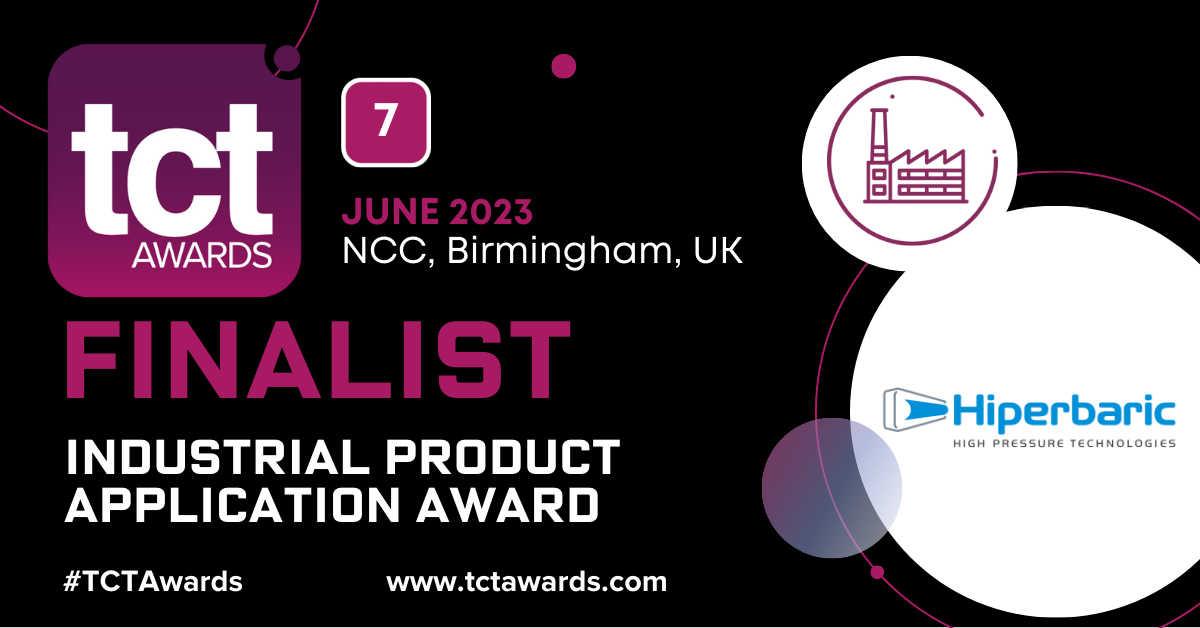
Hiperbaric has been announced as a finalist of the TCT Awards in the category TCT Industrial Product Application Award. The innovation presented was the design and development of a heat exchanger, made by AM in a copper alloy (GRCop-42) which is post-processed with HIP and assemblied in Hiperbaric industrial HIP presses as a key component. In a few word is what we like to call HIP for AM & AM for HIP. With this design innovation, peak cooling rates of up to 1000°C/min are expected. This drastically reduces costs and cycle times of our HIP presses, as well as having a direct and determinant impact on the microstructure of the treated parts. We are grateful for this prestigious recognition that highlights our commitment to innovation and excellence in the field of Hot Isostatic Pressing (HIP) technology.
About the TCT Awards
We are proud for this prestigious recognition that enhances the tremendous work of our R&D engineering team in the field of Hot Isostatic Pressing (HIP). To give a little bit of backgroung, the TCT Awards is an annual event that recognizes the best examples of additive manufacturing, 3D printing, design, and engineering across the globe. The awards celebrate the innovators, technologies, and collaborators behind these achievements. The event showcases world-leading projects and recognizes the most influential and impactful members of the additive manufacturing industry. The TCT Awards 2023 edition were celebrated on June 7, 2023, at the National Conference Centre in Birmingham.
Industrial Product Overview, Uniqueness and Originality
Hiperbaric, global leader in high pressure technologies offering industrial equipment, including Hot Isostatic Pressing (HIP), has designed and developed a heat exchanger, made by AM in a copper alloy (GRCop-42). The heat exchanger is part of the XtremHIP project, which takes full advantage of the benefits offered by 3D printing, such as design freedom, and the unique properties of this copper alloy developed by NASA.
With this design innovation, peak cooling rates of up to 1000°C/min are expected. This drastically reduces costs and cycle times, as well as having a direct and determinant impact on the microstructure of the treated parts.
HIP is well known in the AM industry as this post process improves the properties of 3D printed parts for the most demanding sectors. With this innovation, not only will HIP help AM, but also AM will be the key to building more efficient HIP presses.
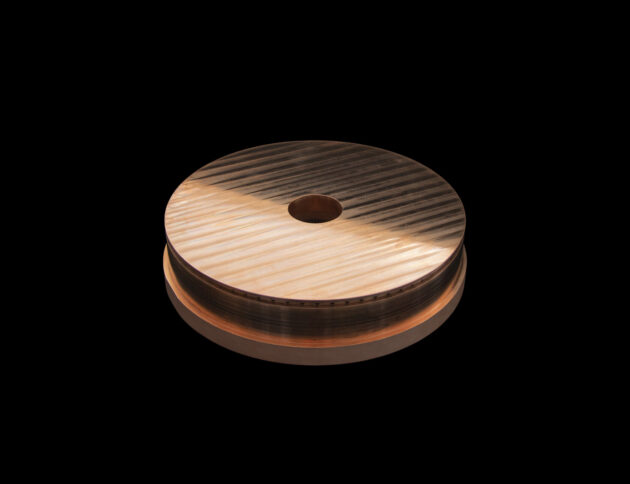
The heat exchanger is unique as it is designed to enhance heat flux and withstand pressures up to 30,000 psi (2,070 bar) using a complex manufacturing process, tailored to obtain good thermal conductivity and mechanical properties. One of the key steps in this manufacturing process has been the HIP process of the part itself, so the circle has been closed: the heat exchanger, manufactured by AM, has required a HIP treatment, and in turn, it will be used to HIP AM parts.
Hiperbaric is the first HIP equipment manufacturer to incorporate a heat exchanger made 100% by AM in their presses. The part has been created by laser powder bed fusion (LPBF), with a NASA alloy: GRCop-42. Thanks to the design freedom offered by AM and the properties of the GRCop-42 alloy, ideal for high heat flux applications, a heat exchanger has been developed to reach peak cooling rates of up to 1000°C/min.
There are other systems on the market based on heat sinks that absorb energy during the cooling stage, but this requires some idle time between cycles before this sink is cold again. Using a water/gas heat exchanger overcomes this problem and thanks to additive manufacturing its size can be minimized in order to increase press useful volume.
Impact of the innovation
Metals often require several processes and treatments to achieve final properties that meet the needs of the applications for which they are designed. These processes increase the cost and manufacturing time and each process is usually performed in different locations, which also increases lead times: stress relieving, solubilizing, aging… and also HIP. But what if we could combine these treatments into one process?
HIP is an essential treatment in AM parts to cover the most demanding needs and thanks to this innovative concept, we will be able to combine several of these processes within the same equipment and in a single cycle. Advantages include:
- Economic and Energy savings: It avoids transport and displacement between the different equipment and reduces the number of intermediaries. In addition, a post-treatment in each equipment requires starting from scratch, which means a higher energy and resource expenditure.
- Reduced Manufacturing Time and Delivery Times: Combining several processes into one reduces manufacturing time and therefore a quicker lead time of delivery.
- R&D: It opens the window to a wide range of possible combinations, being of great interest for the development of new applications.
Materials used
Material used is based on criteria such as good thermal conductivity, and also good mechanical properties. The first helps to improve thermal flux, reduce gradients and thermal induced stresses while the latter is required to cope with the high isostatic pressure to be withstood by the part. Among the materials that meet these specifications, GR-42 has been chosen.
Although the GRCop-42 alloy was developed by NASA in 1987 for aggressive environments, such as the combustion chambers of rocket engines, it was not until just 6 years ago that the parameters for its use in AM began to be developed. This copper-based alloy with 4 at. % Cr and 2at. % Nb has a high resistance and conductivity, typical of copper alloys, which together with the efficient design of the heat exchanger allows such high cooling rates to be achieved.