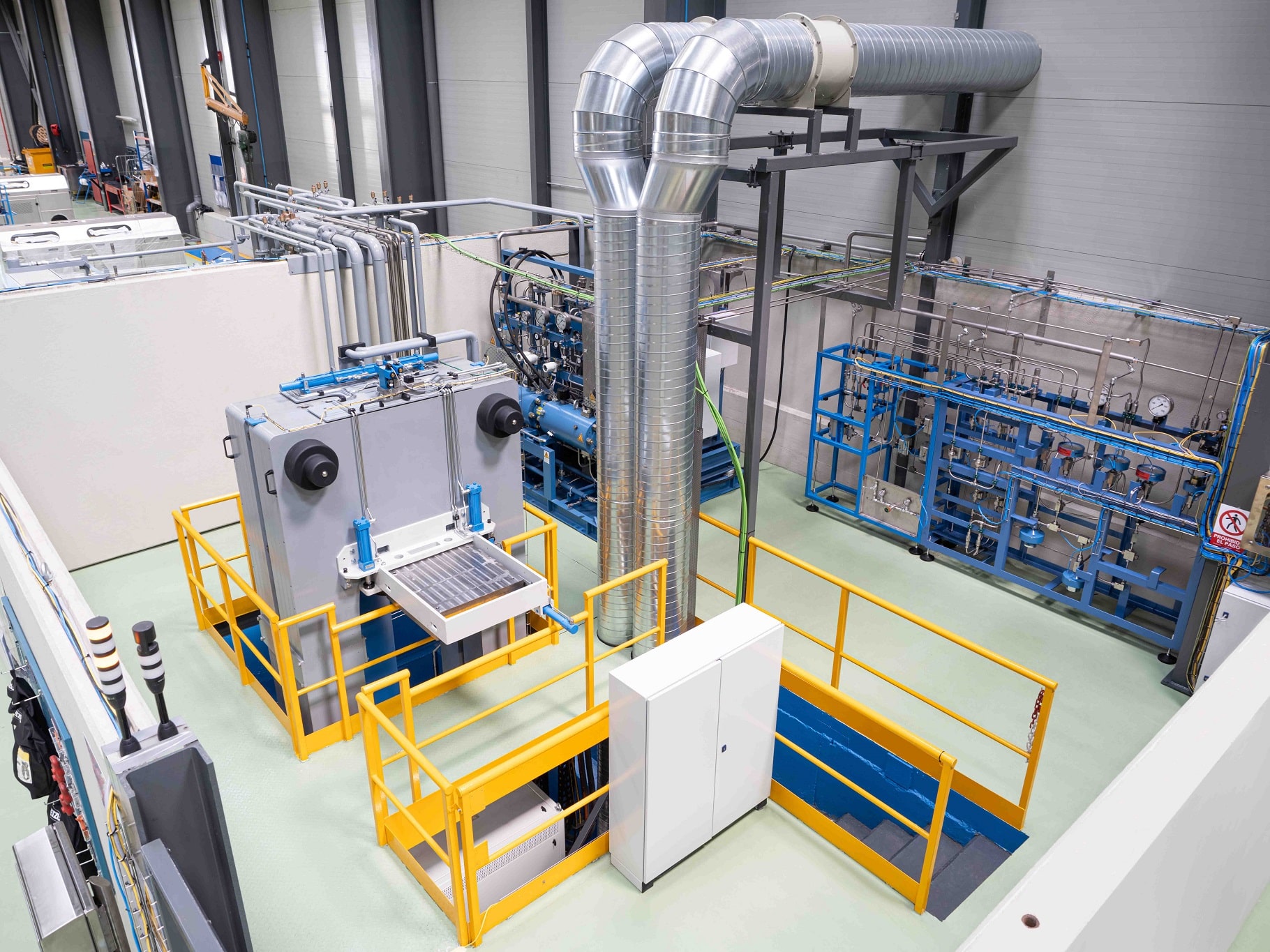
Through Hot Isostatic Pressing (HIP) technology, this case study analyzes how the fatigue life of Titanium alloy TI-6Al-4V has been improved by HIP post-processing at 850ºC / 200 MPa and fast-cooling technology, which can be applied for aerospace or biomedical sector. Good material densification and fatigue properties similar to the reference material were achieved by this HIP post-processing.
Challenge
Hot Isostatic Pressing (HIP) is a thermo-mechanical post-processing technique widely used in additive manufacturing parts to reduce internal defects, such as porosity or internal defects, such as porosity or lack of fusion, which have a great influence on the mechanical and fatigue properties of the material. In this case study that we have carried out jointly with the University of Burgos, we present the effect of a HIP cycle at a pressure of 200 MPa and a temperature of 850ºC during 2 hours, on the fatigue behavior of a Ti-6Al-4V alloy manufactured by SLM, one of the most used alloys of all the alpha-beta titanium alloys.
In addition, the HIP equipment developed by Hiperbaric is associated with a cooling phase called fast-cooling, which is much faster than that obtained by conventional furnace cooling cycles. This HIP cycle achieves a very good densification of the material, reducing the coarsening effects of the microstructure of the material, and obtaining fatigue properties similar to those of the reference material manufactured by conventional methods.
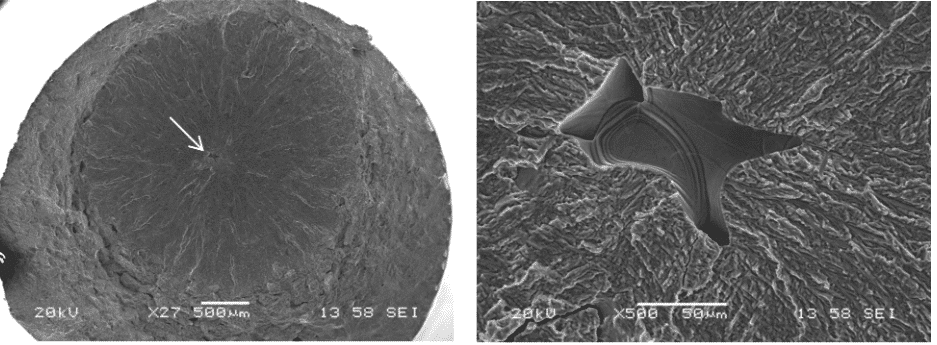
Solution
The conventional HIP cycle for Ti-6Al-4V alloy consists of a thermo-mechanical post-treatment at a pressure of 100-120 MPa and a temperature of 900-920°C for 2 hours in Argon atmosphere, followed by cooling in the furnace chamber.
This cycle is derived from the available HIP technologies, although it has been observed that treatment at elevated temperatures is associated with a thickening of the alpha phase of the microstructure of this material, which has detrimental effects on its fatigue behavior. This has led to try to perform post-treatments at lower temperatures, but with higher pressures to achieve an adequate densification of the material without generating large alterations in its microstructure.
The HIP post-treatment studied in this case consists of reaching a temperature of 850ºC (maintained, as in the conventional cycle, above Ms=800ºC).
above the Ms=800ºC and below the transus=980ºC) and applying a higher pressure of 200 MPa for 2 hours. The cooling process is also carried out by means of a fast-cooling technology, which achieves cooling rates of -138ºC/min for the initial temperature range from 850°C to 600°C (corresponding to a situation between air cooling and oil quenching), and subsequently an average cooling rate of -67ºC/min (similar to air cooling) for the lower temperature range from 600ºC to 400ºC.
This reduces the time the material is subjected to high temperatures, minimizing the phenomenon of thickening of its alpha phase, and improving the properties of the resulting material.
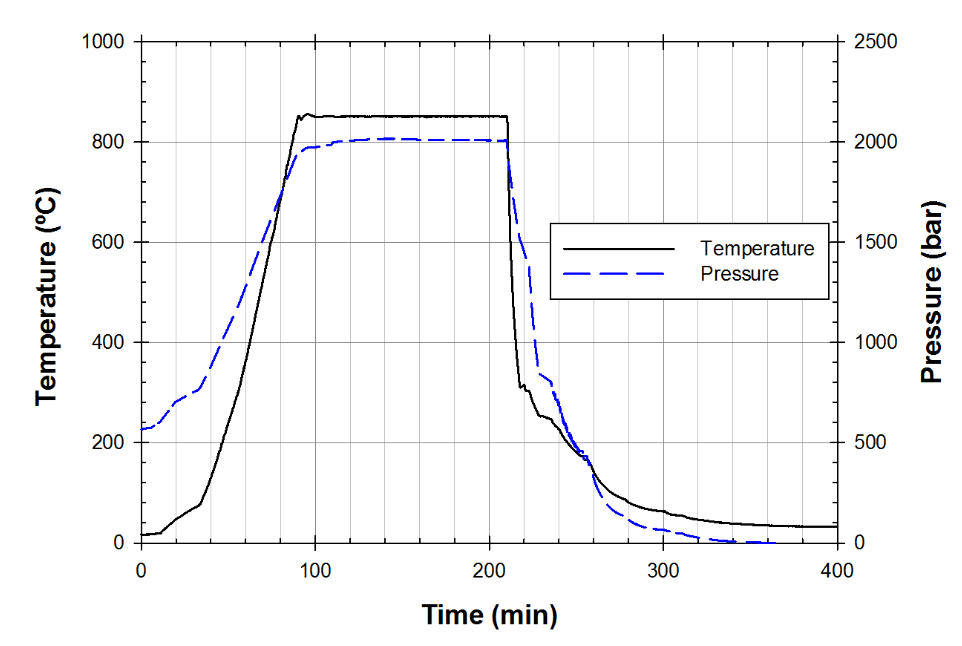
Benefits
Fatigue tests and metallographic analyses have been carried out at the Structural Integrity Laboratory of the University of Burgos. The HIP cycle applied has achieved a good densification of the material and a minimum coarsening of the microstructure.
None of the specimens treated by this HIP cycle started to break from a lack of fusion defect, which indicates that the treatment is effective in eliminating such defects. The fatigue results have been compared with those corresponding to a reference alloy of Ti-6Al-4V Grade 23, obtaining very similar fatigue life values. In addition, the microstructure achieved has not experienced significant thickening of the alpha phase, typically observed in HIP processes at higher temperatures and with conventional furnace cooling.
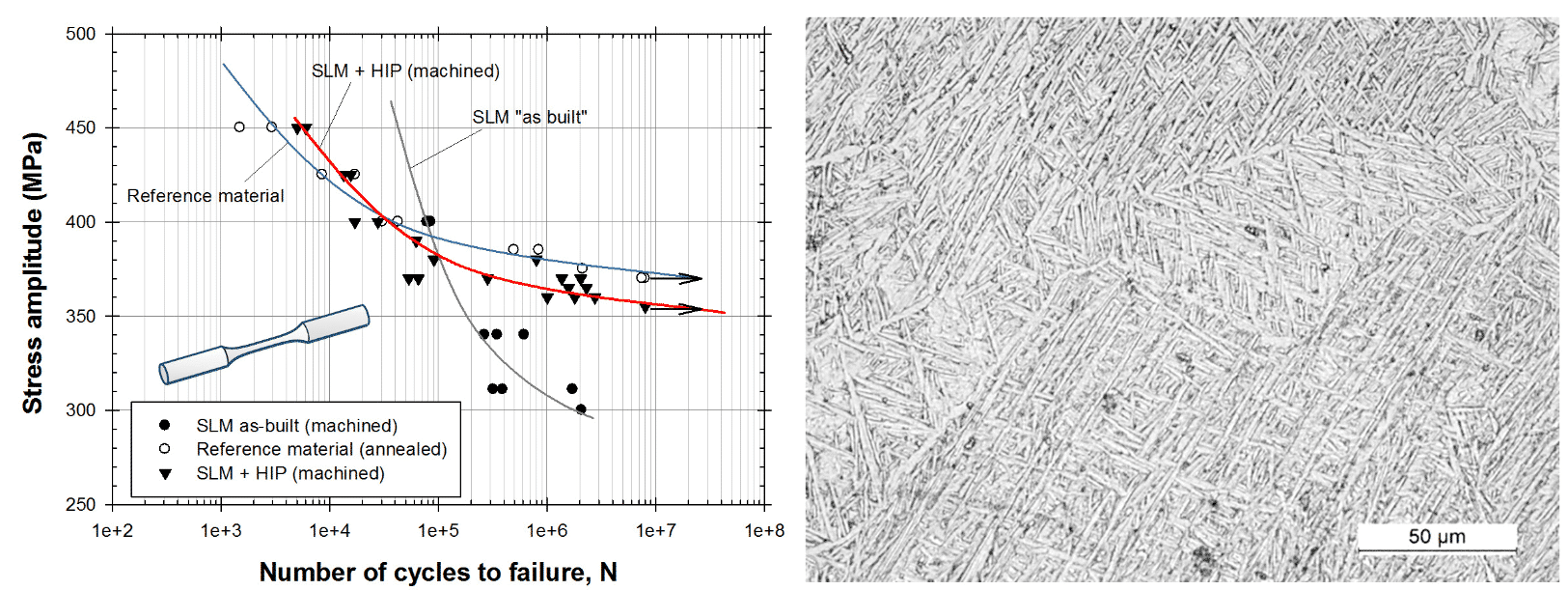
Para más información, no dudes en ponerte en contacto con nosotros y conocer nuestro HIP Innovation Center en Burgos (España). Estaremos encantados de atenderte.
For further information, do not hesitate to contact us and visit our HIP Innovation Center in Burgos (Spain). We will be pleased to assist you.