Metal Injection Molding (MIM)
Metal Injection Molding (MIM) is a powder metallurgy manufacturing technique that injects binder and metal powder into a mold or cavity obtaining the green part with the shape of the final product. This green part must then be sintered to obtain a density of around 95-98%, depending on the process and material.
The mold or cavity into which the raw material is injected can be of very complex geometry, which makes MIM an attractive process for small, complex products that are manufactured in large batches.
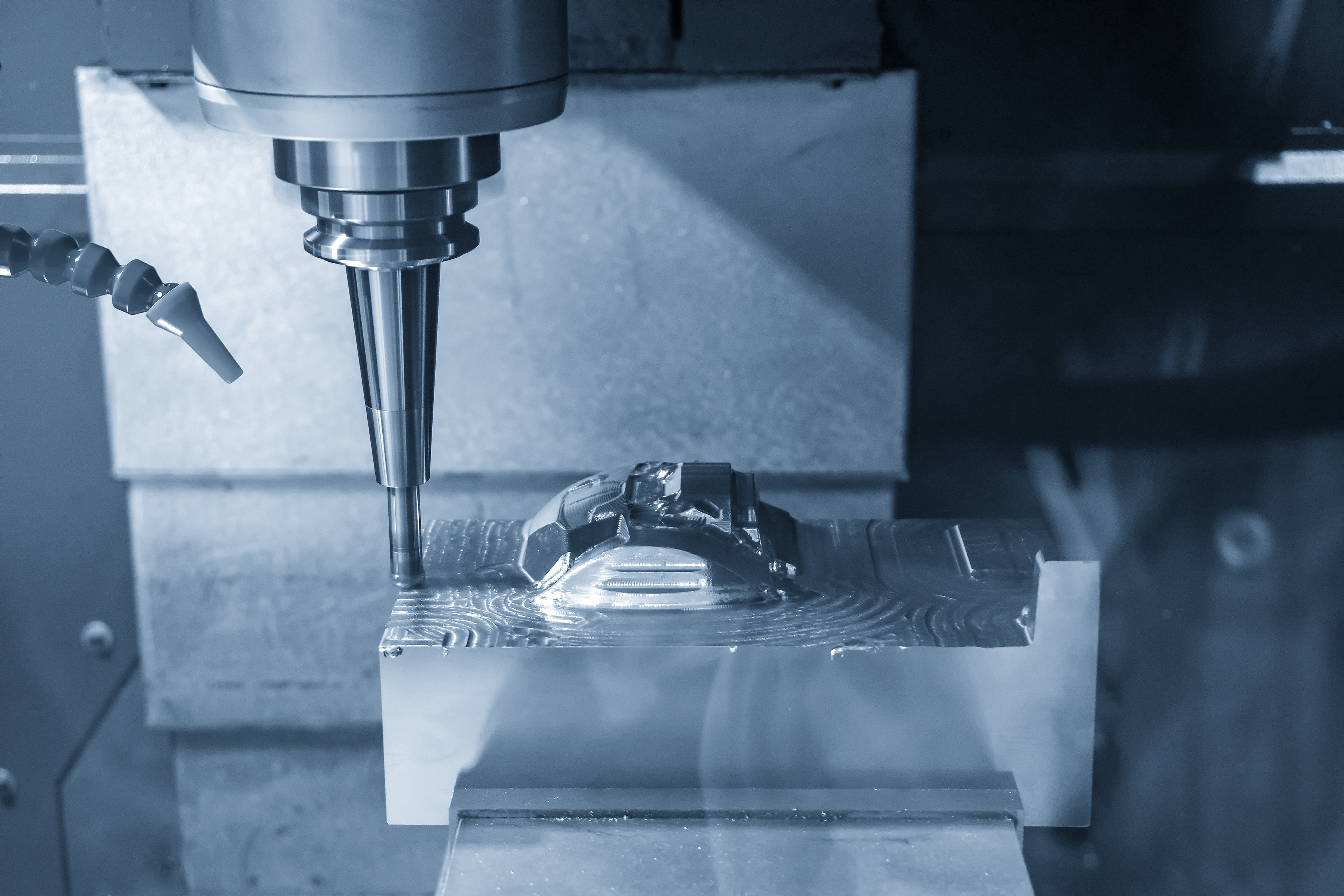
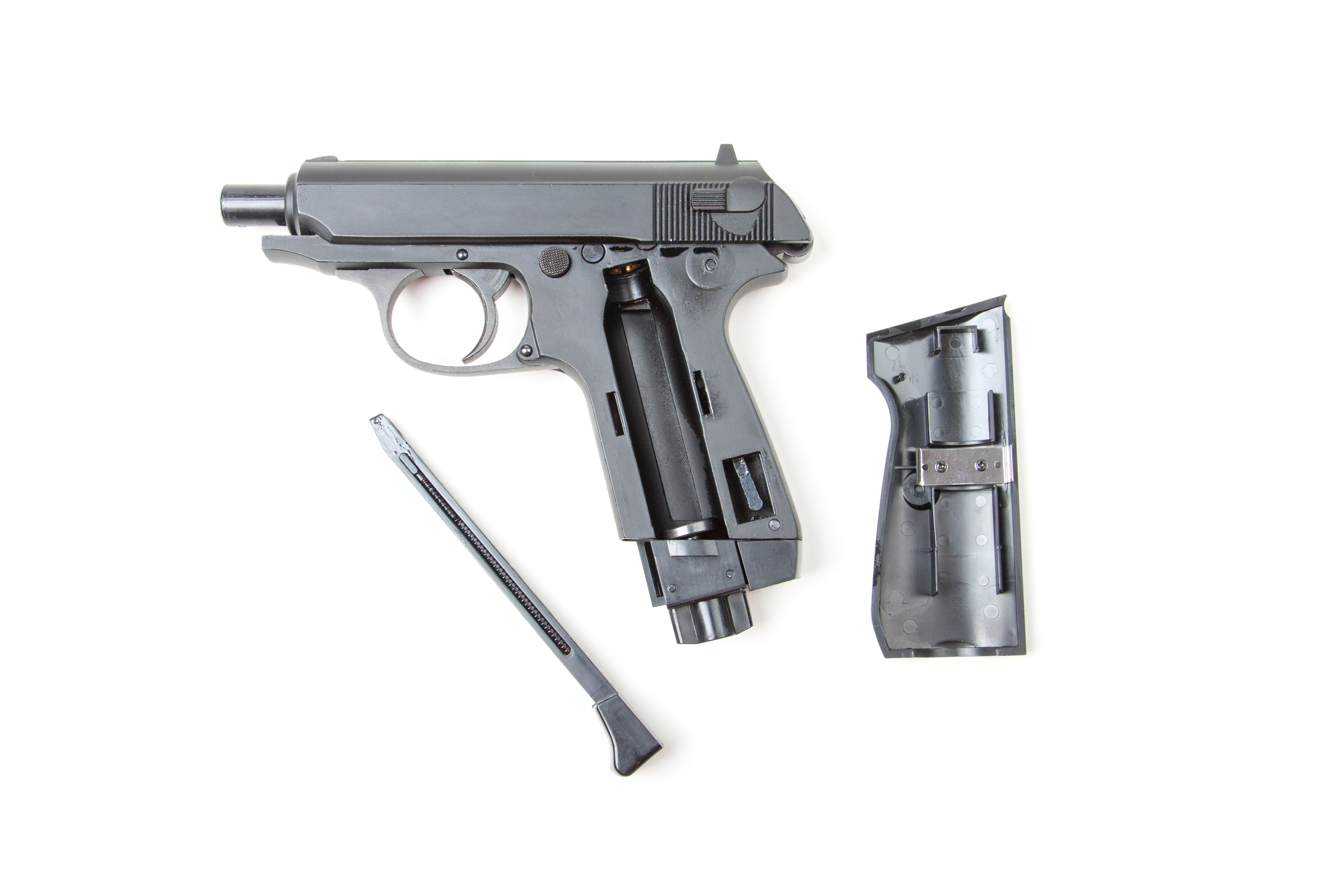
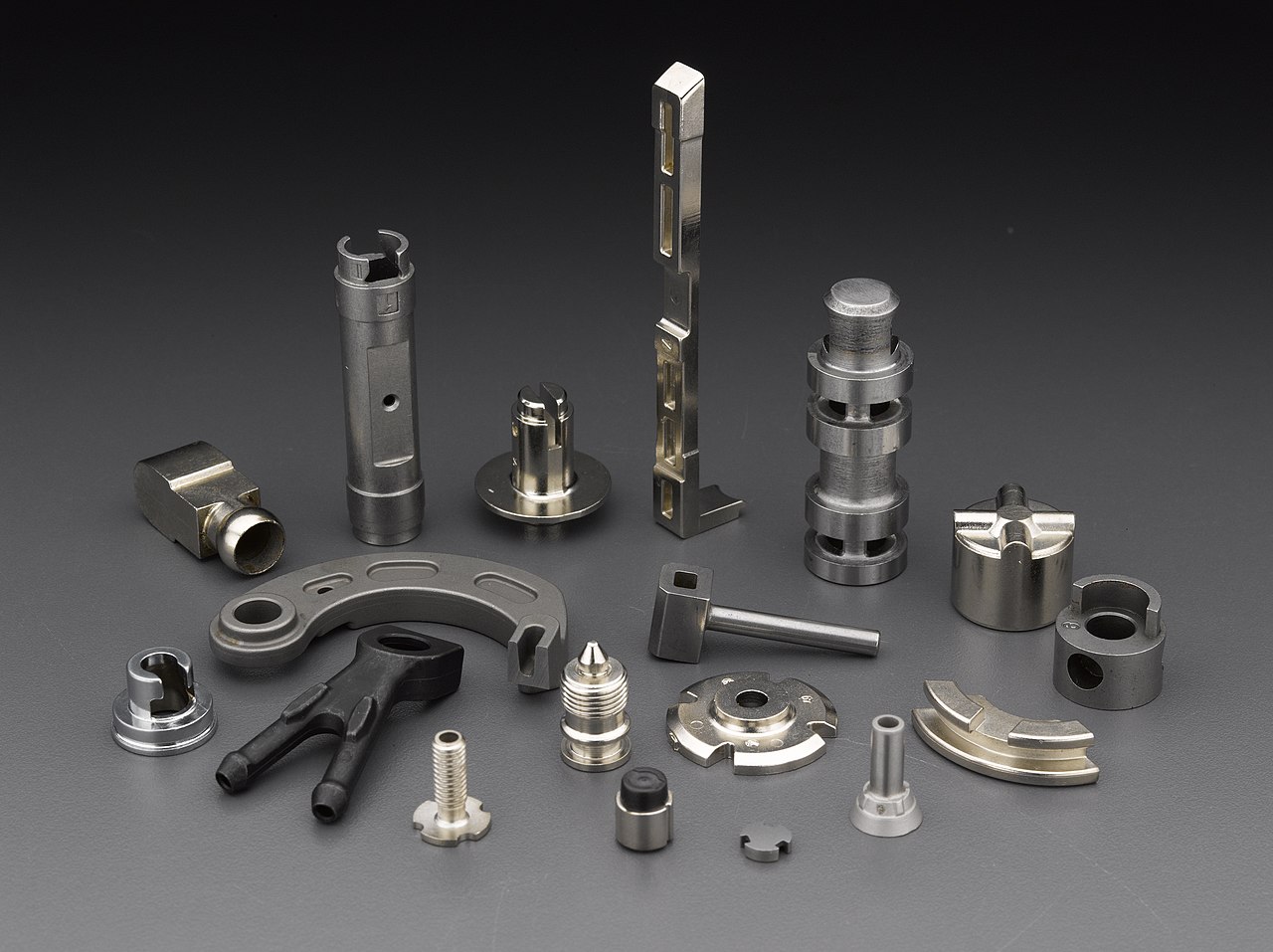
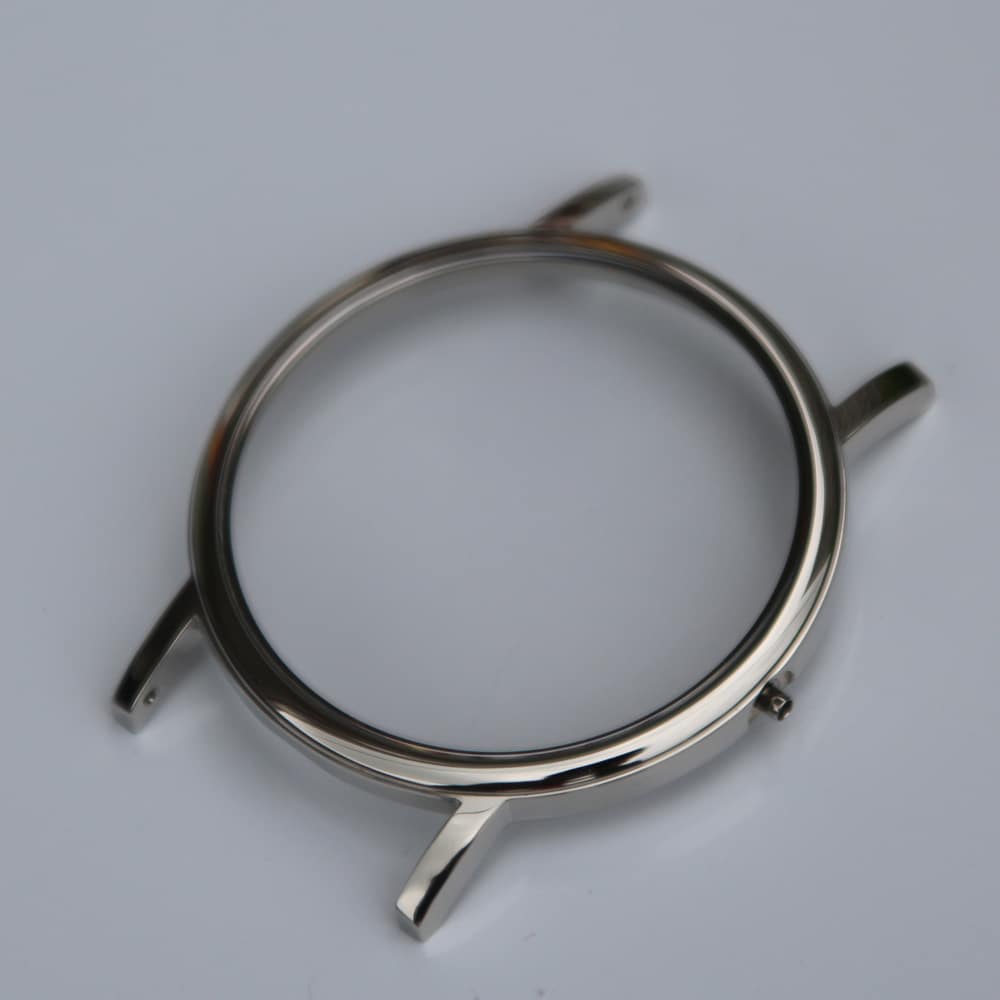
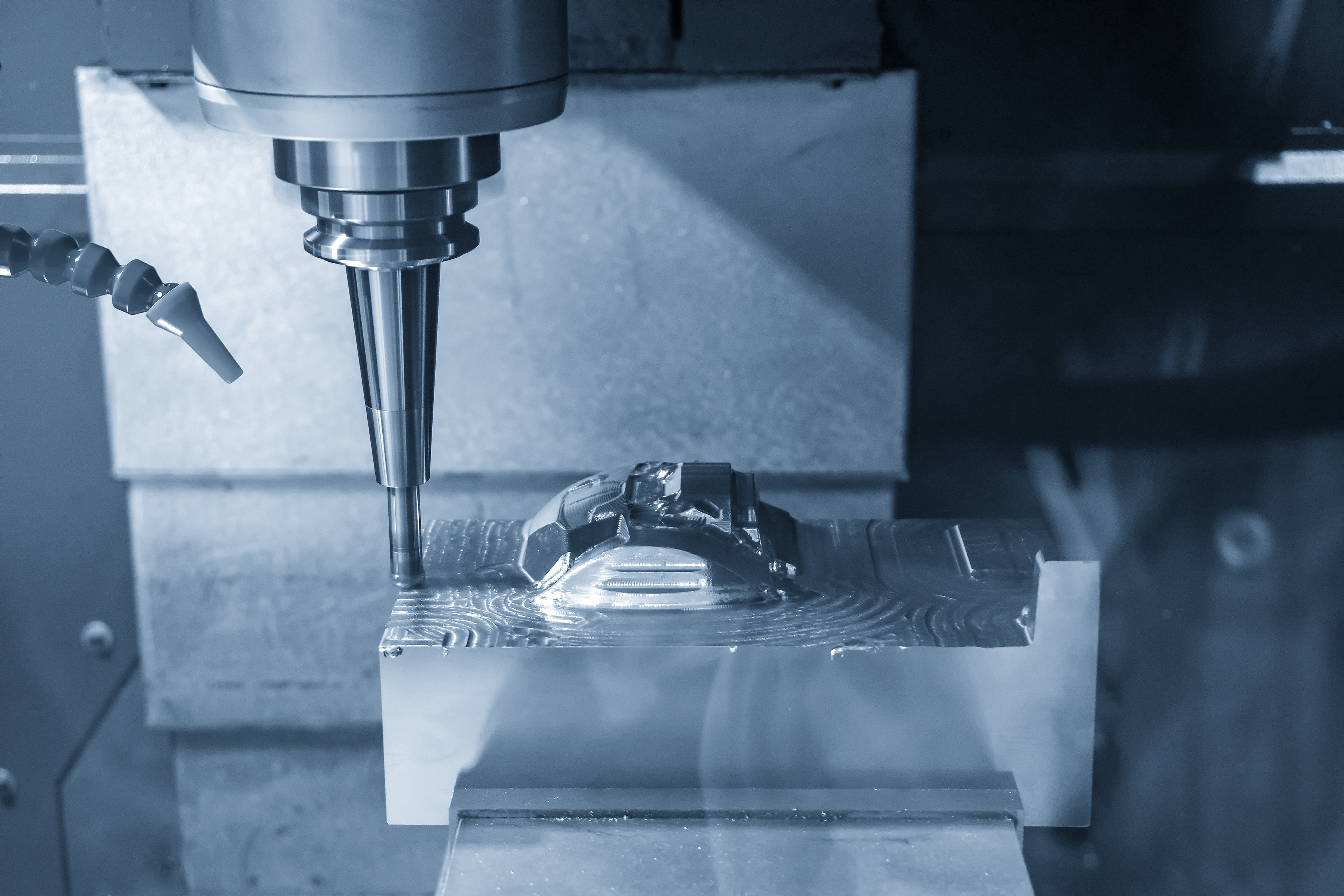
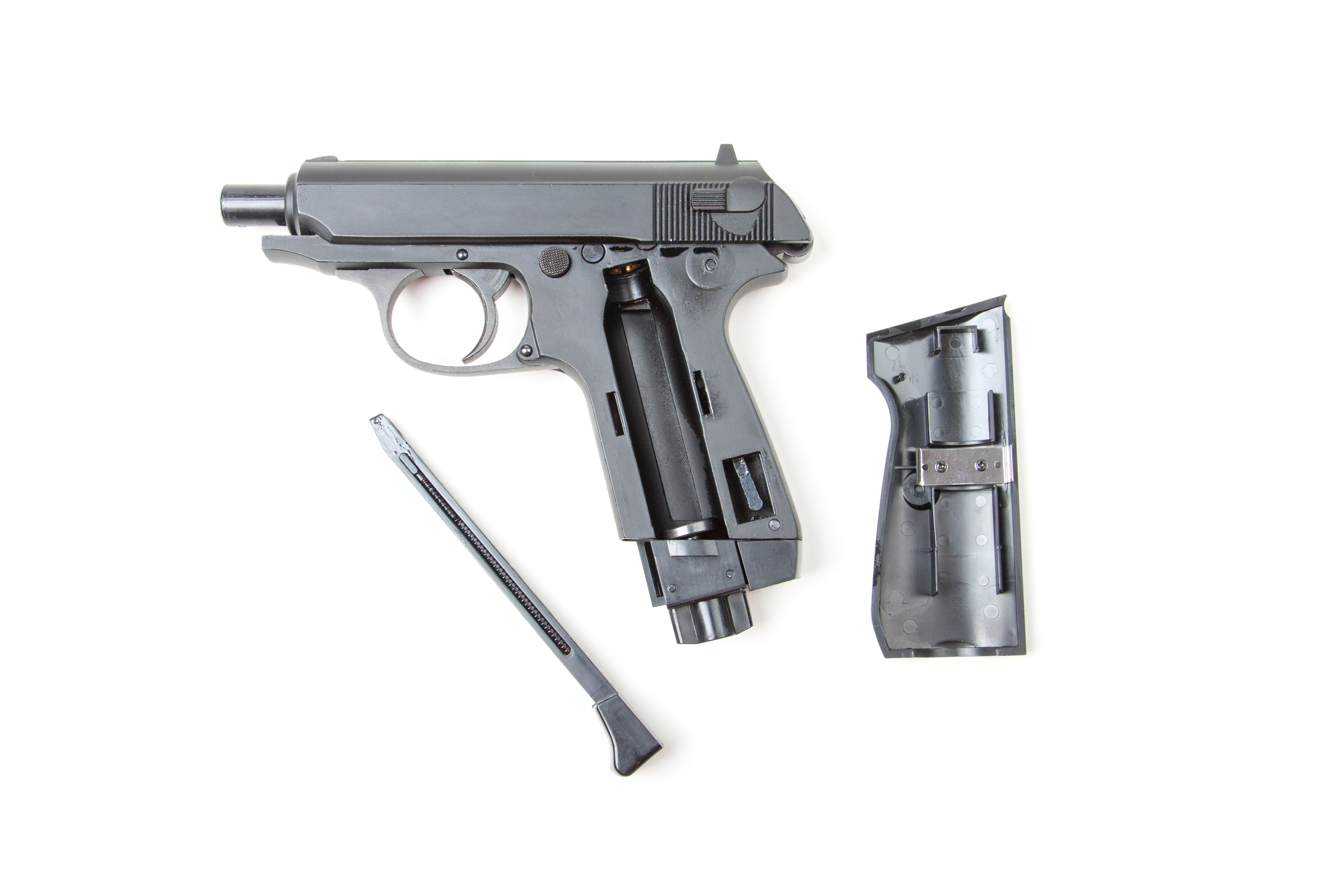
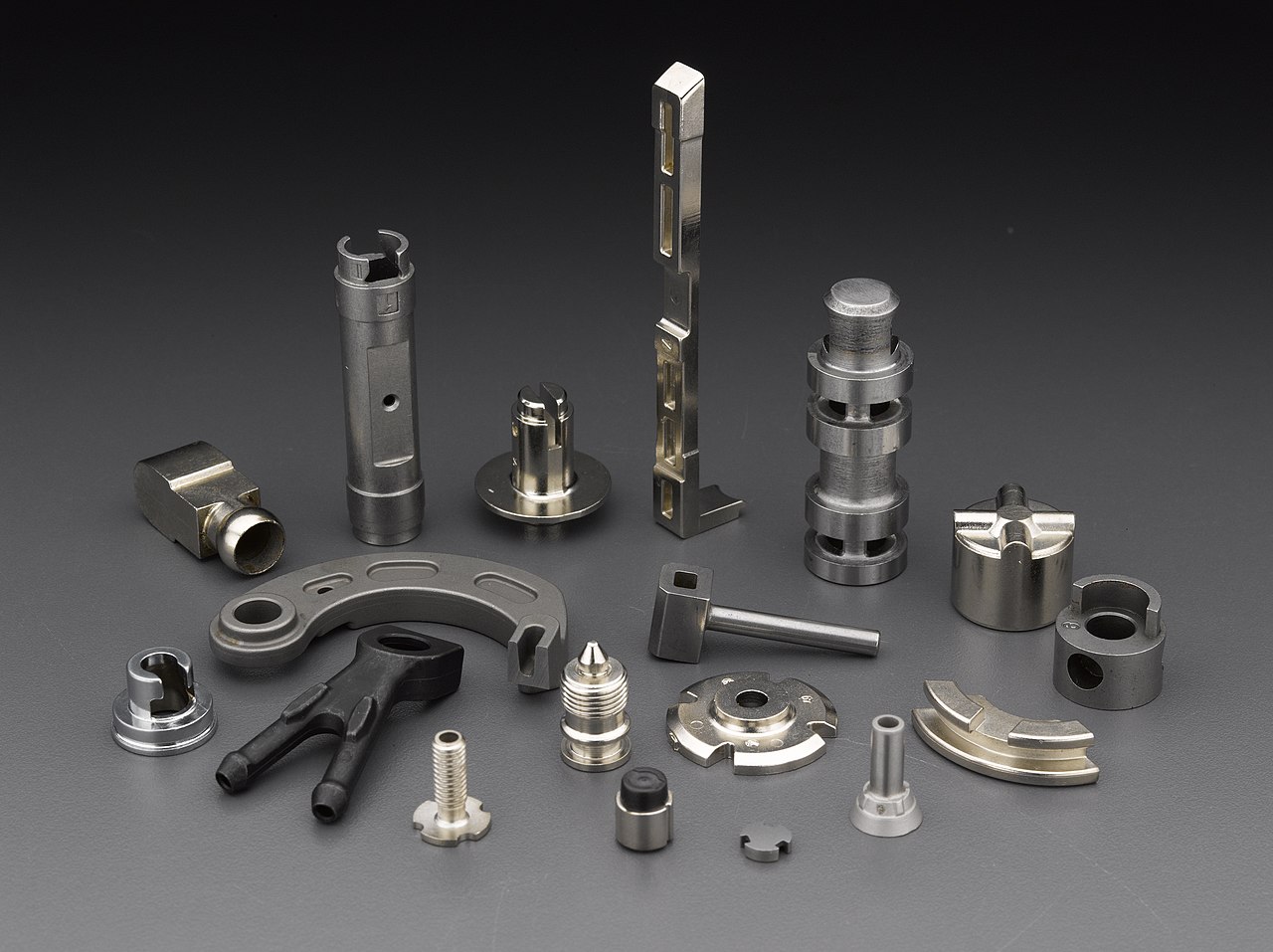
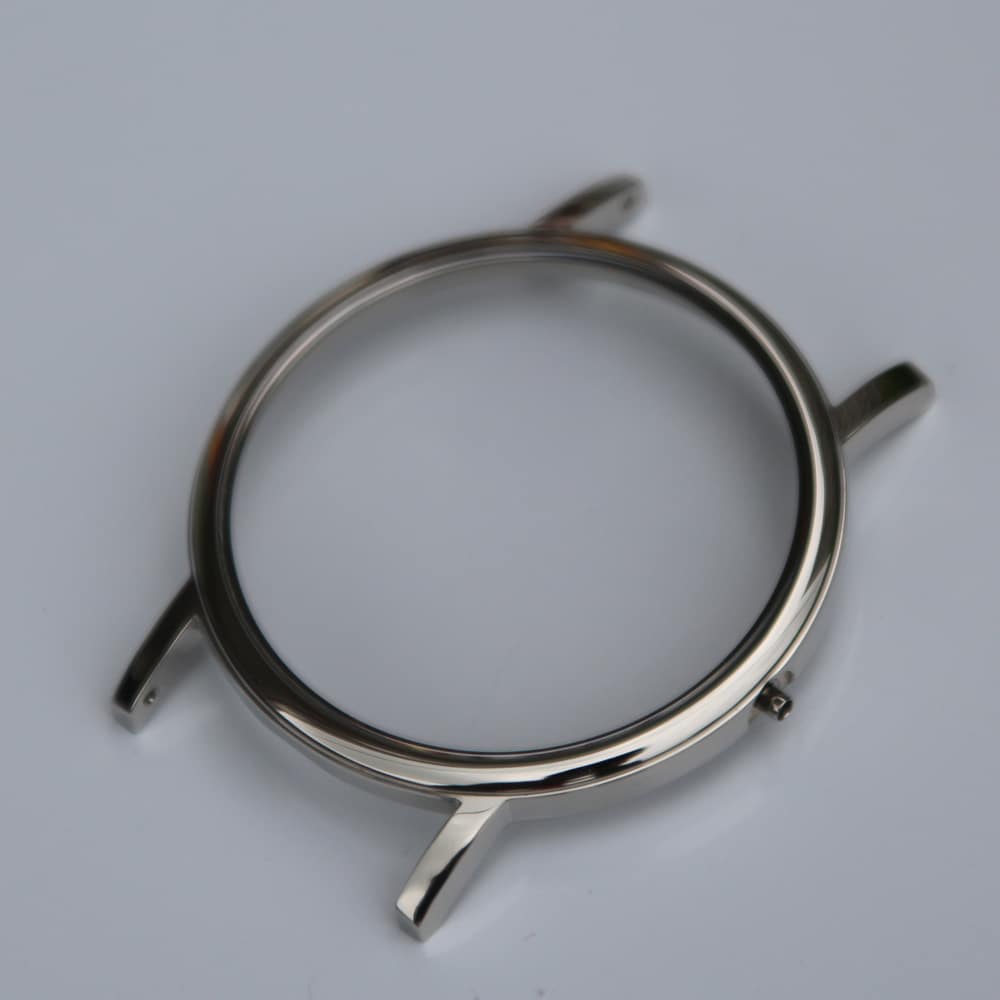
SYNERGIES AND BENEFITS OF CASTING USING HIP
Hot Isostatic Pressing (HIP) technology is capable of improving the mechanical properties of parts manufactured by MIM and of achieving 100% of the theoretical density.
Adding a HIP treatment to the parts manufactured by MIM allows new markets with higher mechanical requirements to be reached, the number of rejected parts to be reduced, the limits of MIM process variables to be relaxed and better processing times to be achieved.
On other occasions, the aim of applying HIP to MIM manufactured parts is to improve specific properties such as responsiveness to polishing, since the elimination of internal porosities allows for an improved final surface finish.
In addition, depending on the material, the heat treatments required by the component can be used in combination with the HIP.
Typical examples of HIP and MIM combinations:
In the field of jewelry and watches, parts manufactured by MIM are treated by HIP to improve the responsiveness of these materials to polishing. The decrease in the porosity of the metal (after HIP) allows for an exceptionally high quality polish. One of the most common uses is the watch case.
For weapons, some weapon components that are manufactured by MIM need to be further treated by HIP, which gives them the mechanical properties required of the material.