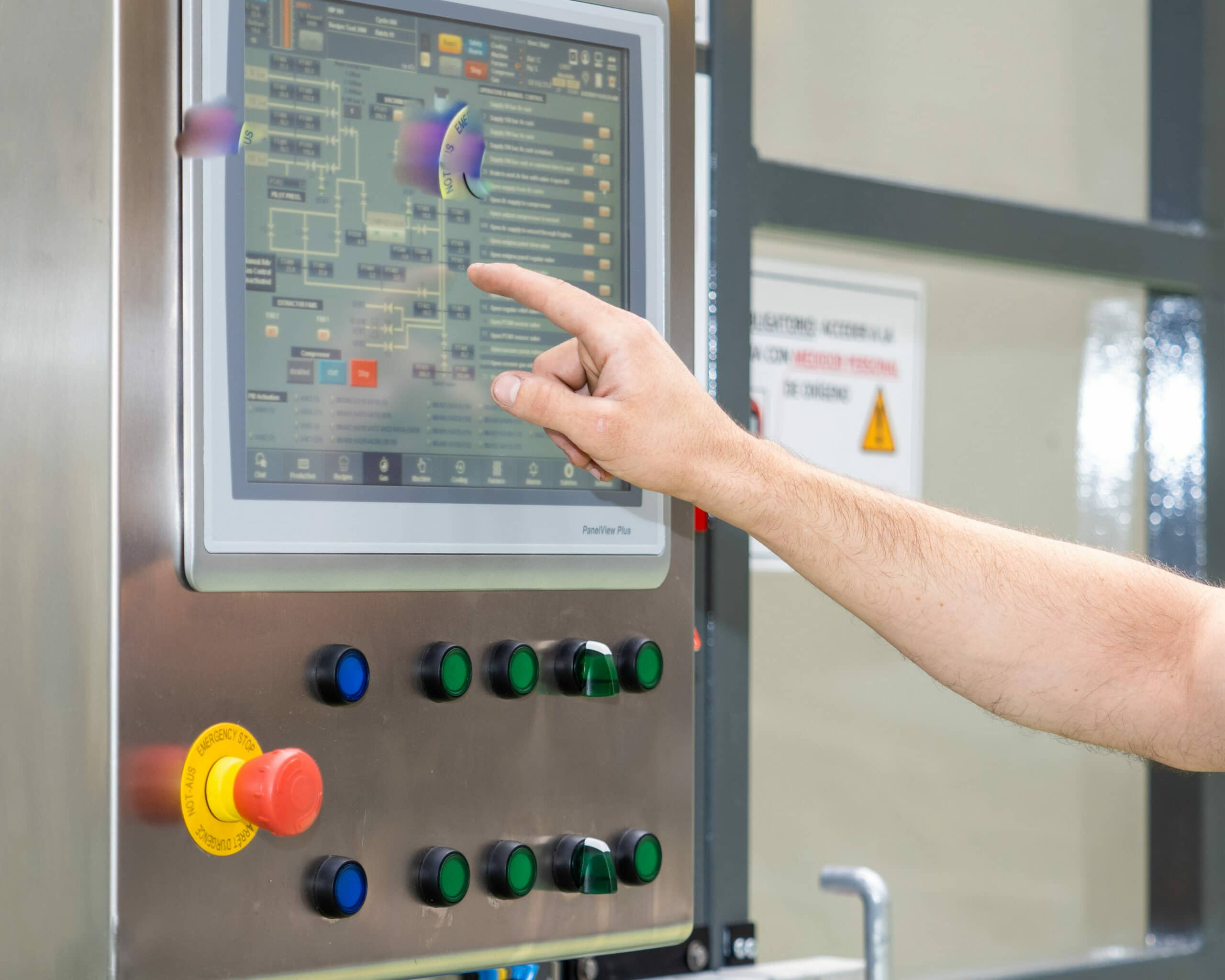
Hiperbaric’s HIP technology provides ease of operation and peace of mind to user thanks to the different systems compromising a HIP machine working smoothly. This article dives into the different systems, what they are in charge of and what Hiperbaric has kept in mind when developing our HIP technology.
HIP technology applies high pressure and heat to components placed inside the vessel. Seeking to improve their mechanical properties amongst other benefits. In order to achieve this, multiple systems with specific functions must work. This article explains the different systems and what their function are.
HIP Press: main components
The press itself is the most important system, it is composed of all the pressure bearing parts. This includes the vessel, the yoke, the plugs and wedges. The vessel itself is constructed using our wire wound technology ensuring maximum safety with a leak before burst design as well as enabling Fast Cooling capabilities to the equipment. The plugs hold the pressure seals as well as all the feedthroughs for all thermocouples, gas and electrical power connections to the inside of the vessel. The vessel and the plugs are always water cooled, this ensures their temperature does not go over a certain safety limit. Finally the pressure held by the vessel and plugs is transmitted through the wedges onto the yoke.
HIP Furnace: up to 2000ºC
The system in charge of providing the heat and keeping a controllable temperature inside the vessel is the furnace. The furnace is placed inside the vessel and carries within, the load that is to be HIP’ed. Furnaces are designed to operate at different temperatures depending on their materials and construction. The most typical are Molybdenum furnaces since they can reach up to 1400ºC which cover most metallic applications, higher temperature furnaces for ceramic applications can be made out of graphite. The furnace also includes all the necessary electrical power supply, sensors and mechanisms to control the temperature and perform Fast Cooling.
Argon in a HIP machine
The pressure medium used in a HIP machine is normally an inhert gas, most typically Argon. The gas management system is dependent on the size and needs of the customer. This system includes both gas storage, the compressor unit, a vaccum pump to eliminate the initial air and all the necessary valves and fittings. Hiperbaric has designed a scalable, efficient, reliable and safe to operate gas management system for its HIP machines. By working closely with our partners at Linde, Air Liquide and Nippon gasses the best solutions can be given.
Refrigeration system and Fast Cooling Technology in HIP machine
The refrigeration system is in charge of keeping things cool and safe during operation. This system guarantees that critical pressure bearing components such as the vessel and plugs that are also exposed to some furnace heat are kept under safe temperatures. Therefore the cooling system ensures cooling is provided to the vessel under any circumstances during operation. This system also plays a big role in our Fast Cooling technology designed to cool down quickly the load, shortening cycles and increasing efficiency and achieve the desired material properties.
Finally the control system managing all the different systems is latest technology with safety always at the heart of all the programming, intuitive to operate interface which provides the user with all the information needed at a quick glance and remote visualization to the press operation. Production control and data logging, as well as integration with other manufacturing devices such as Additive manufacturing printers can be easily so as to implement industry 4.0 production techniques.