HPP, del inglés High Pressure Processing, Conocida también como pascalización, pasteurización hiperbárica o pasteurización en frío es un método de conservación de alimentos y bebidas, no térmico (5ºC – 20ºC) que consigue un aumento de la vida útil, conservando las características del producto fresco y garantizando su seguridad alimentaria.
HPP mantiene las propiedades del producto fresco durante varias semanas o incluso meses
Se basa en la aplicación de altos niveles de presión isostática transmitida por el agua (presión hidrostática) de hasta 6.000 bar /600 MPa /87.000 psi, durante unos segundos o minutos. Esta presión se transmite de forma uniforme e instantánea a todos los puntos del producto, consiguiendo así un efecto equivalente a una pasteurización, pero sin utilizar calor.
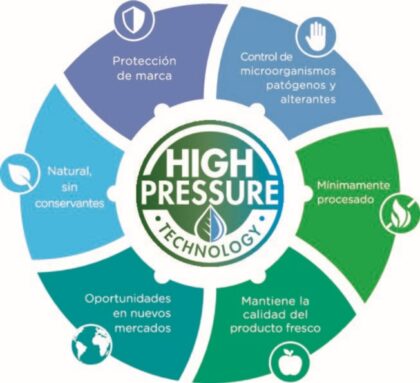
Los consumidores actuales demandan alimentos y bebidas con unas características muy concretas: mayor calidad sensorial y nutricional, ausencia de aditivos y conservantes, listos para el consumo, con una amplia caducidad y 100% seguros.
Mantener la frescura original hasta 3 meses después es posible gracias a la tecnología HPP.
Las técnicas de conservación no térmicas, entre las que están las HPP, han experimentado un boom en los últimos años por adaptarse perfectamente a estas premisas, a diferencia de los tratamientos térmicos y químicos tradicionales. El procesado por altas presiones o pasteurización en frío es el referente industrial de las técnicas de conservación no térmicas entre debido a sus numerosas ventajas.
Ventajas HPP
- Seguridad alimentaria garantizada. HPP inactiva patógenos (Salmonella, E. Coli, Listeria, Vibrio, norovirus, etc.) y los microorganismos responsables del deterioro (bacterias lácticas, coliformes, etc.), cumpliendo los requisitos de las autoridades alimentarias.
- Mínimo procesado. Las características nutricionales y organolépticas de los productos alimenticios se mantienen intactas. Proporciona alimentos mínimamente procesados, conservando la frescura del producto original.
- Nuevas oportunidades de mercado. En el caso de algunos productos, como el jamón curado, es la única tecnología que permite a sus productores entrar en los mercados más exigentes en cuanto a requisitos de seguridad alimentaria, como Japón o Estados Unidos.
- Extensión de la vida útil. Dependiendo del producto, la alta presión en frío prolonga la vida útil entre 3 y 30 veces, al mismo tiempo que garantiza un producto de alta calidad.
- Mejora de las operaciones de la cadena de suministro. Gracias a la prolongación de la vida útil, es posible optimizar la planificación de la producción y las operaciones.
- Reducir el desperdicio de alimentos.HPP evita el desperdicio de alimentos en el supermercado y en el hogar, gracias a su vida útil prolongada.
- Etiqueta limpia. La alta presión permite reducir drásticamente o eliminar el uso de conservantes o aditivos en los alimentos.
- Amplia gama de aplicaciones. Puede aplicarse en una gran variedad de aplicaciones alimentarias. Descubra la gama de aplicaciones en nuestra página web.
- Versátil. HPP puede aplicarse sobre productos envasados (In-Pack), evitando la contaminación cruzada; o directamente sobre líquidos a granel para una mayor productividad y sin limitaciones de envasado (In-Bulk).
- Productos innovadores. Las altas presiones permiten a los equipos de I+D desarrollar productos innovadores para el consumidor y abrir nuevos nichos de mercado.
- Aumenta el rendimiento de extracción de la carne de marisco. A 3.000 bar de presión, se utiliza para abrir moluscos bivalvos y extraer la carne de los crustáceos, aumentando la eficiencia y minimizando la mano de obra.
- Ecológica. Requiere electricidad y agua, ambas se reciclan en el proceso.
--> Se debe tener en cuenta que los productos HPP se han de conservar en refrigeración para obtener todas estas ventajas
Desventajas HPP
- No inactiva esporas. Para conseguirlo sería necesario combinar presión (6.000 bar) y temperatura (>100ºC).
- Por definición la esterilización es una tecnología capaz de inactivar esporas. Clásicamente la industria alimentaria utiliza altas temperaturas, consiguiendo un alimento estable a temperatura ambiente durante meses o años. El inconveniente es que las altas temperaturas que se aplican alteran las propiedades nutricionales y organolépticas del alimento o la bebida.
- Actualmente se investiga la combinación de diferentes tecnologías barrera, incluyendo la HPP, que aseguren la eliminación de esporas y respeten las características del alimento fresco.
- No funciona con producto seco. Para asegurar su efectividad, es recomendable que los productos tengan una Aw (actividad de agua) superior a 0,8.
- En algunos casos es posible desarrollar productos alternativos o incluso modificar ciertos aspectos como formulación o acidez para conseguir que el proceso sea eficiente, aunque la Aw sea inferior a 0,8.
- Posibles cambios de textura o color. Las macromoléculas como proteínas y polisacáridos cambian su estructura tridimensional con la alta presión. Esto puede generar cambios de textura y color de algunos productos (como carne, huevos o pescado). Sin embargo no se produce alteración alguna en la composición de los mismos o en su sabor.
- Este efecto es prácticamente imperceptible en carnes crudas marinadas, escabechadas y similares pues pueden contar con colorantes naturales que lo mitigan.
- En la aplicación de HPP para la extracción de carne de mariscos la estructura de las proteínas no se altera ya que se utilizan presiones más bajas (aprox. 3.000 bar /300 MPa /43.000 psi).
Tecnología HPTP para productos estables a temperatura ambiente
Mientras los productos HPP se deben mantener en condiciones de refrigeración, la tecnología alta presión alta temperatura (HPTP) permite desarrollar productos estables a temperatura ambiente.
Preguntas frecuentes
1. ¿Cuáles son los requisitos para los alimentos HPP?
La tecnología de procesado por altas presiones (HPP) es un proceso hidrostático que se basa en la compresión del agua para transmitir la presión. Por tanto, se recomienda que los alimentos tengan una actividad de agua (aw) superior a 0,96 para maximizar el efecto letal sobre los microorganismos.
Es decir, HPP es más eficaz en productos de alta aw porque el producto tendrá un mayor contenido de agua libre disponible para transmitir la presión, lo que conducirá a una mayor inactivación microbiana y una vida útil más prolongada.
Es importante recordar que el contenido de humedad es diferente de aw. Un producto puede tener un alto contenido de humedad y una aw baja.
2. ¿Cuáles son las principales aplicaciones de HPP?
HPP se ha extendido en una amplia gama de alimentos y bebidas: desde las aplicaciones de HPP más consolidadas, como zumos y bebidas, carne y productos de aguacate, hasta las últimas tendencias, como platos preparados (RTE), dips vegetales, alimentación infantil y alimentación para mascotas.
Observe el siguiente diagrama (actualizado en 2020) con la distribución mundial de máquinas HPP industriales por sectores alimentarios:
2.1 ¿Qué alimentos no se pueden procesar por HPP?
Para disfrutar de las ventajas de HPP, los productos deben tener un alto valor de actividad de agua para maximizar el efecto letal sobre los microorganismos. Además, esta tecnología puede provocar cambios en la textura de algunos ingredientes en ausencia de un líquido o aderezo que los rodee. Por tanto, no se recomienda aplicar HPP a especias, polvos, frutos secos o frutas deshidratadas, cereales, frutas enteras, hojas de hortalizas y ensaladas de hojas, pan y bollería y otros ingredientes que encajen en esta descripción.
Para HPP, los alimentos se deben descongelar, ya que la tecnología no funciona para alimentos congelados. Los cambios de volumen debidos a la compresión / descompresión alteran la membrana celular de los microorganismos y la estabilidad de componentes celulares clave como enzimas o proteínas. El hielo es menos compresible que el agua líquida, lo que protege a los microorganismos. También es posible que los microorganismos adaptados a ambientes fríos / congelados presenten una membrana celular más flexible y generen solutos para estabilizar componentes clave en ambientes fríos, que también pueden conferir resistencia a la presión.
3. ¿El procesado HPP afecta la composición de los alimentos o sus propiedades sensoriales?
HPP tiene efectos mínimos sobre las vitaminas, antioxidantes, otros micronutrientes o compuestos responsables de sabor y aroma. Además, ayuda a retener mejor estos compuestos en comparación con los procesos térmicos convencionales. Esto se debe a que HPP no rompe los enlaces covalentes y solo afecta las interacciones moleculares no covalentes más débiles como son los enlaces de hidrógeno, las fuerzas de van der Waals, interacciones electrostáticas e hidrofóbicas; estas interacciones son responsables de la estabilización de la estructura secundaria y terciaria de las proteínas, carbohidratos complejos o estructuras biológicas como las bicapas lipídicas de las membranas celulares.
4. ¿Cuáles son las ventajas de HPP frente a otras tecnologías no térmicas?
Entre las tecnologías de procesamiento de alimentos no térmicas (por ejemplo, campos eléctricos pulsados, radiación ultravioleta, radiación ionizante o filtración por membranas), HPP es la más conocida y utilizada en los EE. UU., Europa, Asia y Oceanía. A diferencia de las otras tecnologías no térmicas, HPP es completamente no térmica y se utiliza para alimentos líquidos y sólidos. Además, dada su aplicación posterior al envasado, permite eliminar aditivos y obtener un producto de etiqueta limpia.
5. ¿Es necesario envasar los alimentos para HPP?
HPP es un proceso "In-pack", lo que significa que los productos se deben envasar cuando se procesan, generalmente en su envase final. Los materiales de envasado deben ser flexibles (para resistir la compresión), elásticos (para recuperar su forma original después de la descompresión) e impermeables (ya que estarán sumergidos en agua). Estas consideraciones hacen que los polímeros plásticos sean la opción más versátil.
Hiperbaric ha desarrollado la tecnología "In-Bulk", una innovación revolucionaria que permite procesar líquidos sin envasar, es decir, a granel antes del envasado. Esto abre la gama de opciones de envasado que se pueden utilizar, como bricks de cartón, botellas de vidrio y latas de metal.
6. ¿Es HPP realmente un proceso no térmico?
HPP es una tecnología no térmica ya que la temperatura durante el proceso es inferior a 40 ° C / 100 ° F.
Aun así, es cierto que durante este proceso se produce un ligero aumento de temperatura dentro de la vasija. Este fenómeno se denomina calentamiento adiabático y está asociado con la compresión del agua. En el caso particular del agua, la temperatura aumenta alrededor de 2-3 ° C por cada 100 MPa / 1000 bar / 15,000 psi de presión aplicada. Por lo tanto, teniendo en cuenta la presión máxima de funcionamiento de los equipos industriales (600 MPa / 6000 bar / 87000 psi), la temperatura de los alimentos / agua solo aumentaría 18 ° C / 64 ° F durante el tiempo de mantenimiento, que normalmente es de 2 a 6 min. . Además, el calentamiento adiabático es completamente reversible al liberar la presión y el producto vuelve a la temperatura de antes del ciclo HPP.
7. ¿Puede HPP reemplazar la pasterización o esterilización térmica?
La tecnología HPP permite la inactivación de microorganismos vegetativos, parásitos y virus, aplicando de 400 MPa (4000 bar / 58,000 psi) a 600 MPa (6000 bar / 87,000 psi), durante unos segundos hasta alrededor de 6 minutos. Sin embargo, al igual que con la pasterización térmica, algunos microorganismos resistentes a la presión permanecen viables en el producto después del procesamiento, así como las esporas bacterianas que no son inactivadas por HPP. Además, HPP no inactiva por completo la mayoría de las enzimas, por lo que la HPP no permite el desarrollo de alimentos estables comercializados a temperatura ambiente. Por otro lado, los productos tratados con HPP retienen mejor las propiedades sensoriales y nutricionales en comparación con el proceso térmico convencional.
En conclusión, la tecnología HPP ofrece productos “frescos” con resultados microbiológicos similares a los de la pasterización térmica; sin embargo, no es una técnica de esterilización.
8. ¿Puede HPP inactivar los microorganismos formadores de esporas?
Las esporas bacterianas son muy resistentes a la alta presión. De hecho, a la presión máxima de funcionamiento de los equipos industriales (600 MPa / 6000 bar / 87 000 psi), las esporas no se inactivan. Sin embargo, teniendo en cuenta otros obstáculos, como un pH bajo (<4,6) y el almacenamiento refrigerado (4-6 °C), se podría mantener el producto dentro de márgenes seguros al evitar la germinación y el crecimiento de esporas durante el almacenamiento de alimentos. La combinación de alta presión con niveles moderados o altos de temperatura en un proceso conocido como esterilización térmica asistida por presión (PATS) o procesamiento térmico asistido por presión (PATP) podría ser una buena estrategia para lograr la inactivación de esporas y garantizar la seguridad alimentaria con un impacto en la calidad nutricional y sensorial más leve. No obstante, esta tecnología aún no se encuentra en un nivel de aplicación industrial.
9. ¿El procesado HPP afecta la actividad enzimática?
HPP inactiva los microorganismos patógenos y alterantes, así como algunas enzimas tisulares. Los efectos de HPP sobre las enzimas dependen de múltiples factores, incluido el tipo de enzima, las condiciones de procesamiento y las características de la matriz alimentaria. Por lo tanto, la mayoría de las enzimas solo se inactivarán parcialmente y permanecerán activas durante el almacenamiento bajo refrigeración. Si se desea, algunas estrategias para aumentar la inactivación enzimática es combinar HPP con otros obstáculos, como bajar el pH, agregar antioxidantes o escaldar las materias primas antes de HPP. Sin embargo, en algunos casos, esta inactivación parcial de las enzimas puede ser un fenómeno deseable, abriendo la posibilidad de desarrollar nuevos productos con diferente textura.
10. ¿Se pueden almacenar los alimentos HPP a temperatura ambiente?
Se recomienda almacenar los productos HPP en refrigeración (4-6 °C), ya que la cadena de frío actuará como un obstáculo para ralentizar el crecimiento microbiano, la actividad enzimática y las reacciones químicas indeseables durante la vida útil.
Esto resulta fácil de comprender, ya que algunos microorganismos pueden ser resistentes a la alta presión y recuperarse durante su vida útil. Lo mismo ocurre con las enzimas que no están completamente inactivadas: si se mantiene la cadena de frío, su actividad residual será menor. Asimismo, las reacciones químicas que no están relacionadas con HPP pero que conducen a cambios sensoriales o nutricionales, ocurren a tasas más rápidas bajo abuso de temperatura (10 °C) o niveles de temperatura ambiente.
11. ¿HPP garantiza la seguridad alimentaria?
Definitivamente. HPP garantiza la seguridad alimentaria y logra una mayor vida útil, a la vez que mantiene los atributos óptimos de los productos frescos. Además, HPP está altamente reconocida por numerosas autoridades de seguridad alimentaria (FDA, EFSA…). La seguridad alimentaria se logra inactivando los patógenos vegetativos, incluidos bacterias, virus, mohos, levaduras y parásitos mediante la aplicación de 400 MPa (4000 bar / 58,000 psi) a 600 MPa (6000 bar / 87,000 psi), durante unos segundos a alrededor de 6 minutos.
Sin embargo, dado que existen algunos microorganismos y enzimas resistentes a la presión, e incluso a la presión máxima de los equipos industriales (600 MPa / 6000 bar / 87,000 psi), las esporas no se inactivan, deben considerarse otros obstáculos. Por ejemplo, un pH bajo (<4,6), la presencia de antimicrobianos naturales y el almacenamiento refrigerado (4-6 °C) podrían ayudar a garantizar aún más la seguridad alimentaria junto con la tecnología HPP.
Regulación y normativa de los productos HPP
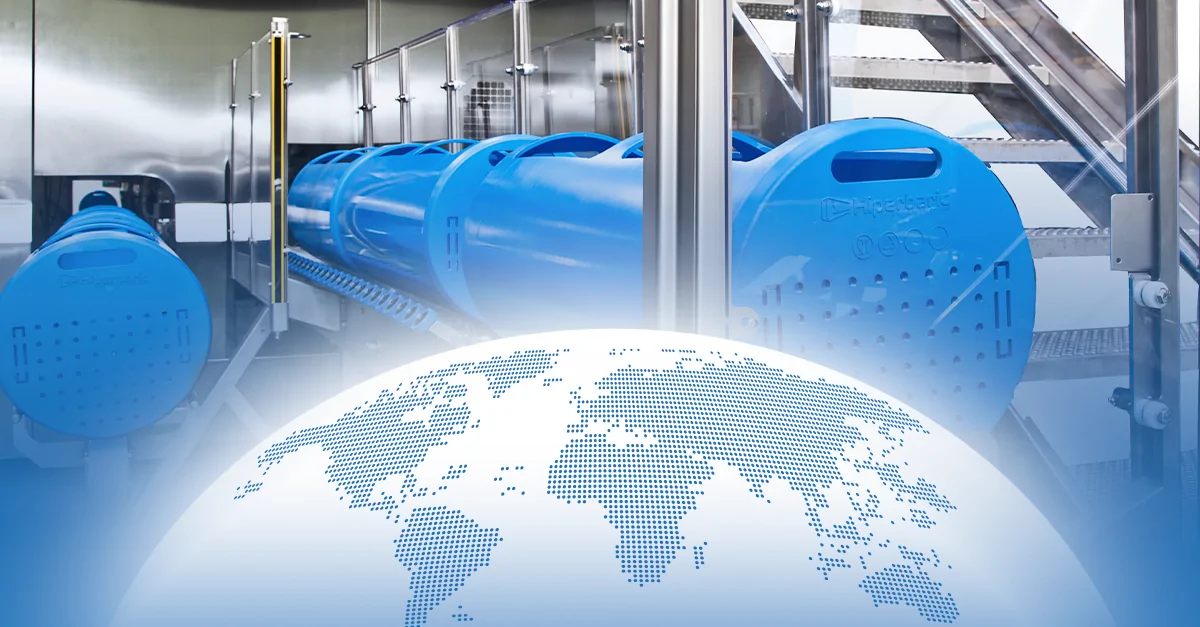
Normativas alrededor del mundo
El procesado a altas presiones se utiliza comercialmente desde hace más de 20 años en todo el mundo. En este tiempo nunca se han registrado retiradas ni problemas de seguridad asociados a los productos HPP.
La ausencia de una autorización global para el procesado por altas presiones (HPP) da lugar a diferentes enfoques para integrar el HPP en los marcos normativos de las distintas regiones. A continuación, detallamos los requisitos para tres regiones principales. Haga clic en su región para obtener más información.
Miembros de algunas de las Asociaciones e Instituciones más prestigiosas del mundo
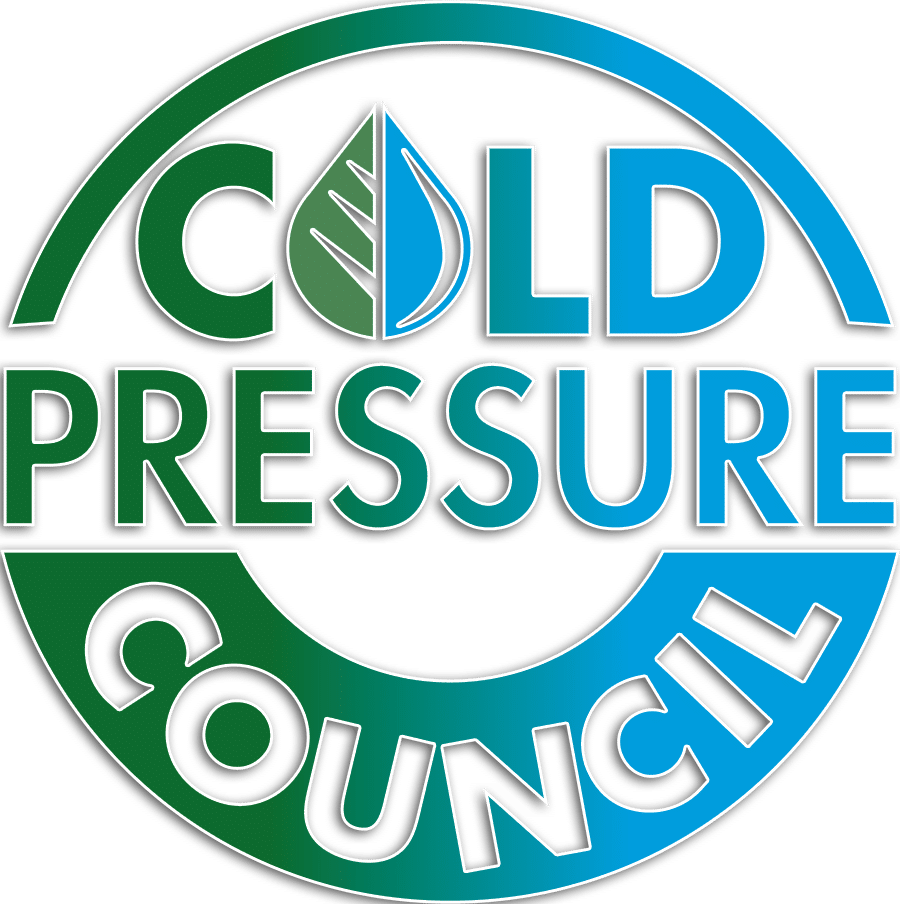
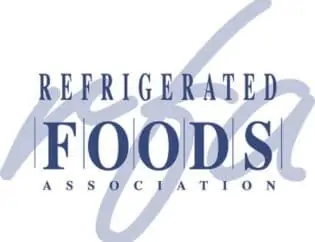
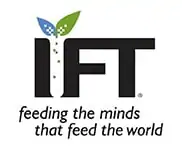
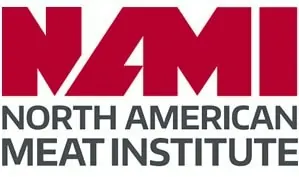
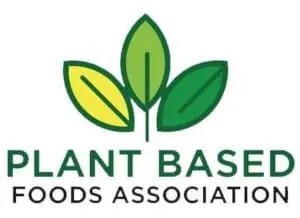
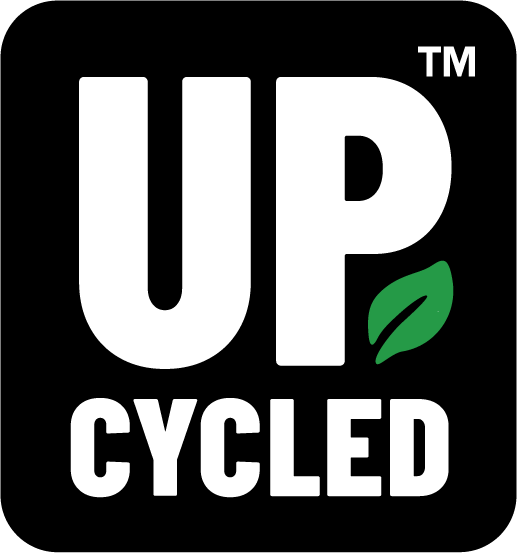
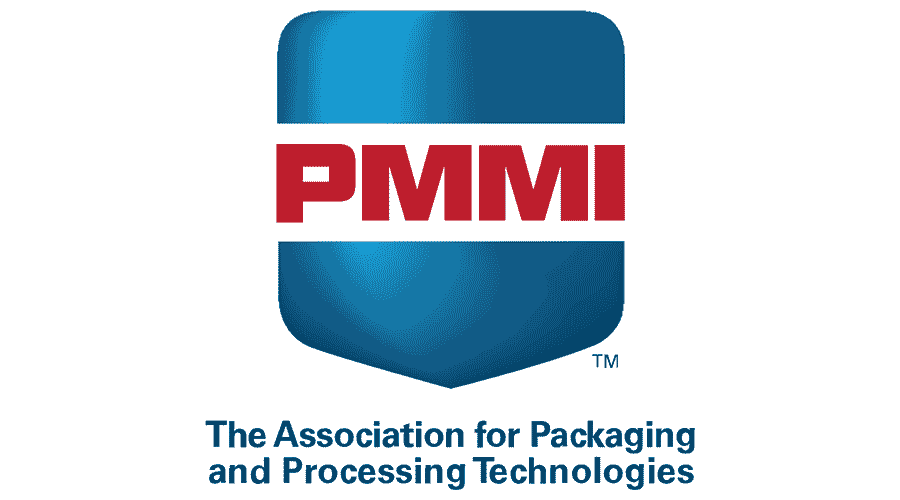
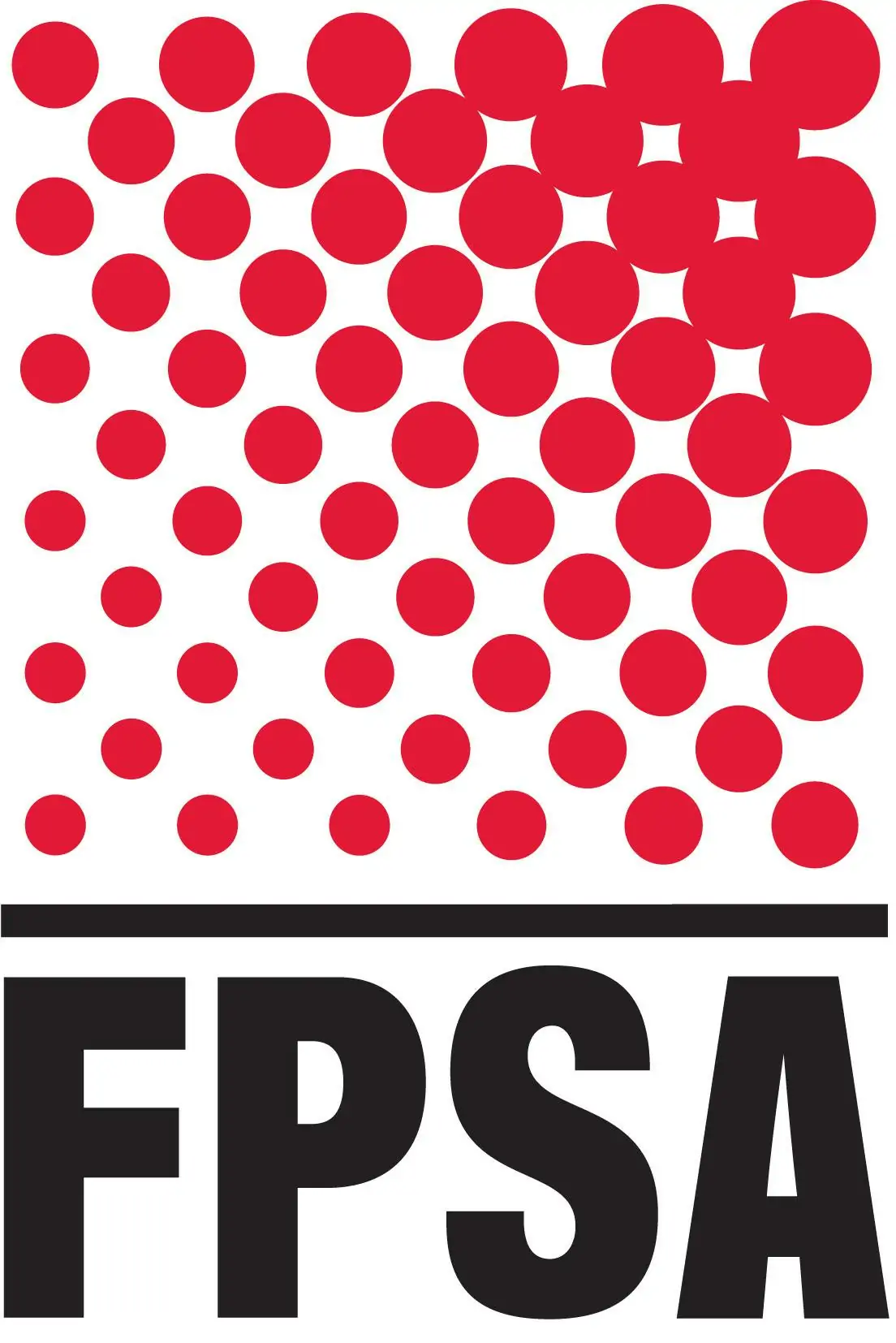