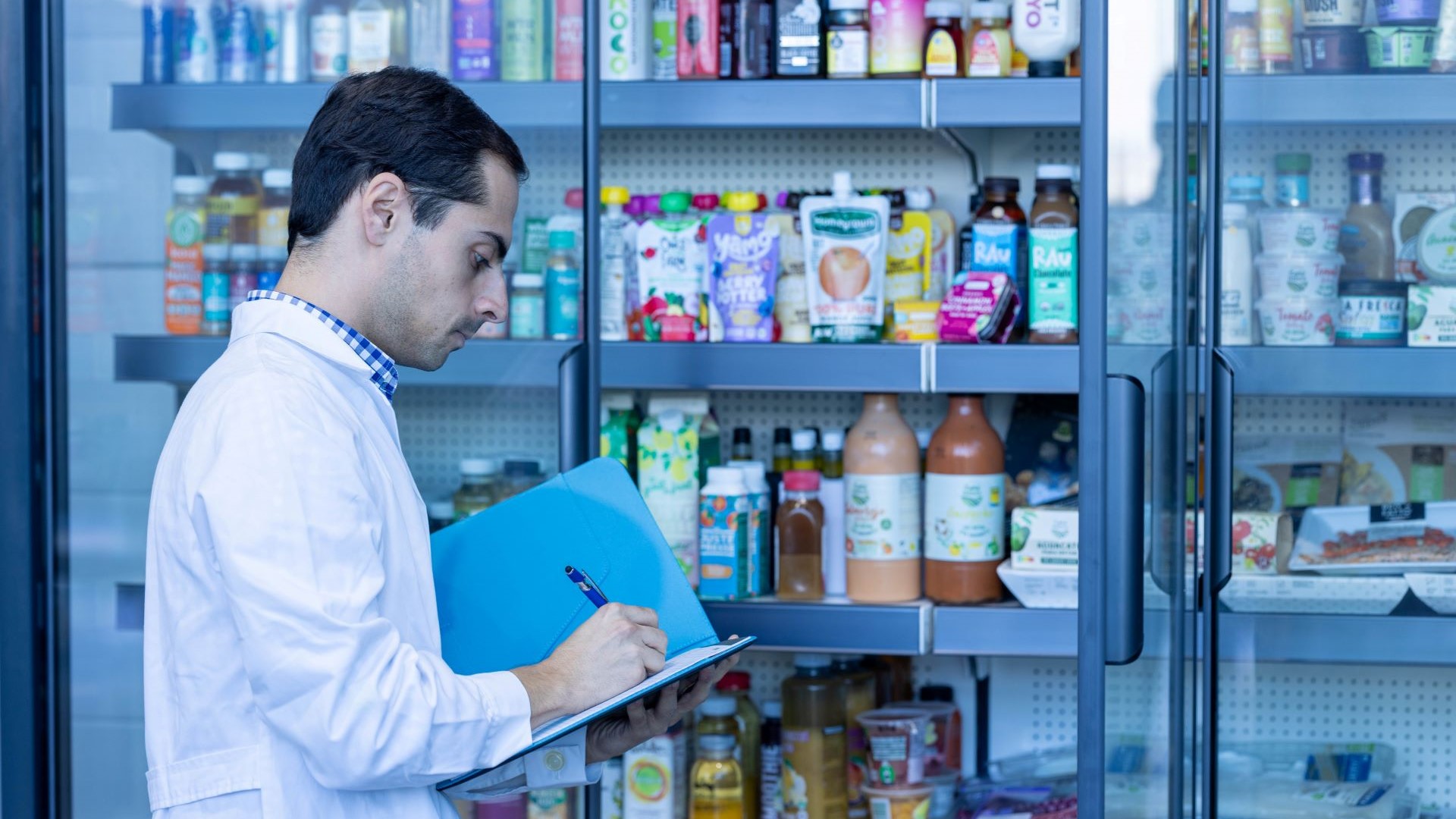
Getting Your Packaging HPP-Ready: What You Need to Know
High pressure processing (HPP) is a powerful tool for improving food safety and extending shelf life, while preserving freshness and quality. But if your packaging isn’t properly prepared for HPP, you won’t reap the full benefits. Here’s what you need to know:
Choose Materials Wisely
HPP is applied to pre-packaged food products, thus the properties and design of the packaging are important considerations. Packaging for conventional HPP is mostly limited to plastic polymers such as PET, PP, PE, PA or EVOH (alone or combined in different layers). Eco-friendly options such as rPET and PLA are also suitable.
Allow for Package Compression
Flexibility and elasticity are the most important characteristics for HPP packaging, as it should withstand compression under high pressure and recover its original shape upon pressure release. Packaging materials should also be water resistant.
Minimal Headspace
Minimizing headspace reduces the likelihood of packaging failure. Gas is more compressible than solids or liquids and occupies a much smaller volume under pressure. Upon decompression, gas molecules expand more violently and packaging is more susceptible to failure. In addition, the smaller the headspace, the higher the filling ratio of the HPP baskets and, consequently, the higher the performance of our HPP equipment in terms of productivity.
Test, Test, Test!
Test and validate your packaging! Hiperbaric offers complimentary HPP packaging trials and evaluations at our HPP Incubator and Pilot Plant facilities. Take advantage of this service to confirm your packaging performs well under pressure and avoid failures down the line. Hiperbaric also maintains a list of preferred suppliers for HPP-compatible packaging solutions.
HPP Packaging Formats: Which Option is Right for Your Product?
High pressure processing (HPP) is versatile – it can be used on products packaged in different formats and containers. When selecting HPP packaging, consider your product characteristics, target market, required shelf life, and processing needs.
Bottles
-
PET is the most suitable material for bottles.
-
ROUNDED CORNERS provide shoulder rigidity and less strain compared to edgy corners.
-
BOTTLE BASE inverted dome provides rigidity and structural support for smooth sidewall panels. A crown shape is used for carbonated drinks.
-
MINIMIZING THE HEADSPACE REDUCES negative chemical/enzymatic reactions and prevents bottle wall paneling.
-
PLA (POLYLACTIC ACID) is a biodegradable and compostable biopolymer with similar mechanical and gas barrier properties as PET.
Bottle Cap
-
HDPE is more compressible than PET and provides a tighter closure.
-
CAPS WITH INNER PLUG/EMBOSSMENT are preferred as the inner lip prevents fluid exchange during high pressure.
-
LINER SEALS IN THE CAP ARE NOT DESIRED as they may lead to leakage if the cap and liner materials compress/decompress at different rates.
-
FOIL CLOSURES & DISPENSER CAPS: The foil must be validated. The cap is placed after HPP to prevent water migration between the foil and the cap.
Tubs and Trays
-
ROUND OR SQUARED TUBS are used in a wide range of HPP applications: guacamole, salsas, spreads, dips, wet salads, fruit chunks submerged in juice, baby food, fruit purees, pet food, etc.
-
ROUNDED CORNERS increase the rigidity of the base and side walls, and reduces the likelihood of puncturing the closing film of adjacent tubs and trays during HPP or further handling.
-
TRAYS ARE THE PERFECT SOLUTION FOR READY-TO-EAT (RTE) meals, deli meats, cured and fermented sliced meats, fish filets, etc.
-
RIGID OR SEMI-RIGID CONTAINERS usually made of PET or PP that may be heated in microwaves or ovens.
Film
-
A PLASTIC FILM is heat-sealed to cover the opening of tubs/trays before HPP. The container lid is placed after HPP.
-
MICROWAVE & OVEN COMPATIBLE FILMS vent off steam to avoid packaging burst during cooking, but easily open at the time of consumption.
-
OXYGEN TRANSMISSION RATE (OTR): Low OTR slows down oxygen migration and maximizes shelf life, but 10K OTR films prevent toxin formation of spore pathogens in seafood products.
Bags and Pouches
-
VACUUM BAGS can be used for a wide range of applications: guacamole, avocado, fruit pulps, sliced deli meats and meat blocks, sausages, etc.
-
POUCHES ARE VERSATILE and a handy solution for soups, wet salads, salsas, baby food, juices, purees, Bag-In-Box (BIB), and pet food.
-
BAGS AND POUCHES MAXIMIZE THROUGHPUT since they minimize void space between packaged food units.
-
MULTILAYERED MATERIALS ARE COMPATIBLE and often preferred since they provide mechanical strength and serve as oxygen barriers, while pouches made of a single material are easier to recycle.
Fittings and Additaments
-
HEAT SEALING MUST BE OPTIMIZED: (>5 mm/0.19 in) to ensure that bags withstand compression and decompression.
-
FITTINGS like spouts, screw, caps, valves, zippers, etc. are also compatible with HPP pouches, but prior validation of the design is encouraged.
-
BAG-IN-BOX (BIB), STAND-UP & INVERTED POUCHES facilitate product dispensing of large packaging presentations.
-
HANDLES on top and bottom panels simplify handling and transportation.
Test Your Packaging with Hiperbaric!
Launching a new product with HPP? Packaging failure could derail your whole project. Why leave anything to chance? Test your packaging at Hiperbaric’s HPP Incubator and Pilot Plant facilities – for FREE. Receive expert guidance as we put your packaging through its paces with high pressure processing trials.
-
Confirm your packaging withstands 87,000 PSI pressure
-
Check for leakage, seal integrity issues, and deformation
-
Validate shelf life extension meets your requirements
-
Make adjustments before full production
Hiperbaric has unparalleled expertise in HPP applications and packaging solutions. Trust us to properly evaluate your packages and avoid costly mistakes down the line. Contact Hiperbaric to schedule your free packaging trials today!