Oil & Gas
The Oil & Gas industry plays a fundamental role in supplying the world's energy needs from the extraction of fossil fuels, such as crude oil and natural gas. It is an industry driven by standards of efficiency, accuracy and reliability, in an often hostile environment and under extreme operating conditions.
That is why the materials used to manufacture the critical parts and elements of the facilities and equipment of the extraction plants must be of high quality, both to ensure the reliability of the extraction operations and to protect the environment.
The incorporation of HIP technology in the manufacturing process of the components makes it possible to improve their performance and increase their useful life, while lowering manufacturing costs and offering great flexibility when manufacturing parts with complex and sometimes large dimensions.
HIP applications in Oil and Gas: parts, materials and techniques
Hot Isostatic Pressing (HIP) technology has been used for many years in the oil and gas industry, mainly for the purpose of compacting parts manufactured in the powder metallurgy process from components close to their final shape, (Near Net Shaping, NNS), allowing for cost reductions (compared to the use of other traditional techniques such as machining), and expanding design options. Its use allows for more efficient work with duplex stainless steels such as 22Cr or 25Cr, super duplex or other nickel-based alloys.
The combination of powder metallurgy and HIP gives the materials greater resistance to corrosion and hydrogen induced stress cracking (HISC), a microstructure without anisotropy and fine grain, ensuring compliance with the most stringent quality standards of the offshore industry.
This sector, which has high demands in terms of integrity and quality, is driven by other factors such as the economy of the solutions it adopts and its versatility in facing new challenges and reaching new environments with maximum security. That is why this industry, in parallel to the aerospace sector, is incorporating elements produced by Additive Manufacturing (AM). At the present moment, still in its early stages, the incorporation of this technology is focused on the predictive maintenance of the equipment in production, "printing" the parts just before it is necessary to replace them, thus reducing downtime. It should be noted that some installations are quite old and there are no parts in stock to replace those that fail.
In the case of parts made by Additive Manufacturing, which are then treated with HIP to improve their microstructure, there is still a lot of room for improvement, since at the moment the same quality standards and identical treatment conditions are being applied to these parts as to "traditional" powder metallurgy parts, while the possibilities in this sector are very wide, both from the point of view of materials and process conditions. For this reason, a major commitment and investment is being made into R&D and the first exciting initiatives are already emerging.
Some of the most commonly used components in the oil and gas industry are manifolds, valves, undersea joints or pump components. The materials used are diverse, but the best options for this type of environment are duplex and super duplex stainless steels, austenitic stainless steels or nickel alloys.
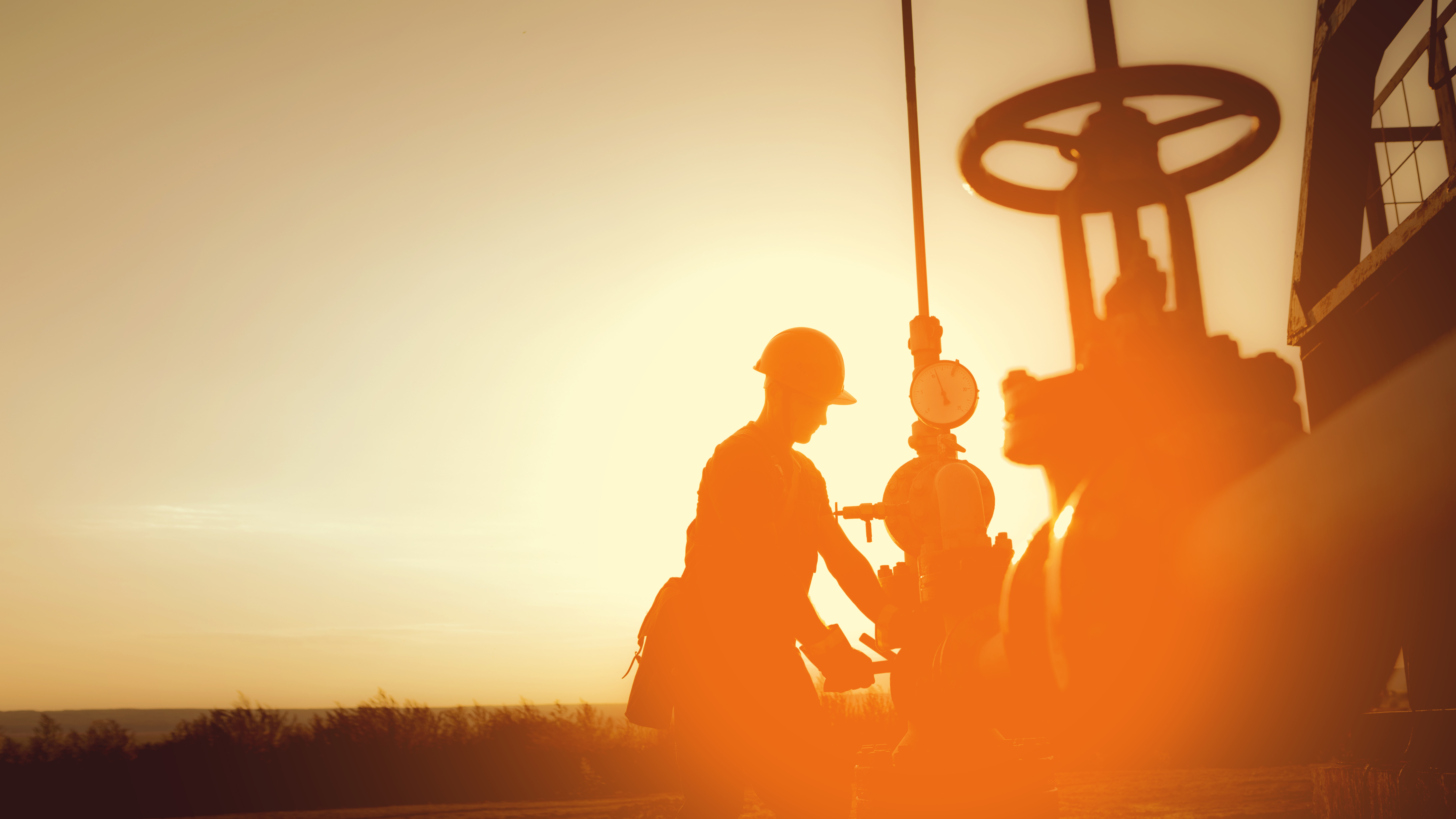
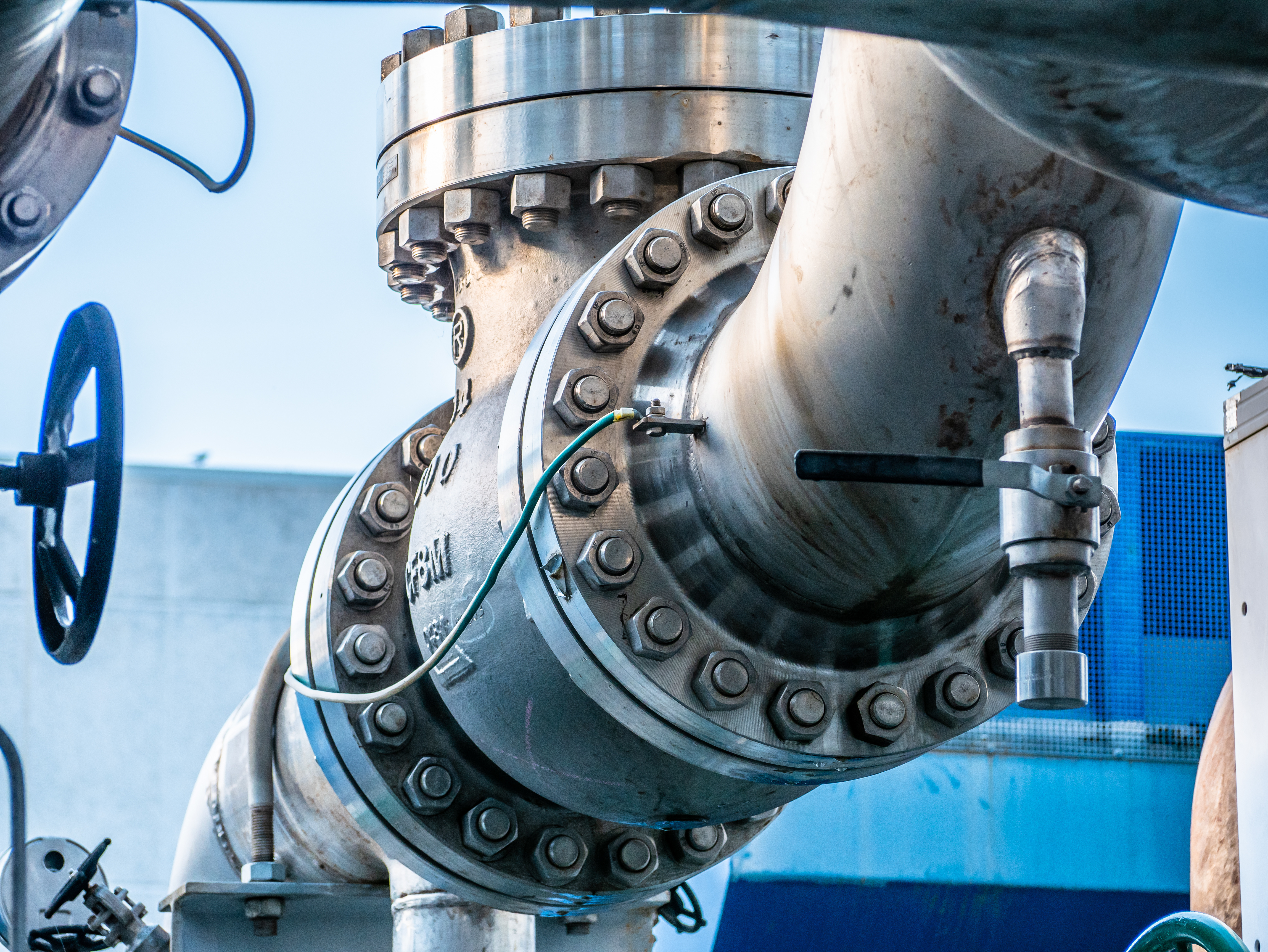
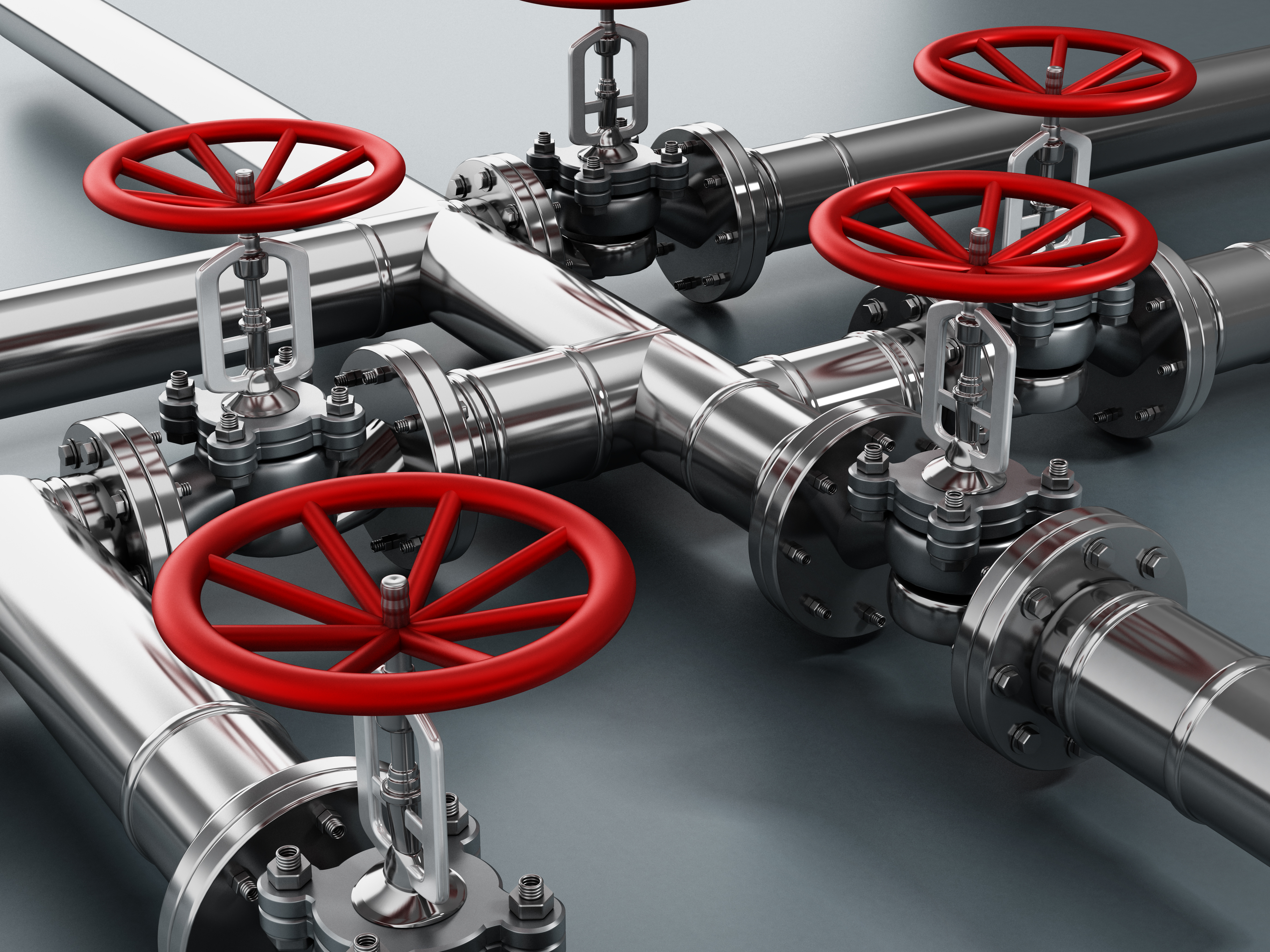
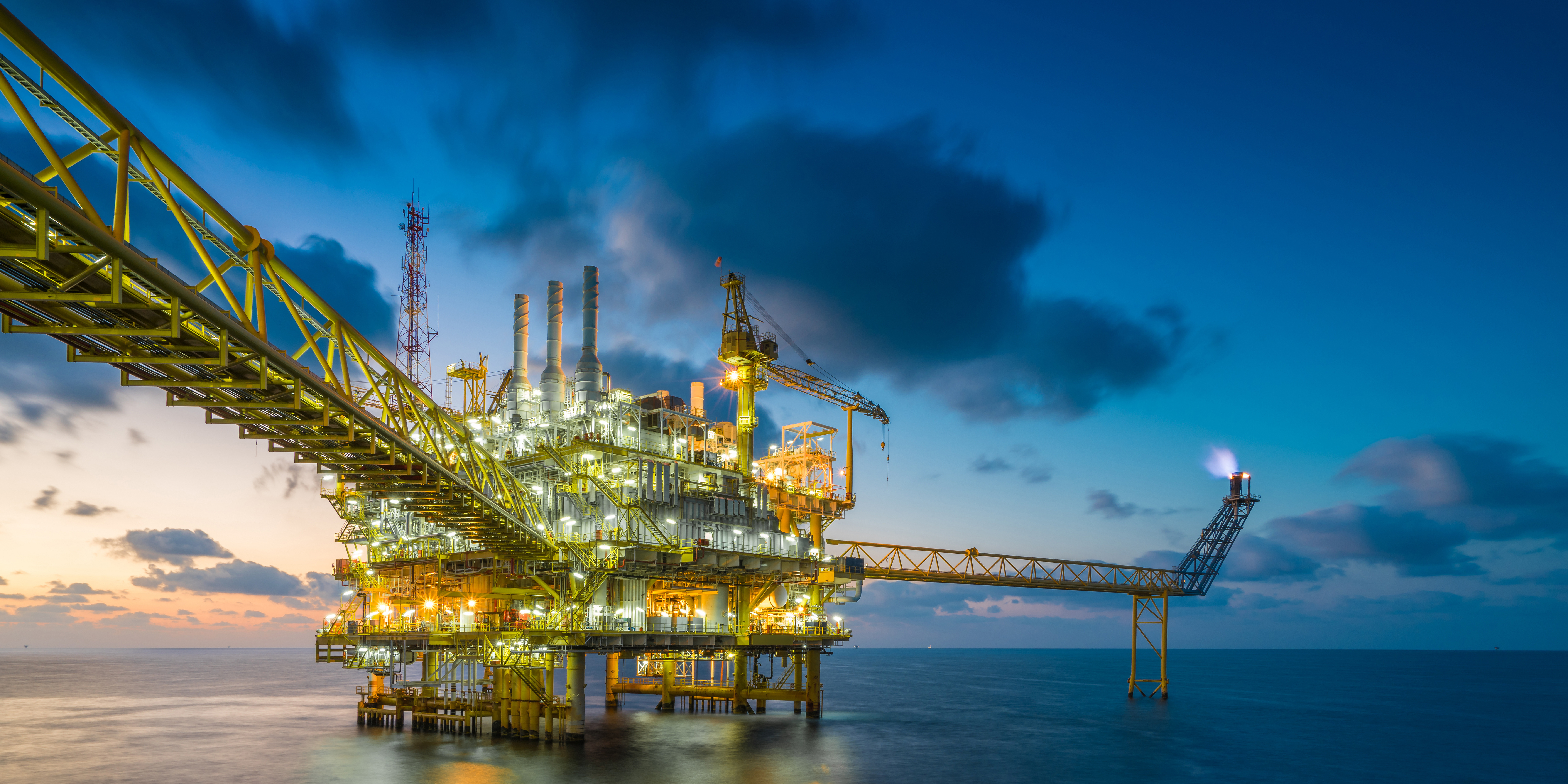
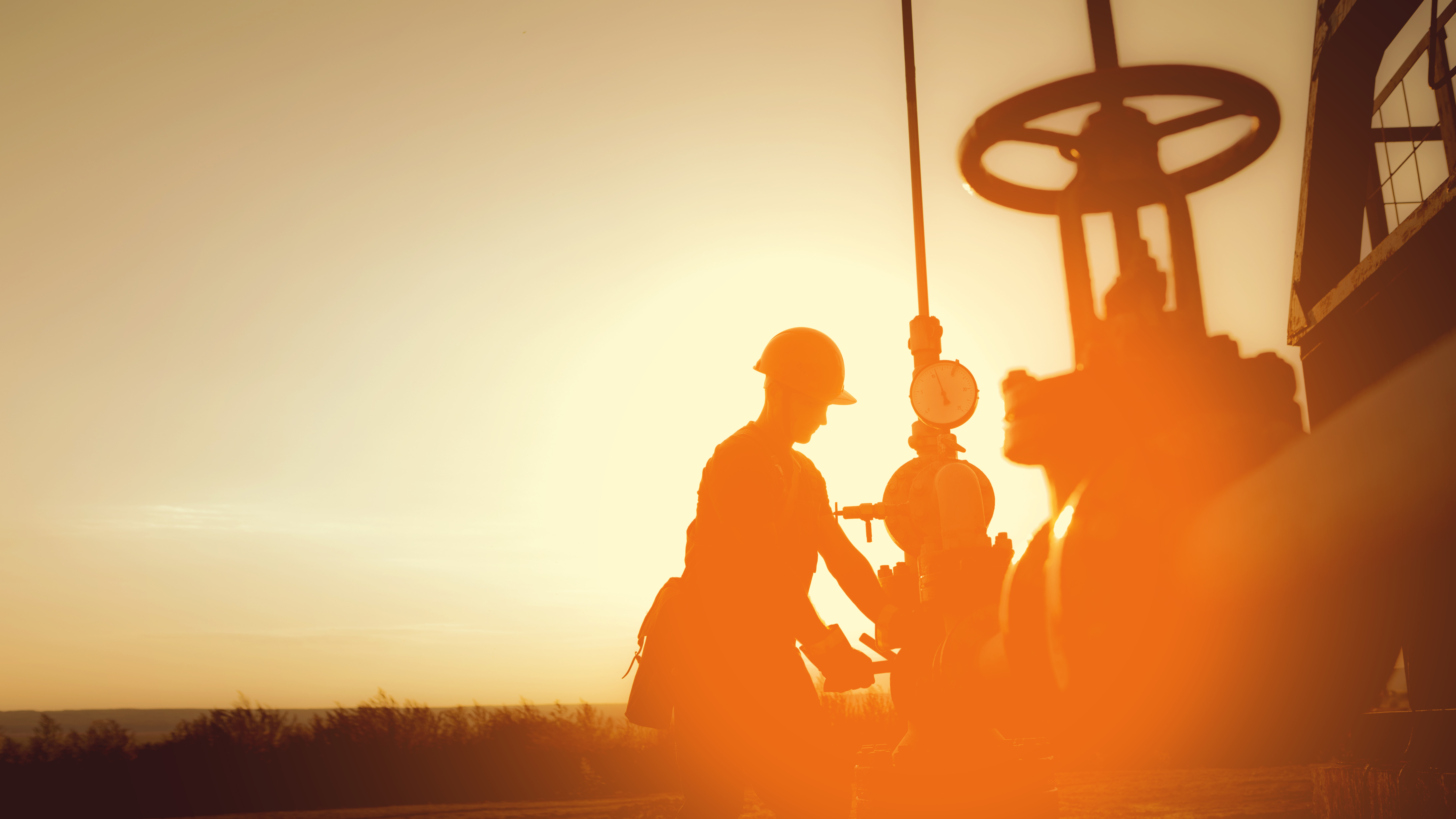
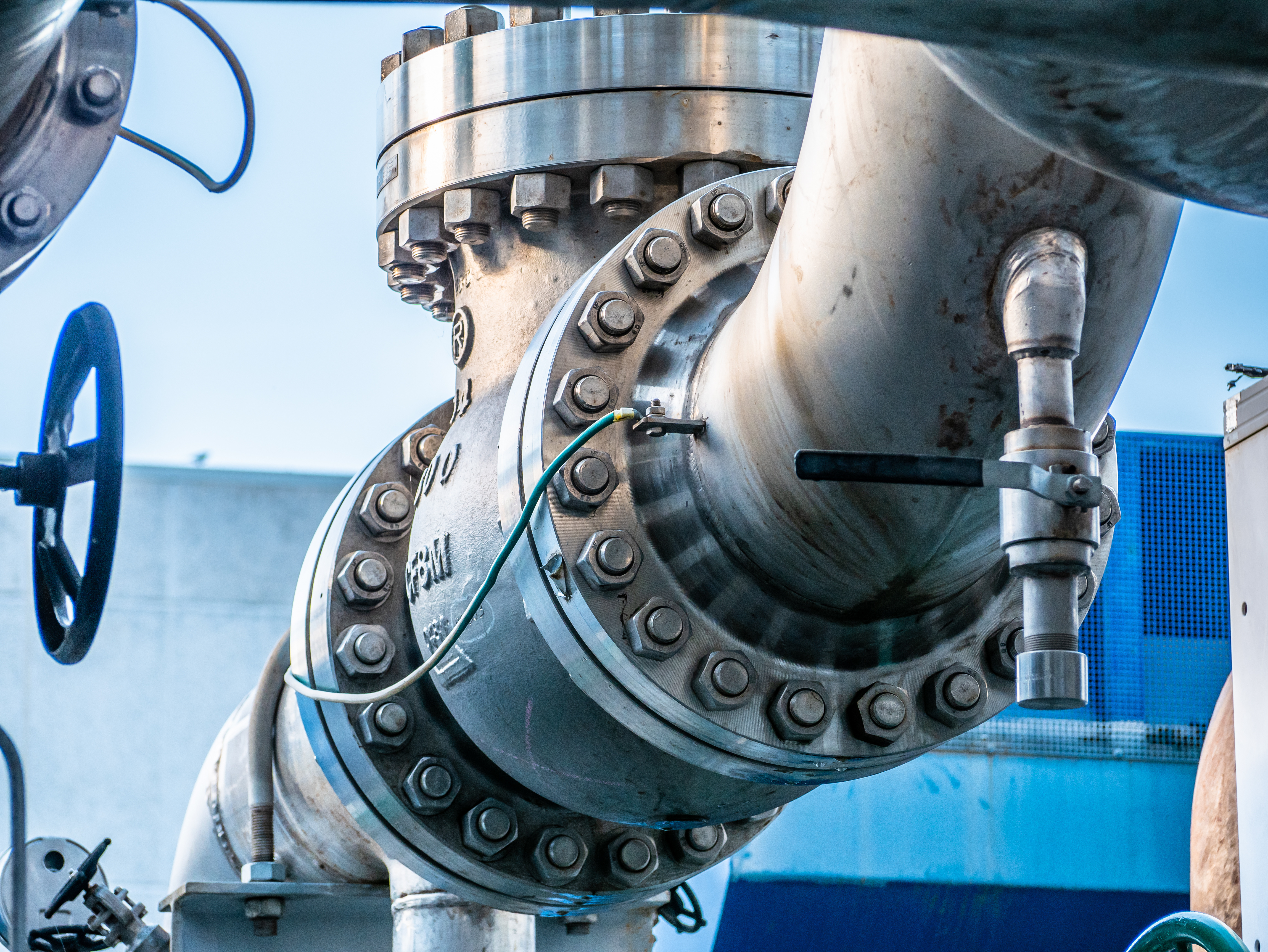
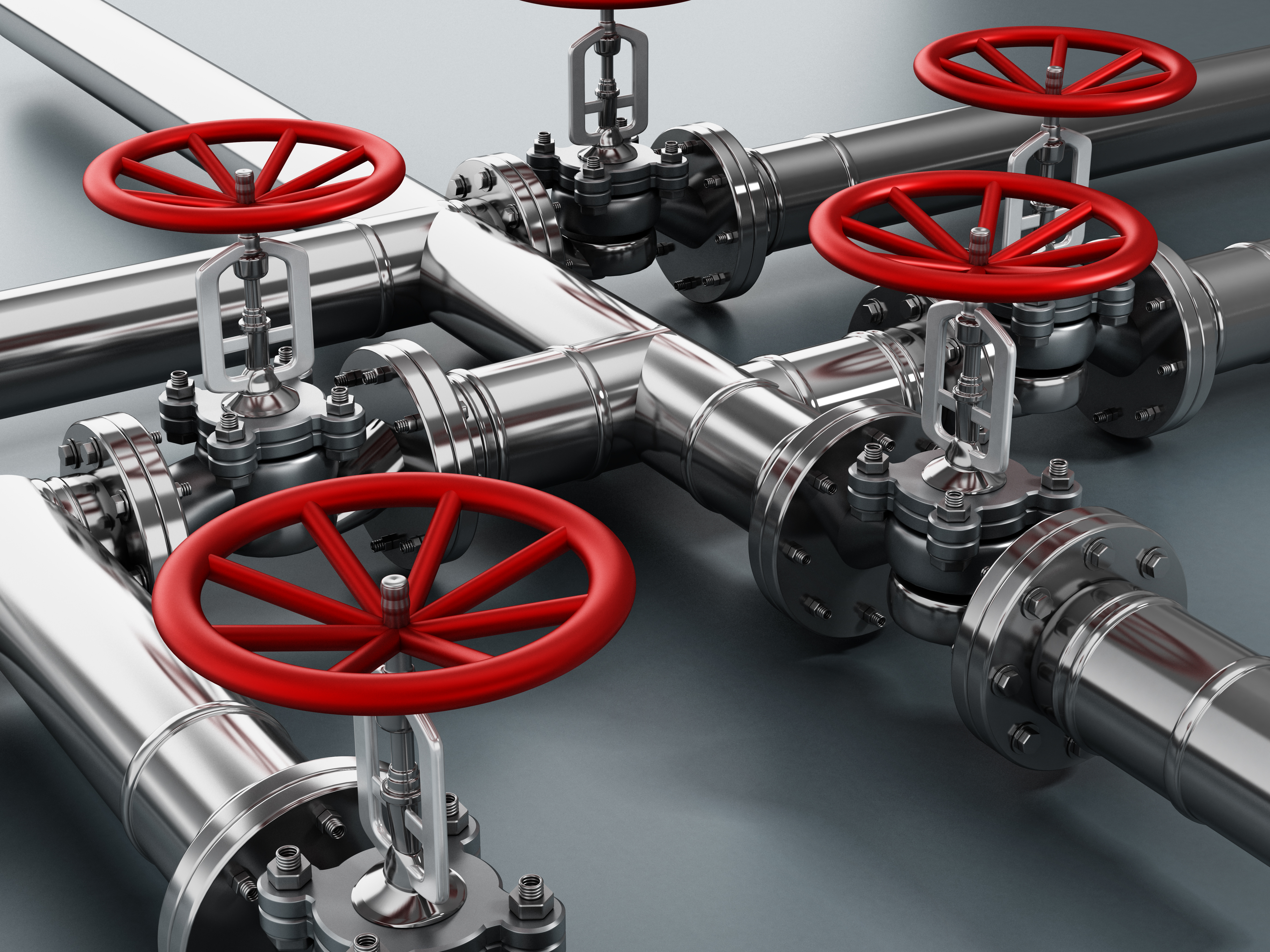
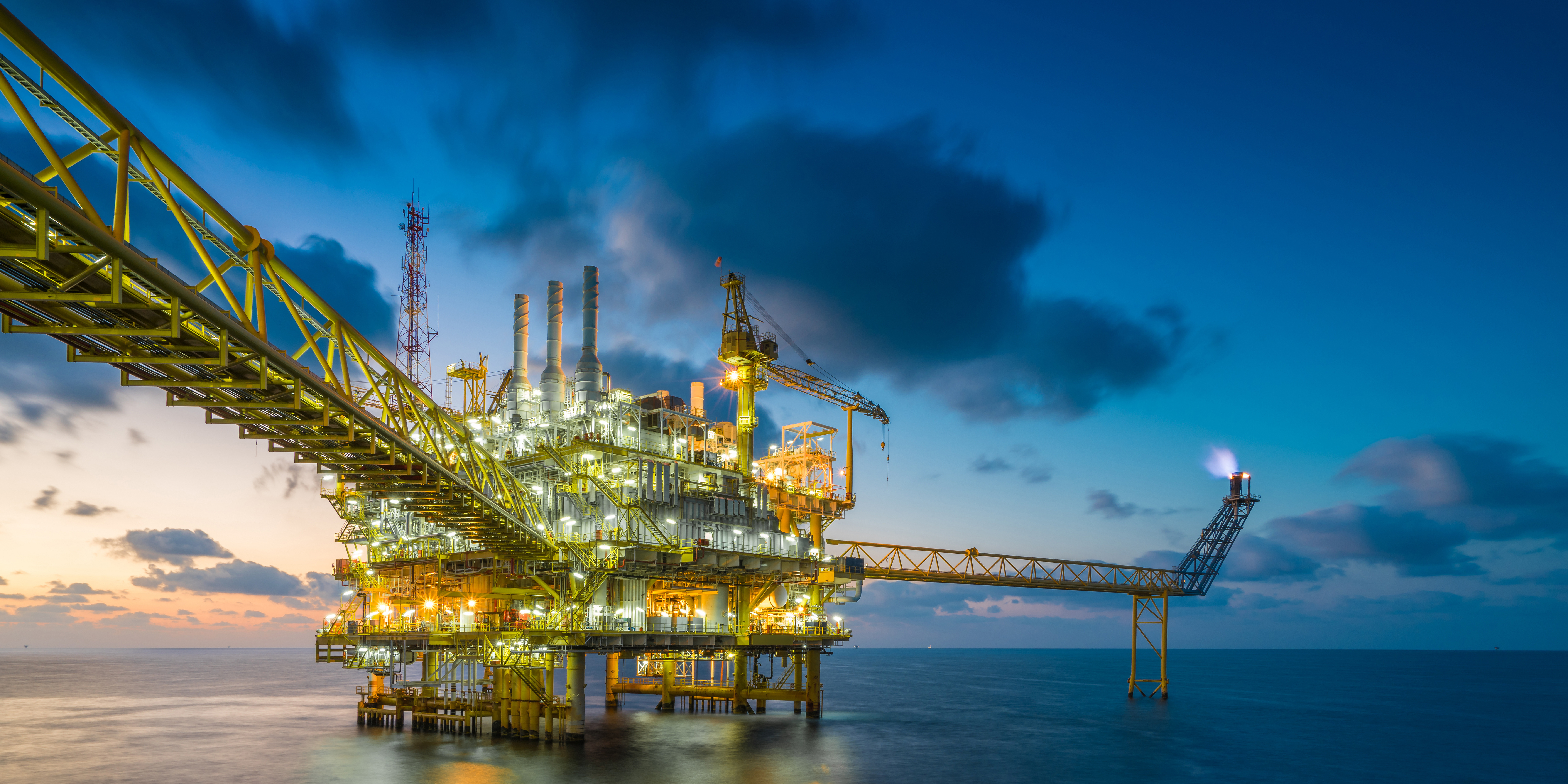
MAIN BENEFITS OF USING HIP
The use of HIP technology to manufacture parts designed by different manufacturing processes for the oil and gas industry brings the following benefits:
Improves material properties and performance:
- High resistance to corrosion and Hydrogen-Induced Stress Cracking (HISC) that it provides to the material.
- Improved options (versatility) and performance of component manufacturing processes, since in many cases it reduces the weight of the part.
- Allows for the design of large parts with complex shapes.
More efficient production in manufacturing processes:
- Minimizes the need for welding.
- Improves the use of material.
- Reduces machining operations to a minimum.
Cost saving:
- Reduces manufacturing costs.
HIP is proving to be an indispensable technology for this sector today, playing a vital role in meeting global energy needs, and will account for almost half of the primary energy supply in 2040.
Certificates
All materials and components used in the oil and gas industry must comply with the strictest quality controls, meeting a wide variety of requirements that allow them to fulfill their functionalities and qualities. Among them, the following manufacturing and control standards stand out.
- NACE MR 0175 ISO 15156 (NACE - National Association of Corrosion Engineers). Aimed at materials for use in environments with a high presence of hydrogen sulphide.
- NORSOK M-650, Rev. 3. Certification for manufacturers of special materials, such as those in the oil industry.
- ASTM A 988/A988 M, ASTM A 989, ASTM B 834 (ASTM – American Society for Testing and Materials). The standards to which those components (flanges, valves, stainless steel parts) processed by HIP that operate at high temperature must be held to.