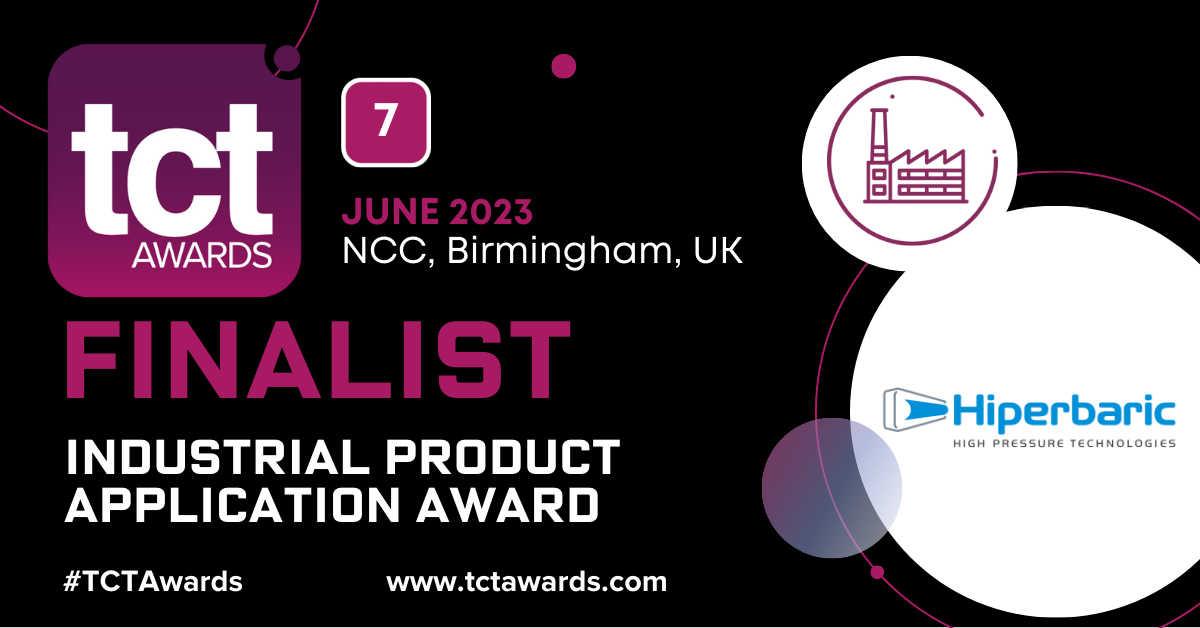
Hiperbaric ha sido nombrado finalista de los TCT Awards en la categoría TCT Industrial Product Application Award. La innovación presentada fue el diseño y desarrollo de un intercambiador de calor, fabricado por Fabricación Aditiva en una aleación de cobre (GRCop-42) que es post-procesado con HIP y ensamblado en las prensas industriales HIP de Hiperbaric como uno de los componentes clave. En pocas palabras es lo que nos gusta llamar HIP para AM & AM para HIP. Con esta innovación de diseño, se esperan velocidades de enfriamiento máximas de hasta 1000°C/min. Esto reduce drásticamente los costes y los tiempos de ciclo de nuestras prensas HIP, además de tener un impacto directo y determinante en la microestructura de las piezas tratadas. Agradecemos este prestigioso reconocimiento que pone de relieve nuestro compromiso con la innovación y la excelencia en el campo de la tecnología de prensado isostático en caliente (HIP).
Sobre los TCT Awards
Estamos orgullosos de este prestigioso reconocimiento que realza el tremendo trabajo de nuestro equipo de ingeniería de I+D en el campo del prensado isostático en caliente o HIP (del inglés Hot Isostatic Pressing). Los premios TCT son un evento anual que reconoce los mejores ejemplos de fabricación aditiva, impresión 3D, diseño e ingeniería en todo el mundo. Los premios reconocen a los innovadores, las tecnologías y los colaboradores que están detrás de estos logros. El evento muestra proyectos líderes en el mundo y reconoce a los miembros más influyentes e impactantes de la industria de la fabricación aditiva. La edición 2023 de los TCT Awards se celebró el 7 de junio de 2023 en el National Conference Centre de Birmingham.
Descripción general del producto industrial, singularidad y originalidad
Hiperbaric, líder mundial en tecnologías de alta presión que ofrece equipos industriales, incluido el Prensado Isostático en Caliente (HIP), ha diseñado y desarrollado un intercambiador de calor, fabricado por Fabricación Aditiva (FA) en una aleación de cobre (GRCop-42). El intercambiador de calor forma parte del proyecto XtremHIP, que aprovecha al máximo las ventajas que ofrece la impresión 3D, como la libertad de diseño, y las propiedades únicas de esta aleación de cobre desarrollada por la NASA.
Con esta innovación en el diseño, se esperan velocidades de enfriamiento máximas de hasta 1.000 °C/min. Esto reduce drásticamente los costes y los tiempos de ciclo, además de tener un impacto directo y determinante en la microestructura de las piezas tratadas.
El HIP es bien conocido en el sector de la AM, ya que este postproceso mejora las propiedades de las piezas impresas en 3D para los sectores más exigentes. Con esta innovación, no sólo el HIP ayudará a la AM, sino que la FA será la clave para construir prensas HIP más eficientes.
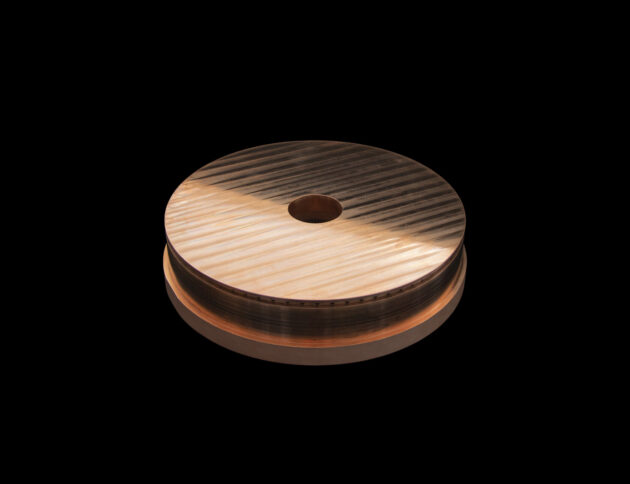
El intercambiador de calor es único, ya que está diseñado para mejorar el flujo de calor y soportar presiones de hasta 30.000 psi (2.070 bar) mediante un complejo proceso de fabricación, adaptado para obtener una buena conductividad térmica y excelentes propiedades mecánicas. Uno de los pasos clave de este proceso de fabricación ha sido el proceso HIP de la propia pieza, con lo que se ha cerrado el círculo: el intercambiador de calor, fabricado por FA, ha requerido un tratamiento HIP y, a su vez, se utilizará para piezas «HIPear» piezas fabricadas con FA.
Hiperbaric es el primer fabricante de equipos HIP que incorpora a sus prensas un intercambiador de calor fabricado 100% por FA. La pieza ha sido creada por fusión de lecho de polvo láser (LPBF), con una aleación de la NASA: GRCop-42. Gracias a la libertad de diseño que ofrece la AM y a las propiedades de la aleación GRCop-42, ideal para aplicaciones de alto flujo térmico, se ha desarrollado un intercambiador de calor capaz de alcanzar velocidades máximas de enfriamiento de hasta 1000°C/min.
Existen otros sistemas en el mercado basados en disipadores de calor que absorben energía durante la fase de enfriamiento, pero esto requiere un tiempo de inactividad entre ciclos antes de que este disipador se enfríe de nuevo. El uso de un intercambiador de calor agua/gas supera este problema y, gracias a la fabricación aditiva, su tamaño puede reducirse al mínimo para aumentar el volumen útil de la prensa.
Impacto de la innovación
Los metales suelen requerir varios procesos y tratamientos para conseguir unas propiedades finales que satisfagan las necesidades de las aplicaciones para las que se diseñan. Estos procesos aumentan el coste y el tiempo de fabricación, y cada proceso suele realizarse en lugares distintos, lo que también incrementa los plazos de entrega: alivio de tensiones, solubilización, envejecimiento… y también HIP. Pero, ¿y si pudiéramos combinar estos tratamientos en un solo proceso?
El HIP es un tratamiento esencial en las piezas de FA para cubrir las necesidades más exigentes y gracias a este innovador concepto, podremos combinar varios de estos procesos dentro del mismo equipo y en un solo ciclo. Las ventajas incluyen:
- Ahorro económico y energético: Evita el transporte y desplazamiento entre los distintos equipos y reduce el número de intermediarios. Además, un tratamiento posterior en cada equipo requiere empezar de cero, lo que supone un mayor gasto de energía y recursos.
- Reducción del tiempo de fabricación y los plazos de entrega: La combinación de varios procesos en uno reduce el tiempo de fabricación y, por tanto, un plazo de entrega más rápido.
- I+D: Abre la ventana a una amplia gama de combinaciones posibles, siendo de gran interés para el desarrollo de nuevas aplicaciones.
Materiales empleados
El material utilizado se basa en criterios como una buena conductividad térmica y también buenas propiedades mecánicas. La primera contribuye a mejorar el flujo térmico, reducir los gradientes y las tensiones térmicas inducidas, mientras que las segundas son necesarias para hacer frente a la elevada presión isostática que debe soportar la pieza. Entre los materiales que cumplen estas especificaciones, se ha elegido el GR-42.
Aunque la aleación GRCop-42 fue desarrollada por la NASA en 1987 para entornos agresivos, como las cámaras de combustión de los motores cohete, no fue hasta hace apenas 6 años cuando comenzaron a desarrollarse los parámetros para su uso en FA. Esta aleación a base de cobre con 4 at. % Cr y 2 at. % de Nb tiene una gran resistencia y conductividad, típicas de las aleaciones de cobre, lo que unido al eficiente diseño del intercambiador de calor permite alcanzar velocidades de enfriamiento tan elevadas.