
Hiperbaric has organized its long-awaited “HPP equipment operation and maintenance training course”, which has been held since 2015. A reflection of the added value and customer orientation that characterizes the 24/7 after-sales service offered by specialized HPP engineers. In addition, this initiative demonstrates the importance that the company attaches to the maintenance of HPP equipment and is a way to strengthen ties with the people who will be working on a day-to-day basis with our equipment. Customers have expressed their satisfaction at the end of the training.
Hiperbaric’s after-sales service, a synonym of reliability and customer focus
Throughout Hiperbaric’s 20 years of existence, reliability and customer focus have been two values that have been present throughout the company’s history.
Customer orientation covers all phases of the value chain, from equipment production to marketing and installation, with after-sales service included for life, in order to guarantee product and service quality. In addition, the aim is to achieve close and continuous collaboration with the customer and to support his technological investment efforts.
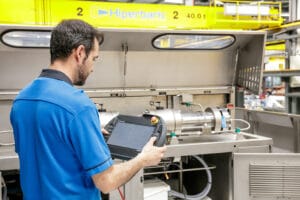
Indeed, after-sales service is one of the aspects that best reflects the combination of reliability and customer focus that has made us the undisputed leader in technology, with a market share of over 60% and nearly 350 industrial machines installed on all five continents.
About Hiperbaric’s after-sales service
Hiperbaric’s after-sales service is the key factor in our success and that of our customers. Our customers have a 24/7 toll-free line available from anywhere in the world, any time of the day and any day of the week, with a team of engineers dedicated entirely to HPP technology. This availability and flexibility allow us to maximize the productivity/availability of their HPP equipment, minimizing waiting times and reducing operational/maintenance costs.
This telephone support is complemented by on-site assistance from our specialists at the customer’s premises in the event of serious incidents. Our specialists are also responsible for the installation and commissioning of all our equipment at the customer’s premises, an opportunity which is used to provide on-site training for our customers’ maintenance managers.
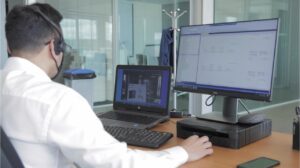
Spare Parts
Hiperbaric is responsible for the production of 95% of the components to control its production process and include them in its continuous reliability improvement programs.
Promptness is a premise in this service. Our commitment is to ship in less than 24 hours to anywhere in the world. It is also a 24/7 service, with original and specific spare parts supplied from our 4 warehouses: Spain, United States, Mexico, and New Zealand.
Hiperbaric Portal
At Hiperbaric, we provide our customers with a web portal for exclusive use, where they can place their orders in real-time with the guarantee of being processed within 24 hours. It has access to an extensive database of technical information such as manuals, instructions, and common queries. It also allows you to check prices, download online offers, and perform simple searches for spare parts through interactive 3D navigation.
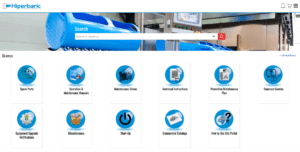
The importance of proper maintenance of HPP equipment
Proper maintenance of HPP equipment is essential to achieve maximum performance. Due to the high pressure levels, all materials and main elements of the HPP equipment are highly stressed, and therefore some of them have to be replaced frequently.
Carlos Pampliega, Hiperbaric’s after-sales manager, states, “In addition to the after-sales service, performing the appropriate maintenance on HPP equipment is crucial to extend its useful life, maximize its productivity and minimize downtime.”
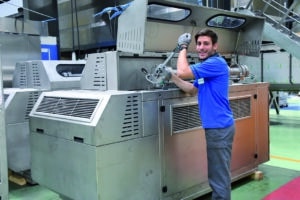
This involves key operations that require training of maintenance technicians. That is the reason why every year we offer two training courses given by our after-sales engineers to all our customers.
Operation and maintenance training course for HPP equipment
With the aim of sharing experience and knowledge about High Pressure Processing equipment, Hiperbaric holds every year with its customers the “Training course in the operation and maintenance of HPP equipment”, with one course in English and another in Spanish. Since 2015, professionals coming from different companies and food sectors participate in varied theoretical-practical sessions to deeply master Hiperbaric’s industrial equipment. The contents include explanations on the main components of the machines and the most common and periodic maintenance actions. The classes are divided between theoretical sessions and more hands-on sessions in the workshop where the guests practice what they have learned under the supervision and advice of Hiperbaric’s specialists.
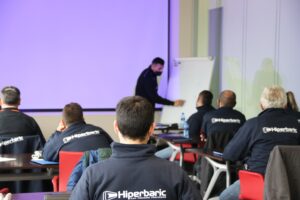
The last course of the training took place last November and was attended by a large group of maintenance professionals, in several sessions given by Hiperbaric’s expert employees.
“Each year, Hiperbaric organizes two training courses at our facilities in which we invite our clients’ maintenance managers”, explains Carlos Pampliega. “The result is always exceptional since it allows us to educate and strengthen relationships with the individuals who will be working with our HPP machines day in and day out.”
Customers are also satisfied after the course. Amor Bustos Peralta, quality manager at Frutas Los Cursos, was one of the participants in this latest course. Amor states, “This training has helped me to consolidate the concepts of how the machine works and how to detect faults in it. I thank Hiperbaric for opening its doors to us, and the entire after-sales team for the treatment offered.”
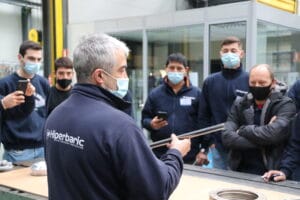
Elmer Villanueva Aguilar, handler and HPP maintenance manager at Naturae said, “This training is a great commitment from Hiperbaric to its customers; and in my particular situation as a production technician, a great complement to my working life”.