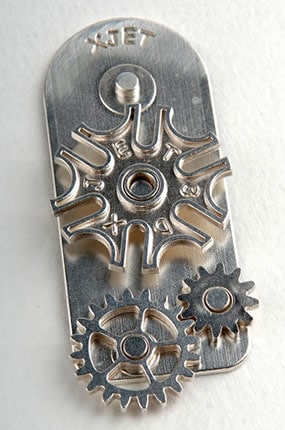
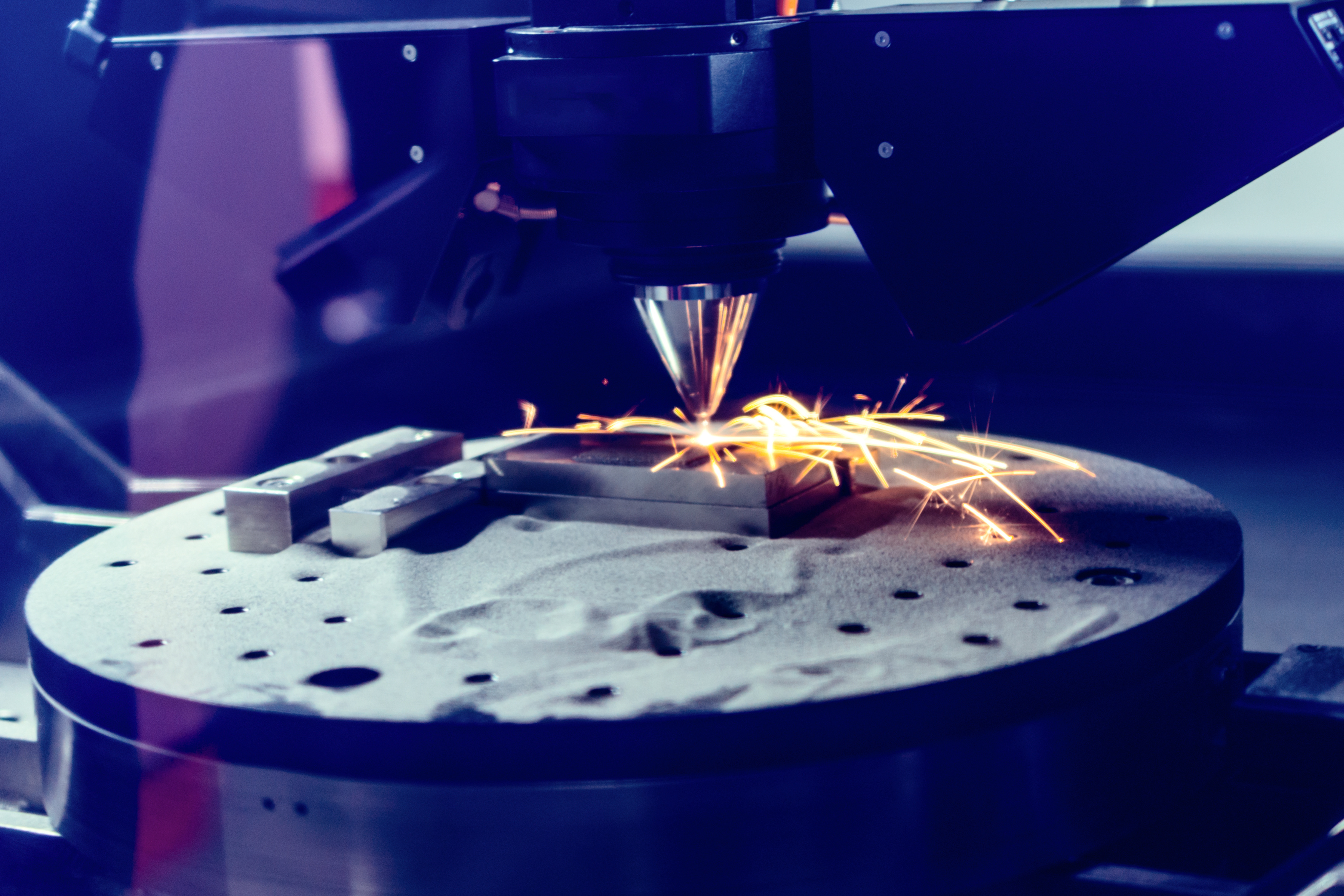
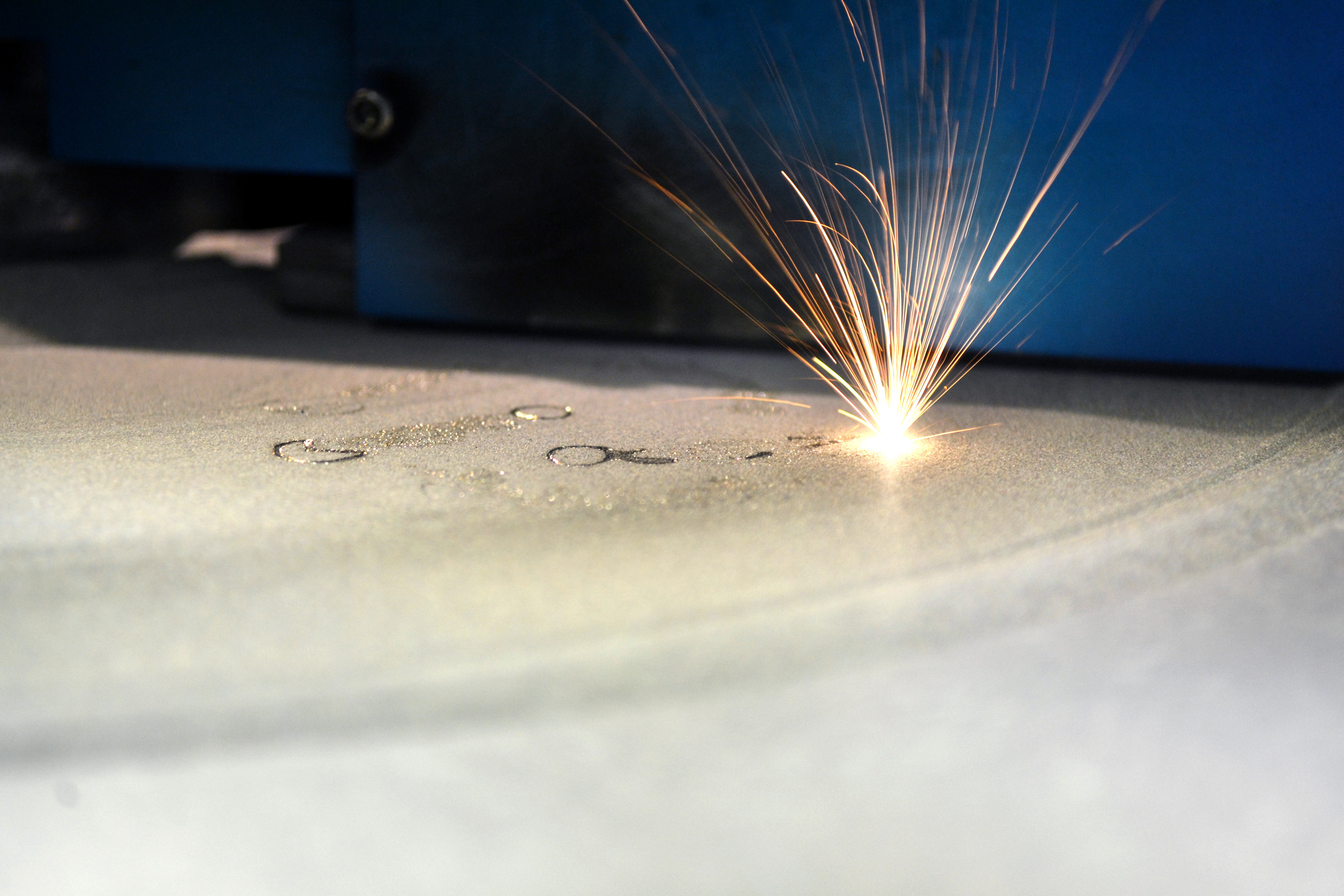
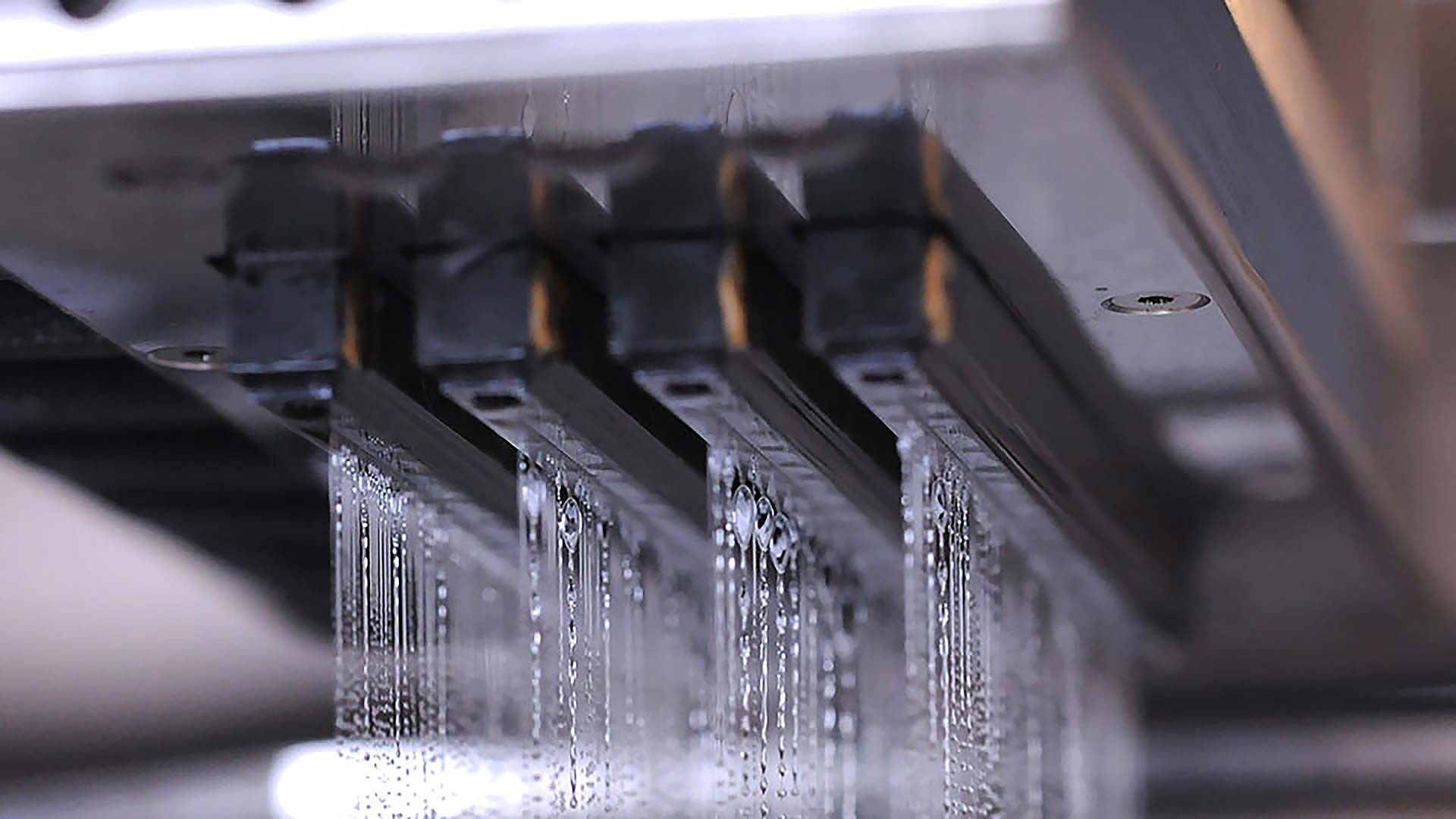
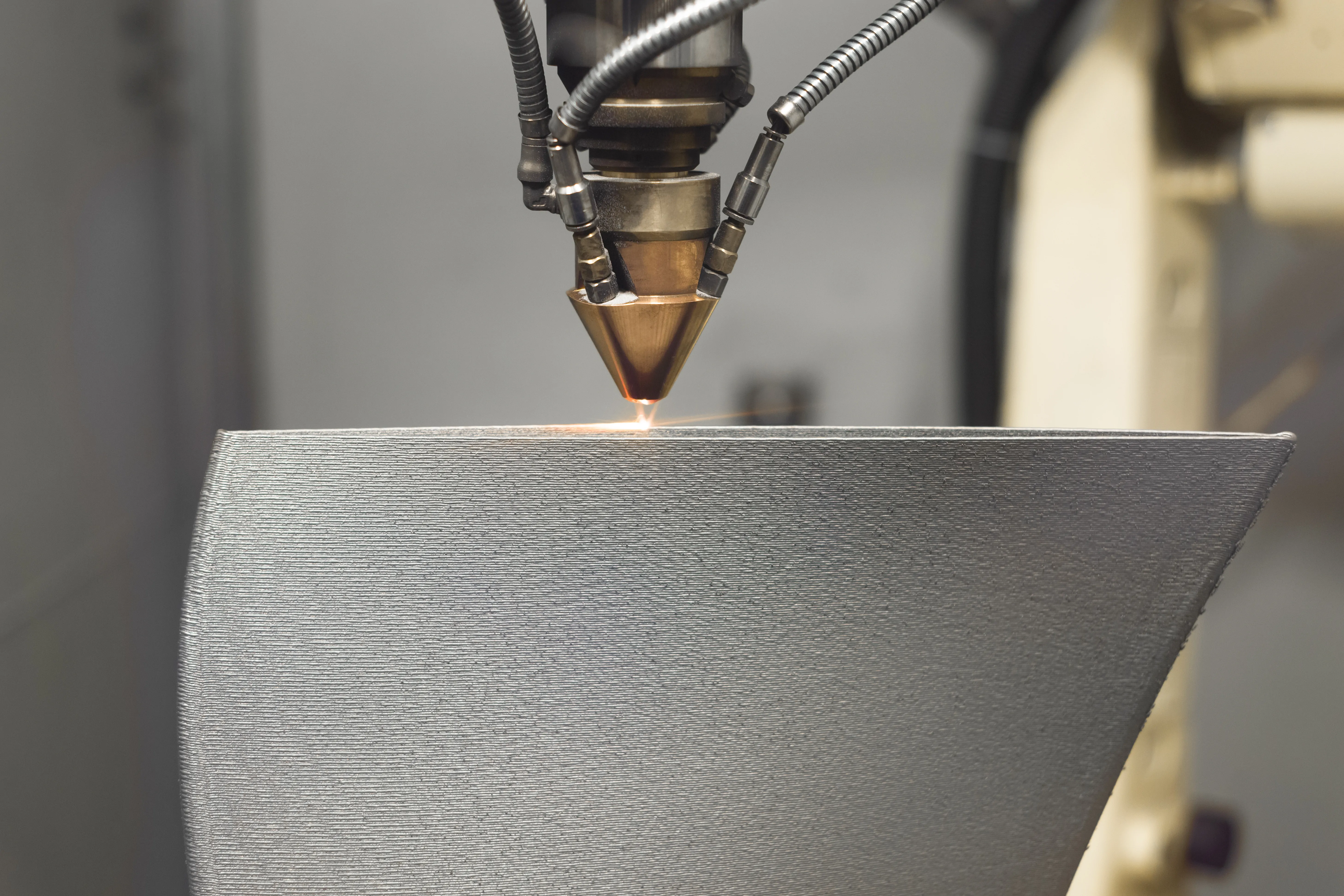
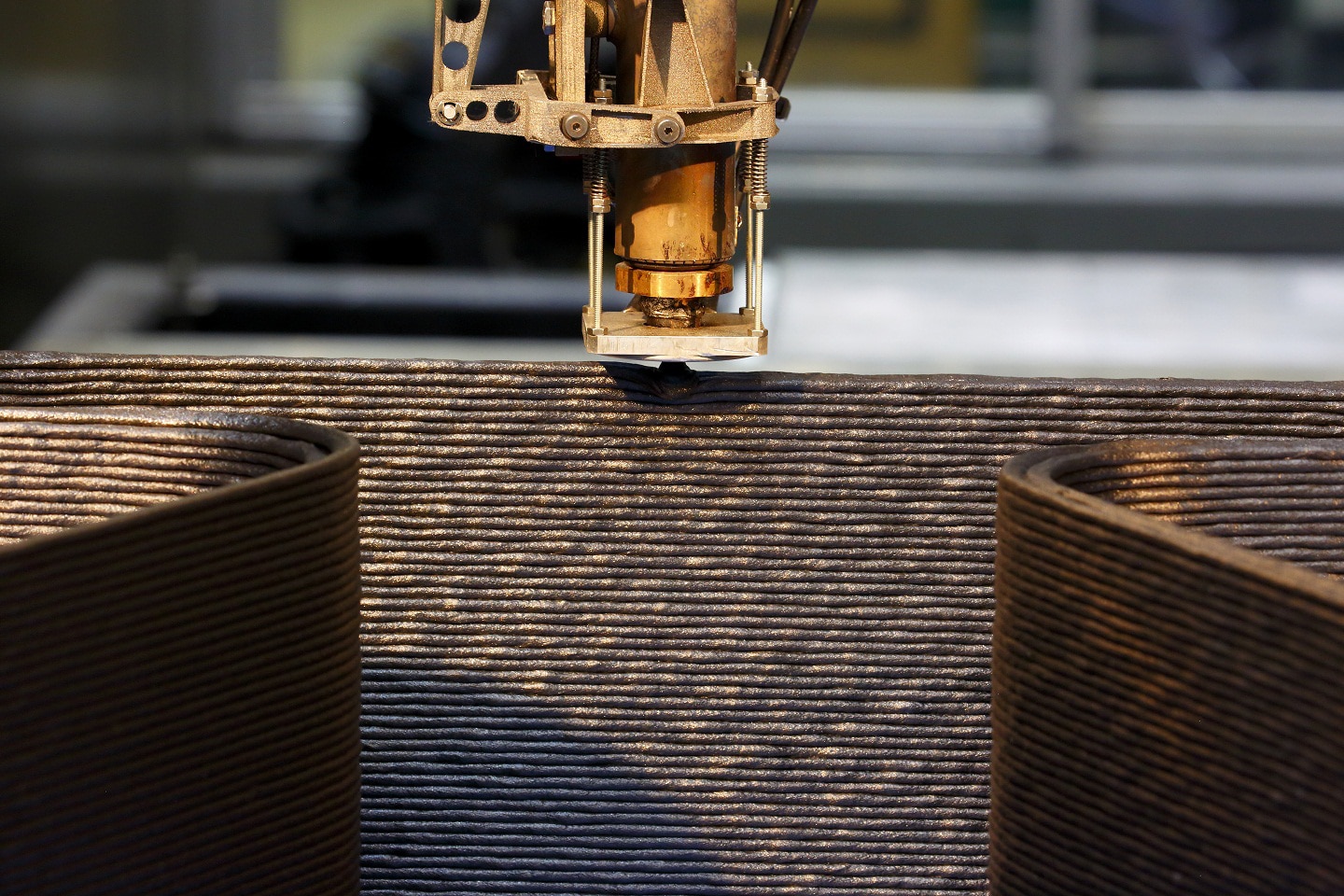

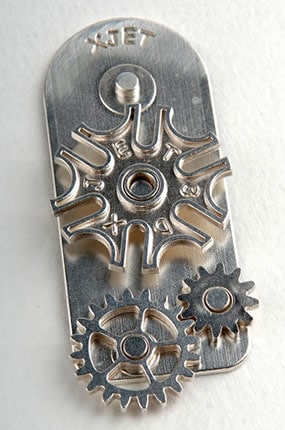
SYNERGIES AND BENEFITS OF ADDITIVE MANUFACTURING WITH THE APPLICATION OF HIP
Nowadays, as the various AM techniques achieve greater reliability and robustness, this form of manufacturing is moving away from validation prototypes, which were possible until now, to become a way of manufacturing components in batches in a viable manner. Alongside this growth, HIP technology has become established as a key post-processing tool to ensure the quality of these components, as its application has numerous benefits, such as the following:
- Elimination of porosity and densification of the material.
- Possibility of combined heat treatment with HIP, saving time and cost.
- Improvement of mechanical properties such as ductility, resilience and fatigue life.
- Reparation of defects and therefore reduction of the number of failures..
- Cost reduction by reducing the number of non-destructive tests required.
Typical examples of HIP and AM combinations:
As Additive Manufacturing techniques evolve and the number of studies supporting the benefits of combining them with Hot Isostatic Pressing processes increases, examples of combining the two technologies continue to grow. Some of the best known examples include the following:
- In the aerospace sector, fuel injectors and other CoCr components manufactured by L-PBF (Laser - Powder Bed Fusion).
- Also in the aerospace sector, turbine blades in aircraft engines, manufactured from nickel superalloys using the L-PBF technique.
- In the field of medical implants, hip and knee prostheses manufactured using L-PBF and EBM (Electron Beam Melting) from titanium alloys.
- In the automotive sector, thanks to HIP, the prototypes and parts manufactured by Additive Manufacturing (AM) can be used with total confidence, as they obtain greater reliability and better properties.
METAL ADDITIVE MANUFACTURING TECHNIQUES
The various Additive Manufacturing techniques differ in the way the two-dimensional layer is created, and the way each layer attaches to the previous layers. This defines the required precision, materials and post-processes, as well as times and costs of each AM method making some more suitable than others depending on the application.
Additive Manufacturing - Powder Bed Fusion (PBF)
Selective Laser Melting (SLM), also known as Selective Laser Sintering (SLS), or DSL or EBM (Electron Beam Melting)
This is one of the most established AM techniques. The piece is created from layers of metal powder spread evenly and welded to the previous layer with a power source. The power source can be either L-PBF/SLM laser or an E-PBF/EBM electron beam. Thus, layer by layer, the part is produced. Since it is a spot welding process, defects and porosities are relatively frequent depending on the material and processing parameters. HIP technology helps to overcome these problems.
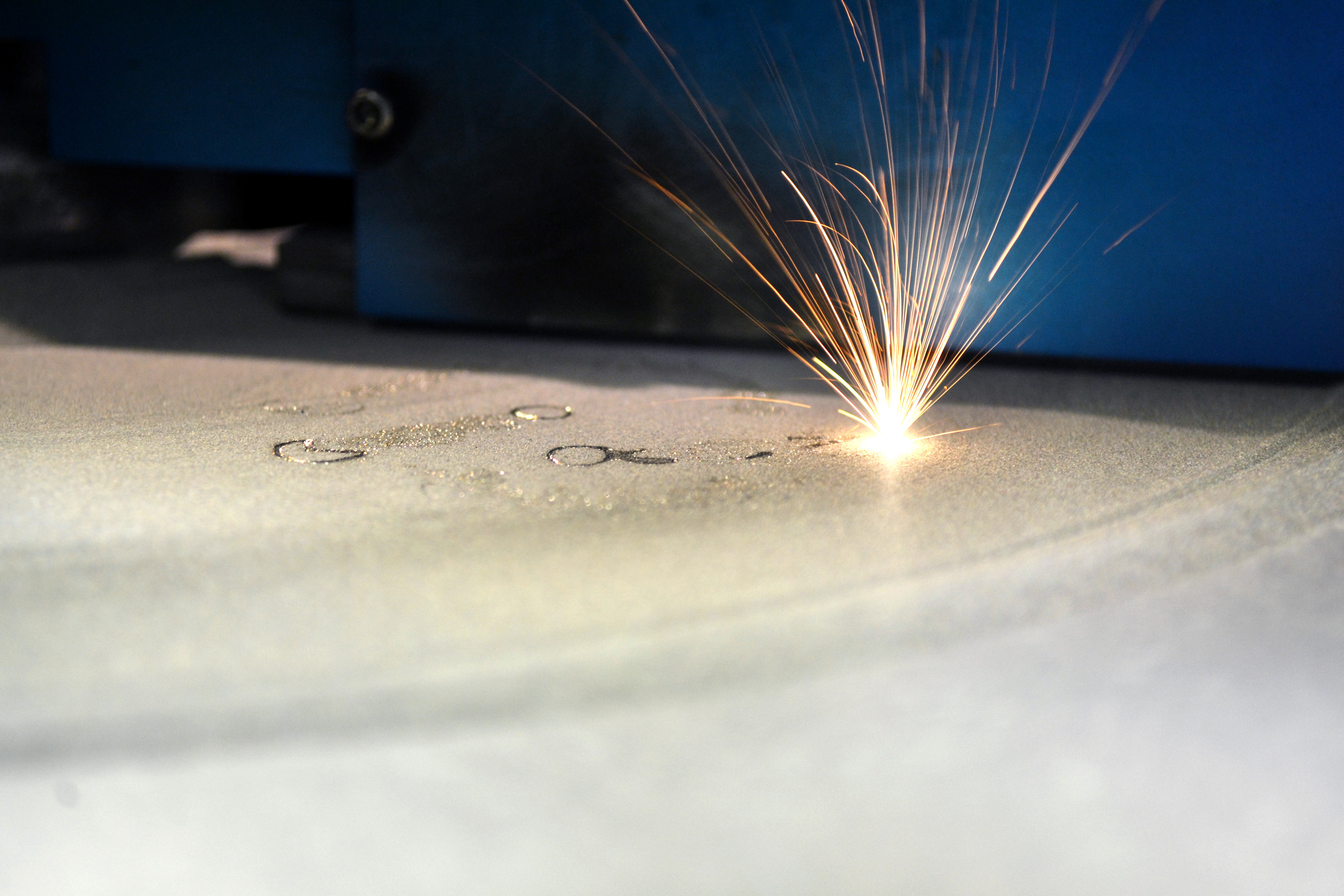
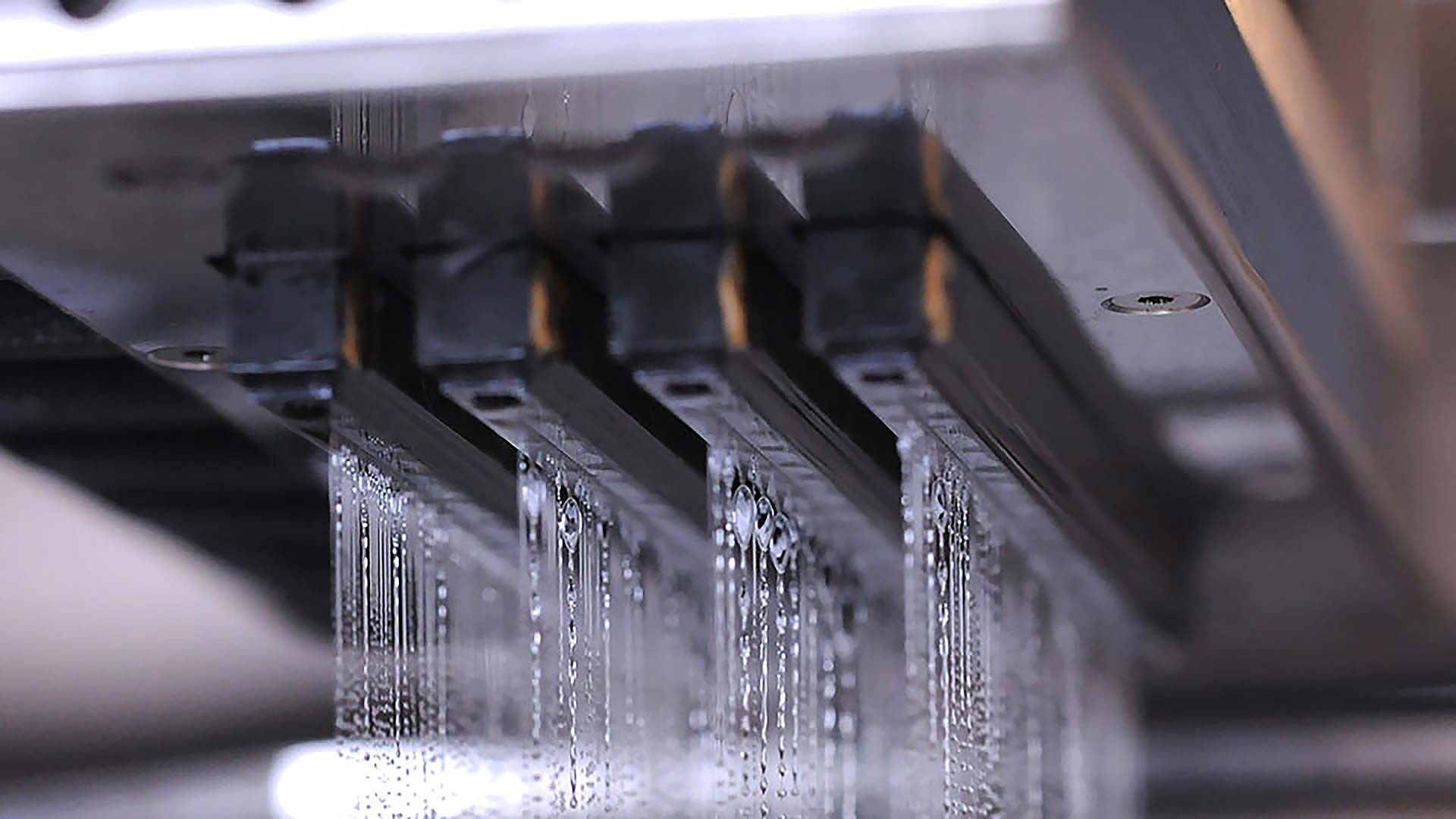
Additive Manufacturing - Binder Jetting
The Binder Jetting technology is based on a patent from MIT (Massachusetts Institute of Technology). Here, after a layer of powdered material has been applied, binder drops (liquid adhesive) are applied to hold the powder particles together, as well as to the previous layer. Due to the nature of the process, a part is obtained that is joined by a binder, called "green", which must be sintered in order to be used. During the subsequent sintering stage, the binder is removed (it can also be removed in a previous stage).
The sintering process binds the powder particles by reducing their surface energy. Total densification is not achieved after sintering, for this reason, HIP technology is applied for components that require high mechanical properties and full density.
Additive Manufacturing - Directed Energy Deposition
This additive manufacturing process applies a source of energy while adding the material that forms a part of the part. As in Bed-Fusion processes, the energy source can be either a laser or an electron beam. The added material can also be supplied in the form of powder or wire through a concentric cone to the energy source.
This AM process has a very high output but lower geometric accuracy and is intended for repairs, coatings or large parts. Pressing these parts with HIP substantially improves their performance.
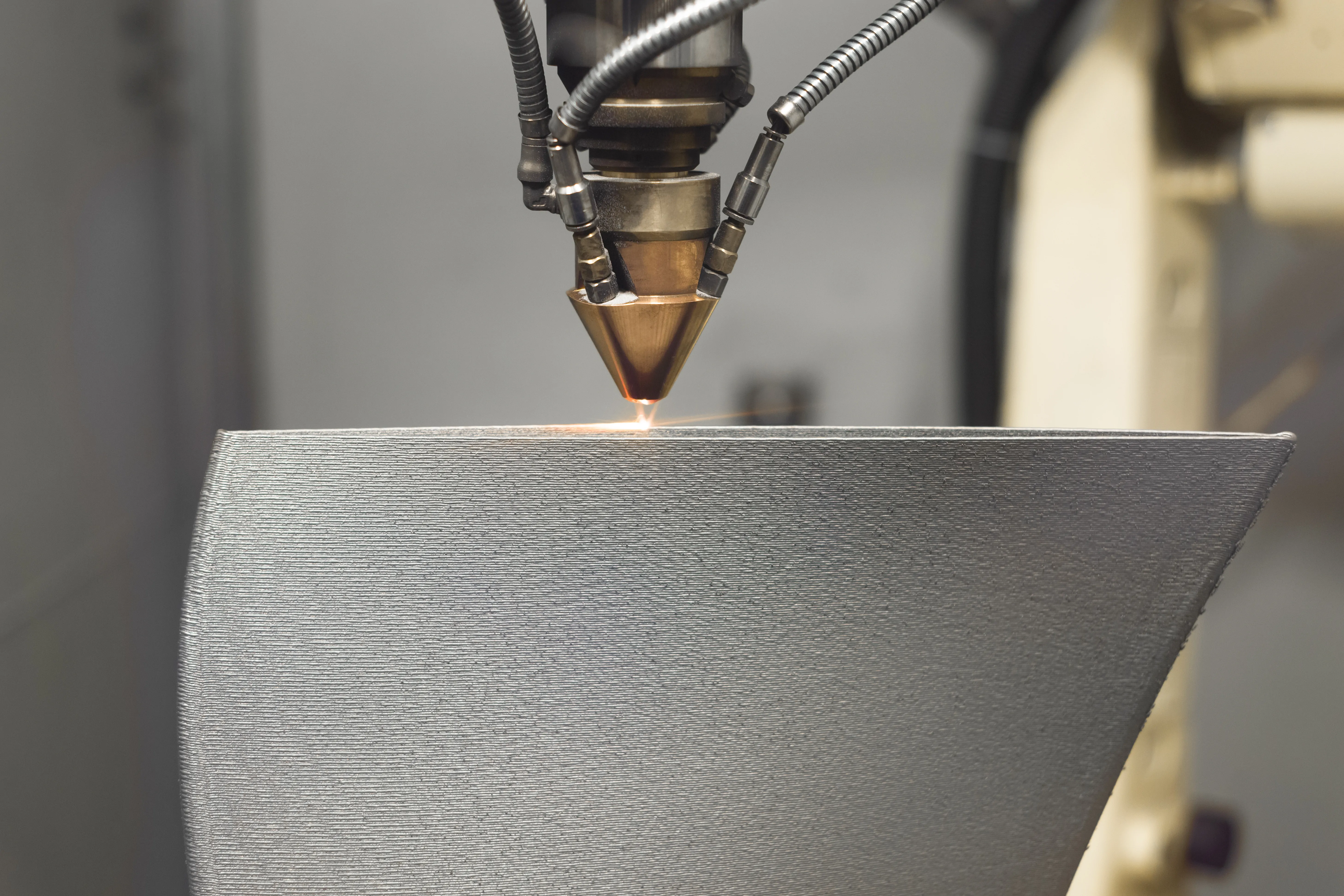
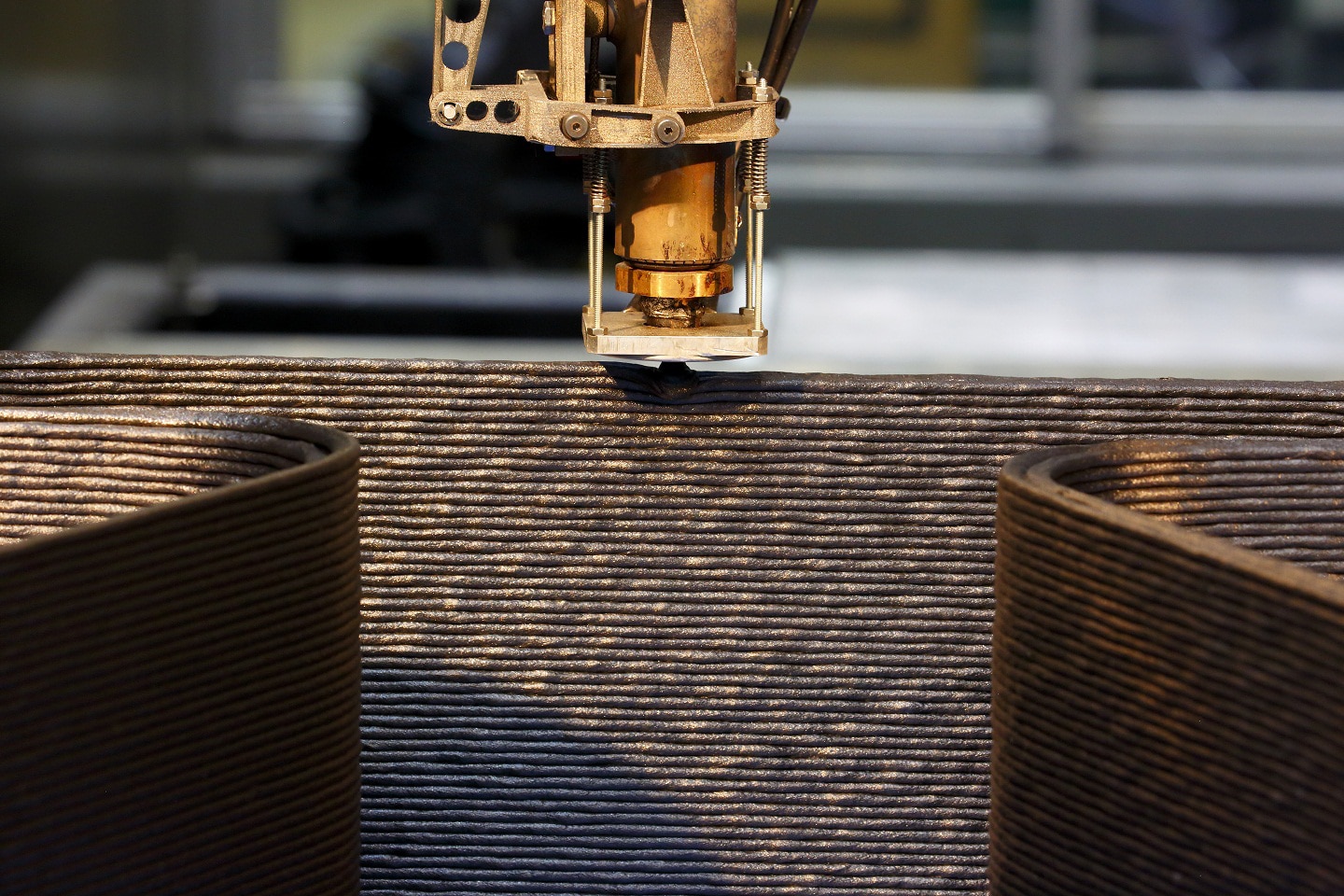
Wire Arc Additive Manufacturing (WAAM)
This technique is similar to DED in that the material and power source act together to create material. The process is essentially MIG/MAG welding. A wire made of metallic material serves as an electrode as well as a filler material. The material is deposited (sprayed) on the weld pool.
This AM process has a very high output and low geometrical quality, and is intended for repairs, coatings or large parts.
Additive Manufacturing - Material Extrusion
It is an Additive Manufacturing Technique based on the extrusion of a plastic material that flows and attaches itself to the substrate on which it is deposited. The extruded material can be a mixture of plastic Binder and metal particles.
After printing, a green piece is obtained which is then sintered to achieve a specific density and consistency. As with binder jetting, these parts can undergo HIP to achieve the maximum theoretical density.

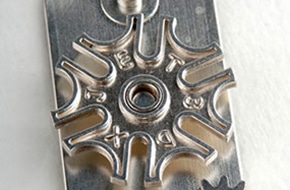
Additive Manufacturing - Material Jetting (MJ)
Includes MJ, NPJ, DOD
The evolution of the conventional printing industry towards Additive Manufacturing has led to the development of Material Jetting (MJ) technology. This is a technology in which inkjet-like print heads inject material onto a previous substrate creating, layer by layer, the 3D print. In the beginning this technology was limited to wax-like materials.
More recently, some manufacturers have developed technology where a liquid binder carrying nano metal particles is injected, creating a green part that is subsequently sintered and whose properties can be enhanced by the use of HIP.