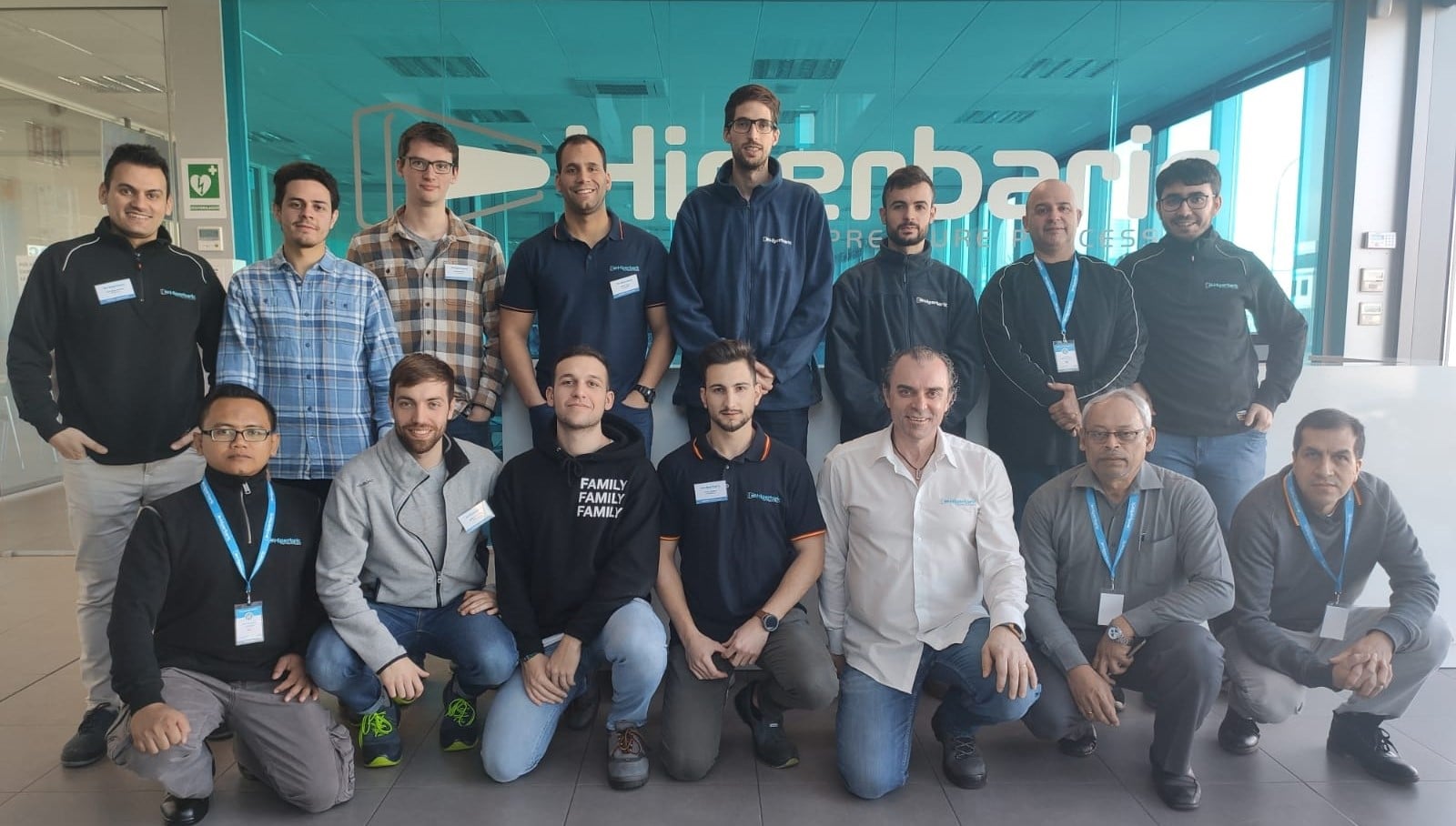
Hiperbaric, headquartered in Burgos, Spain, has held its long-awaited “Training course in the operation of HPP system”, which since 2015, has brought more than fifty professionals together. Some the most interesting topics during the training included the general vision of the industrial equipment, maintenance of the machinery, and the continuous support of the Hiperbaric After-Sales Portal.
Throughout the 20 years of Hiperbaric’s life, the company’s team, made up of highly qualified professionals, has become one of the most authoritative and prestigious voices in High Pressure Processing (HPP) Technology for the food & beverage industry worldwide. This is because at Hiperbaric, we design 100% of the components that make up our advanced HPP units (vessels as well as intensifiers). For this reason, we have become the undisputed leaders in high pressure processing technology, with a market share of over 60% and almost 300 industrial machines installed in five continents.
With the aim of sharing the experience and knowledge about High Pressure equipment, Hiperbaric celebrates every year with its customers the “Training course in the operation and maintenance of HPP system”, presented in English and another in Spanish. Since 2015, more than fifty professionals from different companies and food sectors, participate in the various theoretical-practical sessions to deepen the mastery of Hiperbaric’s industrial equipment. The latest training course took place last March, and brought together a large group of maintenance professionals in several sessions given by Hiperbaric’s own HPP experts.
The overview of HPP equipment and its operation is the cornerstone of the training. The entire HPP In-pack and Bulk range is analyzed to ensure that it achieves maximum performance and key machine components are covered in depth. Topics range from the technical advantages of our design, through maintenance, reliability and spare parts service.
Key components and operations of HPP system
Broadly speaking, the main structural elements of the HPP In-pack system (up to 5 different process chamber sizes: between 55 L and 525 L) are composed of the vessel, yoke, caps and wedges, intensifiers, high-pressure tubes and multiple safety mechanisms.
Among these components, the intensifiers in charge of the generation of high pressure water take on special relevance. Thanks to our design as independent and redundant units, they allow the machine to continue producing the equipment, while maintenance is carried out in an intensifier. This design allows us to achieve high reliability.
Also, critical components are the elements that transport the water, high pressure tubes and fittings, as well as the devices that control the release of the pressure: the discharge valves.
As explained in multiple articles in this blog, High Pressure Processing (HPP) is a non-thermal preservation method in which food, in its flexible final packaging, is introduced into a steel vessel and subjected to high levels of isostatic pressure (300-600 MPa/43,500-87,000psi/6000 bar), transmitted by water (in this video, you can see the operation of an HPP unit).
Due to these very high pressure levels, all materials and major components of the HPP system are under great stress, and therefore, some of them have to be replaced often. In order to guarantee the operation of the process without interruptions, one of the most important aspects is to ensure the correct maintenance of the pressure during the cycle by controlling possible leaks in the circuit.
This involves carrying out key operations that require training of maintenance technicians. This training is given by Hiperbaric technicians during the installation and start-up phase. The “Training course in the operation of HPP system” allows to reinforce this first training and to train the new technicians of our customers. Besides, these operations are described and recorded in videos accessible to our clients from Hiperbaric’s web portal.
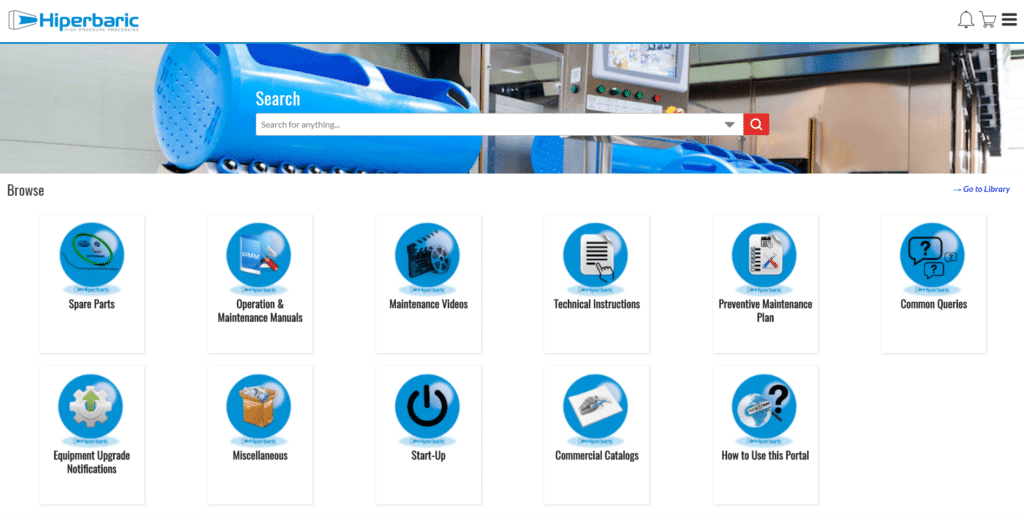
Preventive maintenance and our own spare parts service
All preventive maintenance operations are necessary for the proper functioning of industrial equipment. In particular, the aim is to increase the efficiency of the machines, which reduces the downtime that can influence production. In this sense, the most relevant operation has to do with the alignment of the vessel with the caps. In the case of corrective maintenance, the operator will focus on the minimum breakdowns that may arise during production, in which he will be supported by the spare parts and components developed by Hiperbaric (included in our continuous improvement program). Dependability, immediate availability of parts and the accompaniment of our customers throughout the life of the equipment are key to our company.
Safety and accuracy of HPP units
When an HPP machine is fully operational, another key element of the process is safety. For this reason, the machines have sophisticated pressure transducers that guarantee food safety, as well as motion transducers located in the vessel to ensure process stability. The information obtained from operations is collected in the SCADA System. This is a database that records and stores all the information on the machine’s production cycles: traceability data (product, recipe, operator, etc.) as well as process data (pressure, temperature, time, alarms, etc.).
Our customers in the food and beverage sectors, located geographically around the world and remotely, access this information through a web interface, where they can consult the data and extract it through accurate and precise reports to evaluate productivity.
On a day-to-day basis, Hiperbaric’s team and after-sales service attends in real time to the needs of customers around the world with speed and efficiency, through a direct 24/7 after-sales program. “Being decisive, efficient and close is the added value that we provide and that our customers appreciate the most”, says Eder Gutiérrez, responsible for After-sales. “Therefore, when we give these courses at Hiperbaric’s headquarters, the results are always excellent, as they allow us to strengthen the bonds with the people responsible for the maintenance of the equipment”.
If you want to know more about HPP and how it can improve the safety and quality of your food & beverage products or if you’d like to speak with our after-sales or commercial department, contact us.